عوامل تاثیرگذار بر مصرف الکترود گرافیتی و راهکارهای کاهش مصرف
این مقاله در سمپوزیوم فولاد ۹۷ منتشر گردیده است.
عوامل تاثیر گذار بر مصرف الکترود گرافیتی و راهکار های جامع کاهش مصرف
امیر حسین یوسف بیگی[۱]، حسن بداغی۱
- گروه پات روشان نیکتا
چکیده
الکترود گرافیتی در فرایند ذوب فولاد در کوره های قوس الکتریکی (EAF) مورد استفاده قرار می گیرد. روش استفاده به این صورت است که سه الکترود گرافیتی به وسیله ی یک رزوه از جنس خود الکترود[۲] به هم وصل شده و توسط کلمپ بر روی کوره نصب می شود. الکترود گرافیتی یکی از مهمترین المان های موجود در ساختار کوره قوس الکتریکی بوده و یکی از مؤلفه های ضروری در مبحث هزینه های تولید فولاد است. مصرف الکترود گرافیتی با پارامترهای مختلف تکنولوژی تولید فولاد و پارامترهای الکتریکی سیستم تأمین ارتباط نزدیکی دارد. متوسط کیلوگرم مصرف الکترود در هر تن فولاد اندازه گیری می شود و دارای طیف گسترده ای از کمتر از ۱ تا ۵ کیلوگرم و در موارد خاصی تا ۱۰ کیلوگرم به ازای هر تن فولاد است. با توجه به افزایش روز افزون قیمت الکترود و تاثیر آن بر بهای تمام شده ی فولاد، در این مقاله بر آنیم تا راهکارهای جامع کاهش مصرف الکترود را بررسی کنیم.
کلمات کلیدی: کوره قوس الکتریکی، الکترود گرافیتی، کاهش مصرف
مقدمه
در اواسط سال ۲۰۱۸ بحران واقعی برای الکترودهای گرافیت آغاز شد. کمبود عرضه و قیمت بالای الکترودهای گرافیتی در سال ۲۰۱۷ مقدمه ای بر این روند بود. سه مجرای اصلی برای بحران در بازار الکترودهای گرافیت شامل افزایش مصرف الکترودهای چینی و محدود کردن صادرات، بالا رفتن محبوبیت استفاده از کوره های قوس الکتریکی در سراسر جهان و بالا رفتن تصاعدی قیمت کک سوزنی تا ۴ برابر از اوایل سال ۲۰۱۷ مشاهده شده است. این وضعیت بحرانی، فولاد سازان در سراسر جهان که از کوره های قوس الکتریکی استفاده می کنند را با کمبود الکترود گرافیتی مواجه و هزینه های افزایش قیمت الکترودهای گرافیتی نگرانی عمده فولادسازان است [۱].
روش تحقیق
با توجه به پیشینه طولانی تولید فولاد به روش کوره های قوس الکتریکی و الکترود گرافیتی به عنوان یکی از اصلی ترین مواد مورد استفاده در این صنعت، مطالعات گسترده ای در زمینه ی دلایل خوردگی الکترود و راهکار های کاهش مصرف آن صورت گرفته است. بر همین اساس در این مقاله بررسی های متعدد صورت گرفته در کوره های AC مورد مطالعه قرار گرفته و به طور اجمالی به مرور ادبیات در زمینه کاهش مصرف الکترود پرداخته ایم.
نتایج و بحث
مکانیزم مصرف الکترود گرافیت به دو دسته اصلی تقسیم بندی می شود:
- مصرف پیوسته
- مصرف نا پیوسته
مصرف مداوم بیشتر بدلیل تصعید ناشی از فرو بردن نوک الکترود و اکسیداسیون دیواره الکترود می باشد و در مصرف ناپیوسته بیشترین میزان مصرف مربوط به شکستگی و افتادن الکترود است (شکل ۱) [۲]
تصعید نوک الکترود گرافیت: تصعید در نوک الکترود گرافیت در دماهای بالای ۳۰۰۰ درجه سانتیگراد رخ می دهد. در زمانی که قوس وجود دارد در ظرف چندین ثانیه پس از پایان قوس عملیات تصعید متوقف می شود. در طی فرایند تصعید، گرافیت به طور مستقیم از فاز جامد به گاز مونو اکسید کربن تبدیل می شود بدون اینکه به حالت مایع تبدیل شود.
