آنچه باید در مورد نسوزهای تاندیش بدانیم
آنچه باید در مورد نسوزهای تاندیش بدانیم….
1 -مقدمه
تاندیش تجهیزی است که در ریختهگری فلزات استفاده می شود و به صورت یک محفظه باز و پهنی با یک یا چند سوراخ در کف آن است. این تجهیز جهت تغذیه مذاب فلز به داخل قالب شمش استفاده می شود تا از پاشیده شدن مذاب جلوگیری شده و جریان ملایمتری ایجاد شود.
2-عملکرد و اهمیت تاندیش در ریختهگری پیوسته
در ریختهگری پیوسته، تاندیش یک محفظه آسترکاری شده با مواد نسوز و دربردارنده فولاد مذاب با حداقل اتلاف حرارتی است. انتخاب نسوزها در تاندیش به دلایلی از جمله سکوئنس ریخته گری طولانی تر، زمان آماده سازی مجدد سریعتر تاندیش و تمیزی فولاد حائز اهمیت است. از جمله مواد نسوز مورد استفاده در تاندیش، آجرهای شاموتی میباشد. آجرهای آلومینا بالا برای آمادهسازی مجدد تاندیش به صورت گرم مناسب بوده و در آستر تاندیش نیز به طور معمول از مخلوط Al2O3-SiO2-MgO با روش نصب گانینگ استفاده می شود. تاندیش ها مجهز به صفحات حائل (weir) و سد (dam) از جنس بردهای MgO یا آجرهای آلومینایی هستند. فولاد مذاب از طریق نازل تاندیش غوطه ور (SEN) به درون تیوب مسی(در ماشین ریختهگری پیوسته) تغذیه میشود. این نازلها که در فولاد مذاب غوطهور هستند باید در برابر خوردگی و پوسته شدن و همچنین گرفتگی نازل نیز مقاوم باشند. از این رو، از نازلهایی با جنس آلومینا – گرافیت-سیلیس ذوبی تهیه شده تحت فشار ایزواستاتیک استفاده می شود.
ماشین ریختهگری در حین تعویض پاتیلها، از طریق تاندیش تغذیه میشود. از این رو تاندیش به عنوان تغذیه کننده فلز داغ و ملایم کننده جریان ذوب )جلوگیری از ریخته گری قطعات با نقص هایی مانند ترک و حباب( عمل کرده، تغذیه فلز به قالبها را تنظیم کرده و فلز را تمیز میکند. بقایای فلزی باقی مانده در داخل تاندیش به عنوان ته تاندیش شناخته می شود و معمولا لازم است با استفاده از روش های مکانیکی خارج شوند. معمولا ضایعات بازیافتی با این روش، مجددا در فرآیند فولادسازی استفاده می شوند. تاندیشها در ابعاد و مدل های مختلف موجود بوده و شرکت ها ی متعددی این تجهیزات را به همراه لوازم جانبی آن تولید می کنند. لازم به ذکر است سطح مذاب درون تاندیش در تماس مستقیم با هوا بوده که میتواند منجر به ایجاد واکنشهای ناخواسته، تغییر ترکیب مذاب فلز و نهایتا افت کیفیت محصول نهایی شود. از این رو لازم است این تغییرات در تمام مراحل ریختهگری به دقت کنترل گردد.
3-بخشهای مختلف تاندیش
1 -تیوب چنجر با استوپر
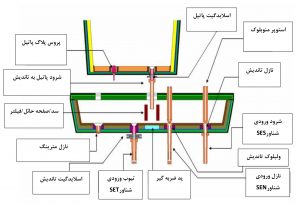
نسوزکاری تاندیش_پاترون
2 -اسالیدگیت تاندیش
3 -اسالیدگیت تاندیش با تیوب چنجر
5 -نازل چنجر
6 -سیستم کنترل استوپر
7 -اتوماسیون سیستم جهانی
4-نسوزکاری تاندیش
طراحی آستر نسوز و کیفیت دیرگدازهای مورد استفاده، تأثیر زیادی بر پارامترهای عملیاتی مانند نیاز به سوپرهیت، سکوئنس طولانی تر، سرعت دستگاه و نهایتا کارکرد ماشین ریخته گری پیوسته دارد. معمولا انتظار میرود در عملیات ریختهگری پیوسته، نسوزهای مصرفی در تاند یش نیازهایی از جمله اتلاف حرارتی پایین حتی در ریخته گری های متوالی طولانی، عمر طولانی و زمان تعمیر کمتر برای کاهش هزینه نسوزها، سیستم گرمایش ساده و قابل اعتماد، اسلایدگیت پاتیل پروس پالگ پاتیل استوپر منوبلوک نازل تاندیش شرود پاتیل به تاندیش سد/صفحه حائل/فیلترنازل مترینگ تیوب ورودی اسالیدگیت تاندیش شناورSET نازل ورودی پد ضربه گیر شناورSEN ولبلوک تاندیش شرود ورودی شناورSES جزوه آموزشی آشنایی با تاندیش شماره مدرک: 10-E-53
در فولادسازی نیاز به نیروی کار کمتر ، تهتاندیش زدایی آسان و تولید ضایعات کمتر، یکپارچگ ی بهتر برای تمیزی فوالد ، نصب ساده، سریع و سازگار با محیط زیست را برآورده سازد.