عوامل متعددی بر میزان تصعید الکترود گرافیتی تاثیر گذار هستند [۳]:
- میزان یا اندازه جریانی که در هنگام قوس از الکترود گرافیتی عبور می کند.
- قطر مقطع نقطه قوس در نوک الکترود گرافیتی
- مدت زمانی که جریان از طریق الکترود عبور می کند (Tap To Tap Time)
- مقاومت ویژه الکترود گرافیت
- پایداری قوس (پایداری قوس برای عملیات مناسب در کوره قوس الکتریکی ضروری است)
با استفاده از ولتاژ بالاتر و جریان پایین (عملیات قوس طولانی) تلفات ناشی از تصعید الکترود کاهش می یابد و همچنین بهبود در عملیات ذوب نیز حاصل می شود. زمانیکه به صورت مداوم عملیات قوس صورت می گیرد قوس مخروطی منطقه وسیعتری را تحت تاثیر قرار می دهد [۴].
اکسیداسیون دیواره الکترود: عوامل متعددی بر میزان اکسیداسیون دیواره الکترود گرافیتی تاثیر گذار هستند:
- چگالی و مقاومت ویژه الکترود گرافیتی
- مدت زمانی که جریان از طریق الکترود عبور می کند (Tap To Tap Time)
- جریان قوس و دما
- پارامترهای جریان گازهای درون کوره قوس الکتریکی
مهمترین فاکتور مصرف دیواره الکترود عامل اکسیداسیون می باشد. مقدار اکسیژن بواسطه فشار هوای کوره قوس در ذوب های مختلف دستخوش تغییرات زیادی می شود. مقدار اکسیژن در فضای کوره معادل اکسیژن موجود در هوای آزاد محیط است مگر اینکه اکسیژن بیش از اندازه و توسط سیستم های تزریق اکسیژن یا لنس اکسیژن تزریق شود یا در مواردی که کوره مجهز به یک سیستم غبارگیر باشد، مقدار بیش از حد هوا وارد کوره شود. این مقدار ناچیز نیست و خطر چسبیدن بخار مذاب و سرباره بر روی سطح میانی الکترود به واسطه پدیده ای که باعث ایجاد قطرات کوچک می شود وجود دارد. قطرات، به واسطه وجود نیروی گرانش به پایین به سمت و نوک الکترود حرکت می کنند و با خود مقداری الکترود را با فرسایش به داخل حمام مذاب می برند. در طول عملیات ذوب گیری با قوس های کوتاه، لبه بیرونی نوک الکترود به طور مداوم و در نتیجه سایش ناشی از تماس با سرباره و مذاب گرد می شود. این اثر زمانی بوجود می آید که به طور مداوم از آهن اسفنجی استفاده می شود.
اگر چه میزان اکسیداسیون الکترود گرافیت تا حد زیادی به کیفیت گرافیت آن بستگی دارد، اما به شدت به دمای سطح الکترود، سرعت و آشفتگی گازها و میزان اکسیژن تزریقی بستگی دارد [۵].
اثر دما و سرعت فشار هوای محیط بر میزان اکسیداسیون: آزمایشات متعددی برای مقایسه اثر دما و سرعت فشار هوا در کوره قوس تحت شرایط کنترل شده و در تونل های باد در دماهای مختلف و سرعت های مختلف انجام شده است [۶] [۲].