نسوزکاری تاندیش معمولا در قالب دو لایه ایمنی و لایه کاری انجام می شود. در لایه ایمنی که لایه دائمی نیز نامیده میشود می توان از جرمهای ریختنی کم س یمان و فوق کم سیمان، جرمهای قابل پمپاژ و شاتکریت، جرمهای قابل اسپری و سیستمهای انکر استفاده کرد. هر کدام از این لایه های ایمنی از لحاظ هزینه، شرایط کارکرد (انتقال حرارت،استحکام و عمر) و سهولت نصب دارای شرایط متفاوتی هستند که با توجه به شرایط تولید(زمان ریخته گری، دمای ریخته گری، …)باید انتخاب شوند.لایه بعدی که به عنوان لایه کاری اعمال میشود می تواند از جنس نسوزهای سیلیسی یا منیزیتی باشد. در تاندیش های بزرگ و تولید بالا از جرم های ریختنی مونولیتیک برای کاهش هزینه، نیروی کاری و نیز عمر بالاتر استفاده می شود.
5-انواع نسوزهای مورد استفاده در نسوزکاری تاندیش روش های مختلفی جهت آسترکاری تاندیش وجو د دارد که به طور عمده به 5 دسته طبقه بندی میشود:
1 .آستر آجری
2 .آستر با قابلیت گانینگ
3 .آستر صفحه ای (صفحات)
4 .آستر با قابلیت اسپری (پاشش)
5 .آستر خشک (تشکیل در محل)
5-1-آستر آجری
با آغاز تجاریسازی فرایند ریختهگری پیوسته در حدود دهه 1960 ،در ابتدا همان مفهوم آسترکشی با آجر نسوز که در سایر مخازن حاوی فلز استفاده می شد، برای آسترهای تاندیش ریختهگری پیوسته نیز اعمال شد. این آسترهای آجری معموال از نوع آلومینا بالا بودند که در تماس مستقیم با فولادمذاب استفاده می شدند .
مزایا:
• ریسک پایین جذب هیدروژن توسط فولاد مذاب
• نبود ماسه
• عدم نیاز به سرمایه گذاری در تجهیزات
معایب:
• نیاز به کیورینگ شدید
• نیاز به نیروی کار بیشتر
• عایق بندی ضعیف
• افت دما در مرحله آخر عملیات ریختهگر ی به دلیل رسانایی حرارتی بالا آستر آجری که منجر به اتلاف حرارت فلز شده و بر پارامترهای متالورژیکی تأثیر می گذارد.
• سردکار نبودن
• ته تاندیش زدایی دشوار
• نیاز به اتصاالت
• زمان طولانی آمادهسازی تاندیش
وجود مشکلات بیش از حد در این روش، باعث شد که برخی از افراد به جرمهای قابل اعمال به روش ماله کشی و سپس گانینگ) با وجود اضافه شدن هزینه ها) روی آورند.
5-2-آسترهای قابل اعمال با روش گانینگ
گفته می شود که این نوع آسترها جهت غلبه بر برخی از مشکالت آسترهای آجری، به صورت تجار ی در ژاپن راه انداز ی شدند. این آسترها در ابتدا بر پایه آلومینو سیلیکات بودند و لی بعداً جهت بهبود عملیات متالورژیکی، به پایه منیز یتی تبد یلشدند. معرفی این پوششها اگرچه ساختاری یکپارچه و بدون اتصاالت را ارائه داد و ته تاندیش زدایی را نسبتاً بهبود بخشید، اما به دلیل تراکم نسبتاً باالی آسترهای گانینگ ، در زمانهای پیش گرم یا میزان اتالف حرارتی بهبودی حاصل نشد.
همچنین تمایل به ایجاد ترک و پوسته ای شدن آسترها در حین پیش گرمایش سریع نیز از جمله عواملی بود که مانع استفاده از آسترهای گانینگ در حالتی که تاندیش سرد بود می شد .