میزان اکسیداسیون محیط اطراف ستون الکترود با دیگر نقاط برابر نیست. عوامل متعددی از جمله میزان باز بودن دریچه سرباره گیری، میزان هوایی که به دلیل آب بندی نامناسب از طریق سقف و یا عدم کنترل سیستم غبارگیر وارد کوره می شود یا سیستم های تنظیم اتوماتیک الکترود (Electrode Regulation) همه و همه باعث افزایش اکسیداسیون در مناطق خاصی از سطح الکترود می شود. این وضعیت منجر به تغییر شکل غیر عادی ستون های الکترود می شود. در برخی از کوره ها، قسمت هایی از سطح که در داخل مثلث الکترود قرار دارند، بیشتر از بقیه سطوح اکسید می شوند. تشعشع گرمایی متقابل از این قسمت ها، دمای سطح در این بخش از ستون را افزایش می دهد و باعث افزایش میزان اکسیداسیون می شود. این الگوی غیر عادی دمای الکترود اغلب در طول عملیات ذوب گیری کوره و در قسمت بین کلمپ و سقف کوره که مرز منطقه قرمز و سیاه رنگ الکترود شیب رو به پایین داخل مثلث نسبت به خارج آن قابل مشاهده است.
فرایند اکسیداسیون، نه تنها در جداره الکترود بلکه در محل قوس (نوک الکترود) رخ می دهد، گرما از طریق احتراق آزاد و مقدار تئوری گرما حدود ۷٫۵ کیلووات ساعت به ازای هر کیلوگرم الکترود گرافیتی قابل محاسبه است [۲].
سایر عوامل تاثیر گذار در مصرف الکترود: شکست الکترود، مهمترین عامل در این دسته بندی می باشد. دلایل مختلفی در شکست الکترود نقش ایفا می کنند که از جمله آن میتوان به برخورد ضایعات در حال سقوط اشاره کرد که اغلب از محل اتصال الکترودهاکه از استحکام کمتری برخوردار است اتفاق می افتد. جهت این نیروها معمولا از یک نقطه خارج از مثلث الکترود بیشتر یا کمتر به سمت مرکز کوره است. جالب است بدانید که سه ستون الکترود نیز توسط نیروهای الکترودینامیک در جهت مخالف، نیروهایی که تمایل به جدا کردن ستون ها در همان جهت افتادن ستون در هنگام قوس الکتریکی دارند را تحت تاثیر قرار می دهند. این نیروها با مجذور آمپر جریان افزایش و با فاصله بین الکترودها کاهش می کنند. شدت این نیروها به کیفیت الکترود، نحوه مونتاژ و جابجایی الکترودها، همچنین عملکرد مکانیسم تنظیم کننده الکترود و عدم وجود حرکت مکانیکی بیش از حد بستگی دارد [۷].
شکست الکترود ممکن است ناشی از شرایط مختلفی از جمله مونتاژ نامناسب الکترود، شل بودن نیپل یا چرخش غلط فاز یا اینکه رزوه ها در خلاف جهت بسته شوند و شل شدن و افتادن الکترود در کوره را در پی خواهد داشت. تا کنون راهکاری برای کاهش افتادن نیپل (Tip Loss) پیدا نشده است و معدود شرکت هایی هستند که اقدام به اندازه گیری مجزای مصرف الکترود ناشی از اکسیداسیون و تصعید با مصرف ناشی از شکست یا افتادن نیپل می کنند. گزارش های رسیده از کارخانجاتی که از به منظور کاهش میزان اکسیداسیون سطحی از پوشش الکترود گرافیتی استفاده می کنند بیانگر این مطلب است که بواسطه لایه ای که روی سطح بوجود می آید، لایه ای مستحکم بین دیواره الکترود و اتمسفر کوره (بخارات و پاشش ذوب) ایجاد کرده و باعث کاهش ترک های ریز سطحی می شود. این ترک ها به مرور زمان بر اثر نفوذ مذاب و سرباره دچار سایش شده و همین شکاف های عمیق به مرور زمان Tip Loss ها را بوجود می آورند [۸].