مزایا:
• ریسک پایین جذب هیدروژن توسط فولاد مذاب
• نبود ماسه
• عدم نیاز به اتصالات
• نیروی کار کمتر
• نصب نسبتا آسان در زمان کمتر
• تاندیش زدایی نسبتاً آسان تر
معایب:
• نیاز به کیورینگ شدید
• اتلاف زیاد به دلیل تلفات برگشتی
• عایق بندی ضعیف
• سردکار نبودن
• پایداری حرارتی پایین
• مشکلات گرد و غبار
• مصرف انرژی بالا
• هزینه های بالا
• سرمایه گذاری در تجهیزات
اواسط دهه 1970 ،شاهد معرفی نوع جد ید ی از آسترهای مقاوم به سایش در تاندیشها بودیم که شامل سیستم های صفحه ای شامل برد هاینسوز پیش ساخته با چگالی کم و هدایت حرارتی کم بودند. ته تاندیش زدایی آسان، عدم نیاز به سرمایه گذاری در تجهیزات و هزینه کم انواع سیلیس موجب محبوبیت این آسترها در بین بسیاری از فولادسازان گشت. گارنکس FOSECO در این مدت به نامی شناخته شده در محافل ریخته گری پیوسته هند تبدیل شد. لازم به ذکر است در ابتدا از بردهای سیلیسی استفاده میشد که فقط سردکار بودند) امروزه نیز معمولا برای فولاد های ساده کربنی، صفحات پایه سیلیسی استفاده می شوند زیرا تخلخل به عنوان عامل بازدارنده شدید مورد توجه نیست(.در اواسط دهه 1980 برای برآوردن نیاز پیش گرمایش و روش کار گرم جهت تولید فوالدهای با کیفیت باال، بردهای منیزیتی نیز معرفی شدند. از جمله مزایا و معایب این صفحات می توان به موارد زیر اشاره کرد:
مزایا:
• ریسک پایین جذب هیدروژن (هنگامی که گرم است)
• شکل یکنواخت آستر و مونتاژ آسان
• عدم نیاز به کیورینگ
• سردکار بودن
• تهتاندیش زدایی آسان
• مصرف انرژی کمتر
• عدم سرمایه گذاری در تجهیزات
• کم هزینه بودن (برد سیلیسی)
• افزایش عمر تاندیش، عمر الیه ایمنی و آجرها
• صرفه جویی در مصرف نسوز و عدم نیاز به استفاده از آجرهای با کیفیت بسیار بالا
• کاهش نیاز به بتونه کاری یا تعمیر آجر های الیه ایمنی
• کاهش کندگی و شناور شدن در تاندیش
• کاهش لنس اکسیژن برای از بین بردن گیرکردن تکه های تاندیش در منفذ نازل
• کاهش میزان سرمایش مذاب به علت شرایط مناسب ریختهگری
• کاهش میزان افت دما به علت میزان بیشتر عایق بودن
معایب:
• اتصاالت
• برگشت ماسه (در ذوب)
• ریسک جذب هیدروژن )در زمانی که سرد است(
• نیاز به نیروی انسانی زیاد
• مشکل جابجایی/شکسته شدن
• هزینه باال ) بردهای منیزیتی(
استفاده از صفحات نسوز در کشورهایی که هز ینه نیروی کار کم و فناوری های کاربردی به راحت ی در دسترس نی ستند،
محبوب است.
5-3-1-اجزا و ترکیب شیمایی صفحه تاندیش
جدول زیر نشان دهنده ترکیب شیمایی صفحه تاندیش(گارنکس)، پد و مالت مورد استفاده در آن است.
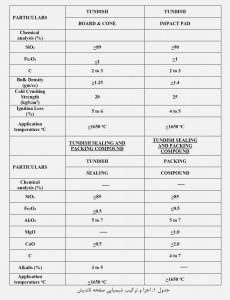
اجزا و ترکیب شیمیایی صفحه تاندیش
5-3-2-نقشه تاندیش و صفحات تولید شده برای آنها
در ادامه نقشه تاندیش و صفحات تولید شده از آنها آورده شده است.
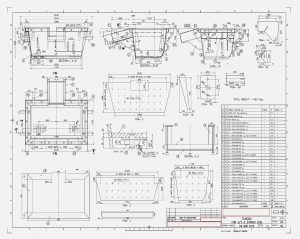
نقشه تاندیش و صفحات تولیدشده
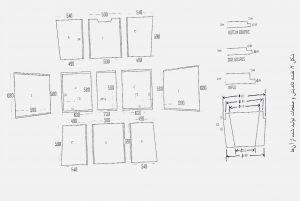
نقشه تاندیش و صفحات تولید شده آنها
5-4-آسترهای قابل اسپری (پاشش)
به دلیل وجود برخی از مشکلات در سیستمهای پیشین و همچنین پیشرفت در طراحی ماشین آلات و تکنولوژی در کشورهای پیشرفته، سیستم پوشش پاششی توسعه یافت که در آن میتوان دوغاب غلیظ را پس از اختلاط و در نهایتا تمیزه شدن با هوای فشرده، بر روی سطح تاندیش اعمال کرد. اولین سیستم کاربردی در سال 1982 راه اندازی شد .
اواخر دهه 1980 ،به دلیل مزایای قابل توجهی از جمله دانسیته کمتر و کنترل بهتر ضخامت پوشش نسبت به آسترهای گانینگ، در کشورهای توسعه یافته به طور گسترده مورد استفاده قرار گرفت. در این روش، امکان افزودن الیاف و سایر مواد شیمیایی به جرم و اختلاط همگن فراهم شد. این روش توانست بسیاری از مزایای آسترهای صفحه ای و گانینگ را به صورت همزمان داشته باشد و در عین حال معایبی مانند ترکیب ماسه با نسوز، اتلاف مواد برگشتی ناشی از عدم اتصال به دیواره، مشکلات گرد و غبار، عایق بودن ضعیف و … را از میان بردارد.
برای زمانهای طولانی تر ریختهگری، آسترهای قابل اسپری مانند جرم قابل اسپری منیزیت با مقدار MgO متغیر بین 70 تا 90 درصد و حداقل مقدار سیلیس به طور گسترده استفاده می شوند . به عنوان مثال، برای ریخته گر ی 12 -10 ساعت، 75-70 ٪MgO با مقدار س یلیس زیر 15 ٪به خوبی کار می کند. اما برای دستیابی به عمر 25-20 ساعت، 90 %MgO با مقدار سیلیس کمتر از 10 %با ضخامت 40-35 میلی متر در دی واره و ضخامت 60-50 میلی متر در کف مورد نیاز است. لازم به ذکر است جهت تشکیل پیوند شیمیایی در جرم قابل اسپری، تجهیزات پیش گرمایش جداگانه ای پس از کاربرد در دمای حدود 1000 درجه سانتیگراد مورد نیاز است.روش اعمال نسوزهای منیزیتی با این روش به این صورت است که این لایه می تواند روی آجر یا بتن محافظ زده شود. این محصول به صورت پودر در کیسه هایی وجود دارد که به ماشین اسپری کننده اضافه می شود. در این ماشین، با میزان معین شده آب که حدود 20 تا 25 درصد است ترکیب شده و به دیواره اسپری می شود. بهتر است که این ملات به دیواره پیشگرم شده اسپری شود. بر طبق اندازه تاندیش و زمان ریخته گری، ضخامت الیه در دیواره ها و کف تعیین می شود. سپس تاندیش باید تا دمای 600 تا 700 درجه سانتیگراد برای 1 ساعت گرم شود تا آب به صورت کامل خشک و دیواره سخت شود. این تاندیش می تواند به صورت شروع سرد یا به عنوان تاندیش داغ استفاده شود، تاندیش باید یک ساعت تا 1000درجه سانتیگراد قبل از ریخته گری حرارت داده شود.
اطلاعات فنی جرم قابل اسپری
مزایا:
• ریسک پایین جذب هیدروژن
• نبود اتصاالت
• نبود ماسه
• نیروی کار کمتر
• تاندیش زدایی آسان
• قابل کنترل بودن ضخامت آستر
• خواص بهتر عدم انتقال حرارت و در نتیجه کاهش دمای کاری
• کمترین میزان جداشدگی به علت باند قوی
• میزان کمتر نیروی انسانی برای نسوزکاری
• قابلیت استفاده در حالت گرم و سرد بر حسب گرید فوالد
• قابلیت اعمال در آجر یا الیه بتنی ایمنی
• قابلیت کار در 6 یا 7 ذوب در یک سکوئنس
• جابجایی راحت تر
معایب:
• سرمایه گذاری در تجهیزات
• نیاز به کیورینگ شدید
• نیاز همیشگی به ماشین اسپری کننده
• نیاز به پیشگرم کردن بعد از اسپری
• نیاز به تمیز کردن مجدد فلز باقیمانده هنگام خروج قبل از ذوب مجدد
لازم به ذکر است اخیراً به منظور طولانی تر کردن سکوئنس ریخته گری، پوشش های قابل اسپری تاندیش با جرم های خشک قابل ویبره جایگزین شده اند . مقدار MgO از 70 تا 90 درصد با مقدار سیلیس کم برای رسیدن به طول سکوئنس 15-12 ساعت تا 40-35 ساعت متغیر است.
5-5-آستر خشک آسترهای خشک در سال 1986 در اروپا معرفی شدند. تفاوت این روش با تمام روش های قبل ی این است که پوشش به صورت پودر خشک اعمال شده و برای تشکیل آستر کار ی تاند یش، ن یازی به افزودن آب ندارد. در این روش به طور کلی از یک پیوند رزینی) واکنش بایندر/کاتالیست(استفاده میشود که با مقادیر نسبتاً کم گرما )حدود 160 درجه سانتیگراد( فعال می شود. بسته به محصول مورد استفاد ه ممکن است نیاز به ویبره جرم باشد یا خیر اما استفاده از یک شکل دهنده (شابلون) در این روش ضروری است به گونه ای که پودر خشک در شکاف بین آستر دائمی تاندیش و شکل دهنده تغذیه می شود.
یکی از مزایای اصلی آستر خشک این است که به دلی ل عدم وجود آب در سیستم، چسبندگی مستقیمی به آستر دائمی تاندیش وجود ندارد که این موضوع، ته تاندیش زدایی خوب و عمر طولانی تر آستر تاندیش را تضمین می کند. علاوه بر این، سطح یکنواخت پوشش خشک تاند یش و توانایی تولید آستر با اشکال متفاوت موجب بهبود کیفیت فولاد و مقاومت بهتر در برابر فرسایش میگردد و نهایتا افزایش طول سکوئنس را به همراه دارد.
مزایا:
• نبود اتصالات
• نبود ماسه
• ریسک پایین جذب هیدروژن (هنگامی که گرم است)
• نیروی کار کمتر
• کاهش زمان آماده سازی تاندیش
• تهتاندیش زدایی آسان
• آستر یکنواخت
• سازگار با محیط ز یست
• سکوئنس باال
• نصب آسان و سری ع
• بهبود تمیزی فوالد به دلیل یک پارچگی آستر
معایب:
• سرمایه گذاری در تجهیزات
• ریسک هیدروژن (وقتی سرد است)
• عایق بودن کمتر
5-6-استفاده از ماسه با چسب سیلیکات سدیم
یکی از روش های نامتعارف و نا مناسب که اخیرا توسط برخی از فولادسازان مورد استفاده قرار می گیرد، ساختن صفحات تاندیش در کارخانه با استفاده از ماسه CO2 است. در این روش ماسه همراه با ماسه درشت دانه مخلوط شده و نهایتا در هوا یا با گاز شهری یا ماسه CO2 در قالب های ساخته می شود. اگرچه این روش ارزان تر از روش های اصولی اشاره شده در بخش های قبل است، اما مشکل عمده در این رابطه تاثیر بسیار منفی آن بر خواص شمش نهایی است. از آنجایی که در صورت جدا شدن ذرات دیگر فرصت شناور شدن آنها بسیار کم می شود، این نکته احتمال ورود این ذرات را به داخل
شمش افزایش می دهد. این ذرات به صورت آخال در شمش باقی می مانند و موجب کاهش استحکام و ایجاد ترک می شوند.
به نظر می رسد در فرایند ریخته گری پیوسته، انتخاب یک روش از میان روش های ذکر شده در باال دشوار باشد چراکه مزایا و معایب آن ها تقریباً به یک میزان است. بنابراین، هنگام تصمیم گ یری، الزم است عوامل دیگری از جمله عملکرد کارخانه فولاد، کیفیت فولاد، شرایط عملیاتی و غیره نیز مدنظر قرار گیرد. تعدادی از این عوامل موثر بر تصمیم گیری به شرح زیر است:
❖ شکل و ابعاد تاند یش باید از نزدیک بررس ی شود. مشکالت نصب بردها با افزایش اندازه تاند یش افزایش می یابد زیرا نیاز به نیروی کار زیادی دارد و این موضوع دسترس پذیری تاند یش را تحت تأثیر قرار می دهد . با این حال، برایتاند یش های ک وچک، بردها سریع و آسان نصب می شوند، در حالیکه استفاده از روش های تر میتواند بسیار پیچیده و گران باشد. در اعمال پوششها با روش اسپری، نصب سریع است اما زمان خشک شدن طوالنی است.
سیستم های خشک معمولا چرخش مناسبی را برای تاندیشهای بزرگ ارائه می دهند. برای هر تاندش ی با شکل پیچیده، ترجیحاً به سراغ آسترهای خشک نروید، زیرا شابلون ها می توانند بسیار پیچیده و گران باشند.
❖ میزان سکوئنس نیز در انتخاب نهایی نسوزها تأثیر دارد. بردها معموالً در سکوئنسهای باال به علت مشکل اتصاالت از بین می روند. آسترهای خشک نیز در این شرایط مناسب نیستند زیرا منجر به مصرف بیش از حد نسوز می گردد.
❖ برای هر کارخانه ا ی که استفاده از روش “کارسرد” را حداقل برای برخ ی از گریدهای فوالدی خود مناسب میبیند، استفاده از آسترهای صفحه ای و خشک ایده آل هستند . در این موارد ممکن است از روش اسپری نیز استفاده شود، اما نیاز به کیورینگ شدید می تواند اتالف هزینه و زمان را به همراه داشته باشد.
❖ روش گانینگ برای روش »کار سرد « مناسب نیست. به طور مشابه بردهای س یلیسی نیز برای روش کارگرم تاندیش مناسب نیستند.
❖ برای گریدهای فوالدی که کیفیت فوالد چندان حیاتی نیست، بردهای س یلیسی می تواند یک روش اندود کم هزینه و مناسب باشد . با این حال، اگر کیفیت فوالد از اهم یت باالیی برخوردار باشد، س یستمهای اسپری و خشک بهترین هستند حتی بهتر از بردهای گرم منیزیتی.
❖ اگر سرمایه یک محدودیت نی ست و می توان تجهیزات پیچ یده ای را تهیه کرد، هر دو روش خشک و اسپری مناسب هستند .
❖ تعداد تاند یش های موجود، ی ک عامل تعیین کننده مهم است. در کارخانجات با تعداد اندک تاند یش، بردها به علت عملیات ته¬تاندیش زدایی آسان بسیار مناسب هستند. اگر آسترهای اس ید ی نیز قابل قبول باشند، صرف نظر از شرایط دیگر، بردهای س یلیس ی ارزان ترین روش موجود هستند،.
❖ اندازه تاندیش یک عامل اصل ی در تع یین هزینه های آسترکشی تاند یش است به گونه ای که با کاهش اندازه تاندیش، هزینه ها به طور قابل توجهی به ازای هر تن فوالد افزایش م ی یابد )مخصوصاً برای س یستم منیزیتی(. سکوئنس ریختهگری نیز در کاهش هزینه ها بسیار مهم است. با اندازه پاتیلهای بزرگ تر و میزان سکوئنس باالتر، کارخانه هایفوالدی با ظرفیت تولید تناژ ب یشتر دارایمزیت قابلتوجهی در حفظ هزینههای آسترکاری تاندیش، حتی با استفاده از س یستمهای آستر اولیه دارند.
❖ مخلوط های تر منیزیتی قابل اعمال به روش گانینگ معموالً برای آسترِ کاری تاند یش استفاده می شوند . نصب این مواد آسان است اما زمان خشک کردن و پیش گرمایش طوالنی دارند. اما دارای مزایایی نسبت به بردهای منیزیتی میباشند: جذب هیدروژن ندارند و نیاز به نیروی کار کمتری میباش د . مخلوط های گانینگ منیزیتی به سطح آستر دائمی می چسبند و ته¬تاندیش زدایی را در یک دوره طوالن ی ریخته گری دشوار می کنند .
عوامل دیگری از جمله در دسترس بودن امکانات مانند تجهیزات پیش گرمایش و غی ره وجود دارند که می توانند تعیین کننده تصمیم نهایی باشند .
6-ارزیابی مقایسه ای انواع مختلف پوششها و آسترهای نسوز تاندیش آسترِ کار ی تاندیش در تماس با فوالد مذاب بوده و نوسانات سطح مذاب در تاندیش، منجر به آغاز فرسایش از محل تماس فلز با هوا میگردد. اکسیدها ی فلزی مختلف موجود در مذاب و همچنین سرباره در تماس با مواد نسوز تاندیش، از جمله عوامل فرسایش در پوشش نسوز تاند یش تلقی میشوند . نقطه شروع فرسایش، تشکیل “ترک های مویی ” در فصل مشترک فلز-هوا به دلیل پوسته پوسته شدن حرارتی است. نفوذ فلز مذاب و سرباره از طریق ای ن ترک های مویی صورت گرفته و متعاقباً فرسایش رخ می دهد. فرسایش کمتر آسترِ کاری باعث میشود مقادیر ناخالصی کمتری وارد فوالد شود. جدول زیر طیف وس یع ی از دیرگدازهای مورد استفاده در تاند یش را در طول ریخته گری پیوسته برای کاربردهای مختلف، متناسب با ویژگی های آن ها نشان می دهد.

مواد نسوز مصرفی در تاندیش
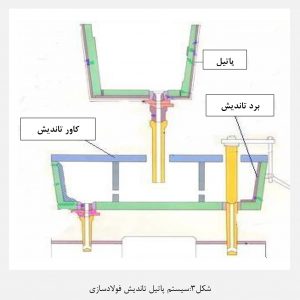
سیستم پاتیل تاندیش فولادسازی
7-اهمیت طراحی تاند یش و نسوزهای اصالح کننده جریان در فولادسازی در فرآیند ریختهگری پیوسته، برای انتقال فوالد مذاب از پاتیل به قالب، از محفظه میانی با نام تاندیش استفاده می گردد.
نقش تاند یش این است که فلز مذاب را به طور یکنواخت و با سرعت و دما ی طراحی شده، بدون ایجاد آلودگ ی توسط ناخالصی ها به قالب ها برساند. شناور شدن ناخالصیها، تالطم)گرداب( سرباره و فلز باقیمانده در تاند یش، تابعی از هیدرودینامیک تاند یش است. طراحی تاندیش و همچنین تجهیزات کنترل کننده جریان/ اصالح کننده، تأثیر ز یادی بر هیدرودینامیک تاند یش دارند.یکی از کارکردها ی اصلی تاندیش، افزایش قابلیت شناورسازی ناخالصیها و در نتیجه تولید فوالد تمیز است. الگوی جریان در داخل تاند یش در حذف ناخالصیها از طریق شناورسازی، کاهش چسبندگی دیواره و اگلومراسیون، نقش مهمی داشته و تابعی از طراحی تاند یش است. جریان مذاب در هر تاندیش معین را می توان با استفاده از اصالح کننده های مناسب جریان تاند یش (TFM)و/یا تغییر طراحی تاند یش، به طور مطلوب تغییر داد. اصالح کنندههای جریان، نقش مهمی در بهبود شناورسازی ناخالصیهای غیرفلزی پاتیل کاور تاندیش برد تاندیش در فولاد دارند. استفاده از نسوزهای جدید، همگنسازی دما، حذف ناخالصی ها و جلوگیری از گرفتگی نازل را در داخل تاندیش تسهیل می کند. جهت آرام کردن جریان و کنترل تالطم داخل تاند یش، دستگاههای کنترل جریان مختلف (FCD) به جای FCDهای سنتی یا قطعاتی مانند سدها، صفحات حائل، پد شارژpads charge ،و پدهای دیوار جانب ی و غیره استفاده می شود. نسل بعد ی FCDها که به عنوان اصالح کننده جریان تاندیش(TFM)و بهینه ساز جریان تاندیش(TFO) شناخته می شوند ، اشکال نسوز پیش ریخته از جنس جرمهای ریختنی بسیار کم سیمان(ULCC) هستند که دارای 85 تا 90 درصد آلومینامی باشد . تزریق گاز آرگون در تاندیش نیز برای کاهش ناخالصیها در فولاد انجام می شود.
لازم به ذکر است که نهایتا این طراحی تاندیش از نظر جریان فلز و انتخاب مواد نسوز و قرارگیری مناسب آنها در داخل تاندیش است که کلید موفقیت عملیات بعدی در فولادسازی است.
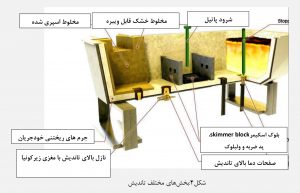
بخش های مختلف تاندیش
8-تفاوتهای اساسی بین دو روش آسترکشی تاندیش: گانینگ و اسپری (پاشش) هماهنگی و انطباق آسترهای ضد سایش اعمال شده به روش گانینگ یا اسپری با آستر دائمی تاندیش، سبب افزایش طول عمر تاند یش میگردد. ویژگیهایی از مواد پوشش که تعیین کننده عملکرد آنها میباشد عبارتند از:
➢ تراکم بهینه جهت بهبود خاصیت عایق بودن و کاهش اتلاف حرارتی از طریق نسوز.
➢ انقباض کنترل شده که به ته تاندیشزدایی آسان و جلوگیری از ایجاد ترک به دلیل انقباض زیاد کمک می کند.
➢ کاهش نفوذ سرباره برای افزایش عمر مفید مواد پوشش و غیره.
مخلوط اسپری شده
تاندیش
جرم های ریختنی خودجریان
نازل بالای تاندیش با مغزی زیرکونیا
شرود پاتیل مخلوط خشک قابل ویبره
صفحات دما بالای تاندیش
بلوک اسکیمرblock skimmer ،
پد ضربه و ولبلوک
جزوه آموزشی آشنایی با تاندیش شماره مدرک: 10-E-53
مواد گانینگ رایج تاندیش به گونهای طراحی شدهاند که در محدوده دمایی 1000 تا 1250 درجه سانتیگراد استحکام پایینی داشته باشند. این ویژگی به ایجاد ی ک ناحی ه ضعی ف بین الیه ایمنی)پشتیبان( و منطقه زینتر شده کمک کرده و تهتاندیش زدایی را تسهیل م ی کند. یکی از معایب بسیار ی از مواد گانینگ تاند یش، انقباض در دمای باالست. انقباض زیاد باعث تنش زیاد و متعاقبا تشکیل ترک در حین کار می شود در حالی که انقباض کم نیز م ی تواند مانعی برا ی تهتاندیشزدایی آسان باشد. رایج ترین مشکلاتی که در استفاده از روش گانینگ با آن مواجه می شویم عبارتند از:
• تشکیل گرد و غبار در حین گانینگ.
• اتلاف مواد در اثر برگشتی بالا که منجر به اتلاف و مصرف زیاد مواد می گردد.
• مشکلات در اعمال ضخامت متغیر که منجر به نفوذ فلز و کاهش عمر نسوز میگردد.
• ته تاندیش زدایی دشوار.
در حالی که وقتی مواد از طری ق اسپری(پاشش) اعمال می شوند ، مزایای زیر را دارد:
• عدم تشکیل گرد و غبار در حین استفاده.
• قابل کنترل بودن ضخامت پوشش و نهایتا افزایش عمر نسوز.
• تهتاندیشزدایی بهتر
علت اصلی موارد فوق را می توان در تفاوت های اساس ی بین گانینگ و اسپر ی) همانطور که در شکل مجاور توضیح داده شده است(یافت. از آنجایی که اختلاط همگن در اسپری)قبل از استفاده از محصول(امکان پذ یر است، استفاده از افزودنی های شیمیایی خاص می تواند به بهبود خواص پایداری حرارتی آستر و همچنین انعطاف پذ یری خوب آن کمک کند.
9-مثال موردی از لایه ایمنی مورد استفاده در یکی از کارخانجات فولادسازی این مورد به یکی از کارخانه های بزرگ فوالد در هند اشاره دارد که دارای ظرفیت پاتیل حدود 300 تن و تاندیش با ظرفیت کاری 50 تن ی و سطح سرریز 55 تن است. تاند یش به شکل قایق طراحی شده است که فوالد مذاب در قسمت میانی آن ریخته شده و از طریق دو نازل که در انتهای آن قرار گرفته اند، خارج می شود. روش به کار گرفته شده، برد سرد بود و فقط نازل تند یش و SEN گرم شدند. همچنین از آجر آلومینایی )شاموتی با 39 درصد آلومینا( به عنوان آستر دائمی ، برد سیلیسی (گارنکس) به عنوان آستر کار ی با ماسه کوارتزیتی در بین آستر آجر و بردها، دو سد از جنس شاموت )39 درصد آلومینا(در کف و دو صفحه حائل)آلوم ینا %70 LC )قرار گرفته در آستر آجری استفاده شد. مشکلی که پیش آمد تهتاندیش زدایی از تاندیش بود که به علت وجود صفحات حائل در آستر آجری پیش آمد. ته تاندیش تاندیش بدون برداشتن آجرهای نزدیک به این صفحات قابل برداشت نبود. در این زمینه اقداماتی انجام ش د اما مشکل افتادن آجرهای آستر همراه با تهتاندیش ها جزوه آموزشی آشنایی با تاندیش شماره مدرک: 10-E-53در فولادسازی همچنان پابرجا بود. این موضوع منجر به سیکل های طوالنی تر در هر تاندیش و تولید ضایعات زیادی در طول ته تاندیش زدایی میشد. همچین هر بار الزم بود تاند یش با آجرهای جد ید روکش شده و سپس به مدت 4 تا 5 ساعت قبل از تثبیت بردها و پر کردن ماسه، خشک م ی شد که این موضوع منجر به افزایش هزینه نسوز میشد . از این رو آنها تصمی م گرفتند از جنس آسترهای ایمنی را از آجر به جرم ریختنی )70 LCC )تغییر دهند . با این پیشرفت، افتادن آجرها در حین تاندیش زدایی به طور کامل حذف شد و همزمان با کاهش سیکل هر تاندیش، تولید ضایعات نیز کاهش یافت. یکی دیگر از مشکالتی که کارخانه فوالد فوق با آن مواجه بود، جذب Si از برد س یلی سی در تاند یش بود که در محدوده 10/0 –0005/0 % قرار داشت. تولید عمده این کارخانه فوالد فوالد کشته شده با Al است. بنابراین، به دلیل این جذب Si ،ترکیب شیمیایی دچار اختالل میشد. استفاده از بردهای س یلیسی مشکالت دیگر ی نی ز داشت: ) 1 )زمانیکه مقدار منگنز ذوب بیش از 30/0 %بود، فرسایش بردها زیاد بود که منجر به ذوب و امتزاج ماسه موجود در پشت آنها میشد ، )2 )به دلیل جدا شدن س یلیس از برد منجر به )گرفتگ ی( نازل ها ی تاندیش میشد. از این رو تصمیم بر جایگزینی بردهای سیلسی با بردهای منیزیتی شد. با این حال، در نسوزهای پایه منیزیتی نیز مشکالتی از جمله جذب اکسیژن دیده میشود. اکسیژن جذب شده توسط مذاب فلز منجر به تشکیل آخال)ناخالصی(هایی م ی شود که برای کیفیت محصول تولیدی مضر است. آخالها در تاند یش با سه مکان یسم ایجاد می شوند: اکسیداس یون مجدد، به دام افتادن سرباره و فرسایش)آستر( نسوز. عموما آخال های ایجاد شده از طریق فرسایش نسوز بیشتر از دو مکانیسم دیگر رخ میدهد . دی رگدازهای منیزیتی مورد استفاده در تاند یش حاو ی اولیوین است که محلول جامد ی از فایالیت (Fe2SiO4) و فورستریت (Mg2SiO4) است. این ترکیبات میتوانند با مذاب فوالد اکسیژن زدایی شده طبق معادالت زیر واکنش دهند:
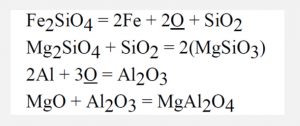
معادله واکنش مذاب فوالد اکسیژن زدایی شده
براساس آنالیزهای انجام شده درمورد آسترهای نسوز تاندیش(TEM ،SEM) مشخص شده است که جزء فایالیت در الیوین کمتر است و همچنین با مشاهده ترکیبات MgSiO3 و MgAl2O4 مشخص شده است که تمام واکنشهای ذکر شده در بالا در تاندیش انجام میشود.
برای دریافت فایل pdf کامل این مطلب، خواهشمند است آدرس ایمیل خود را برای ما ارسال فرمایید.
لطفا فایل مرتبط با نسوزهای تاندیس میل شود
لطفآ فایل پی دی اف را جهت اینجانب ارسال فرمایید
سلام لطفا Pdf را بفرستید. سپاس از شما و گروه
فنی شما.
با سلام وتشکر لطفا فایل پی دی اف را ارسال کنید
لطفا پی دی اف را برای من ارسال کنید
سلام ممنون میشم فایل pdf این مطلب به ایمیل بنده ارسال کنید.
لطفا فایل pdf نسوز تاندیش رو بفرستین
با سلام و احترام
لطفا فایل pdf را برای بندده ارسال فرمایید.
با تشکر
لطفا فایل pdf برای من میل شود.
لطفا فایل pdf برای من میل شود.
لطفا فایل pdf برای من میل شود.
PDF
سلا، لطفا فایل pdf را برای من ارسال کنید.ممنون.