یکی دیگر از عوامل شوک حرارتی بیش از حد است. هنگامی که یک ستون در خارج از کوره باشد ممکن است دچار تنش برشی سطحی شود و در شرایط بد حتی یک بخش کامل از الکترود را در راستای طولی دچار شکست کند.
هنگامی که در زمان ذوب شدن ضایعات سنگین قوس ثابت می ماند، در لبه بیرونی نوک الکترود گرادیان حرارتی بالایی می تواند تولید و ایجاد ترک های v شکل شود و ممکن است به نزدیک ترین مفصل نفوذ کند. بسته به عمق ترک نیپل میتواند باز و به درون کوره بیافتد.
هر عاملی می تواند باعث کوتاه شدن الکترود به صورت ناگهانی شود. اگر مخروطی شدن نوک الکترود به خوبی انجام شود، قوس نمیتواند یک منطقه بزرگ که دارای سطحی شکسته است را پیدا کرده و درنتیجه باعث شکست یا افتادن الکترود شود. پس از چندین ساعت عملیات ذوب گیری کوره، نیاز است که یک الکترود به ستون مخروطی شکل اضافه شود [۷].
مصرف الکترود و عوامل اپراتوری کوره:
مدت زمان عملیات ذوب گیری (T.T.T[3]): مصرف الکترود در نوک قوس، عمدتا بواسطه قوس الکتریکی و فرسایش سرباره و مذاب، در طول زمان قوس دادن رخ می دهد. در مقابل، اکسیداسیون در کل زمان عملیات ذوب، در لحظات Power On، Power Off و زمانی که الکترود ها داغ هستند انجام می پذیرد. علاوه بر این، در طی عملیات، اثرات جانبی مانند پوسته شدن و شوک حرارتی ممکن است رخ دهد. بدیهی است، هنگامی که عملیات کوره آهسته باشد، مصرف الکترود زیاد می شود [۶].
میزان جریان مورد استفاده در عملیات ذوب گیری:
عمدتا، با کاهش زمان T.T.T، توان کوره و جریان های عملیاتی افزایش می یابد.
نتیجه گیری
مصرف مکانیکی الکترودهای گرافیتی در کوره های قوس الکتریکی بسیار پیچیده است. برخی از عوامل به خوبی درک می شوند، در حالی که برخی دیگر نیاز به تحقیق بیشتر و عمیقی دارند. البته هدف این است که مصرف الکترود را تا حد ممکن کم کنیم. این یک مزیت برای فولاد سازان است که هزینه به ازای هر تن فولاد را کاهش داده و تولید کننده الکترود با بهبود مزیت رقابتی در فولاد سازی با کوره های قوس به این امر کمک کند. در همین راستا با کنترل اتمسفر کوره، جریان عبوری از ستون الکترود، تنظیم طول قوس، پوشش الکترود گرافیتی به منظور کاهش اکسیداسیون، کنترل نحوه ی شارژ قراضه و آهن اسفنجی و سرباره سازی به کاهش ضریب مصرف الکترود دست یافت [۹]. در پژوهشهای بعدی میتوان به هر یک از این راهکارها به طور کاملتری پرداخت.
منابع
[۱] |
۳٫ Editor, “Graphite Electrode Crisis to Deepen in 2018?,” 8 May 2018. [Online]. Available: https://www.steel-360.com/stories/graphite-electrode/graphite-electrode-crisis-to-deepen-in-2018-2. |
[۲] |
P. Migas, and M. Karbowniczek, “Selected Aspects of Graphite Applications in Ferrous Metallurgy,” AGH-University of Science and Technology, Department of Ferrous Metallurgy,, Freiberg, 2013. |
[۳] |
J. R. Montminy, “VIBRATION RESISTANT THREAD DESIGN TO PREVENT LOOSENING OF GRAPHITE ELECTRODE JOINTS ON AN ELECTRIC ARC FURNACE,” 2007. |
[۴] |
W. E. Schwabe, “The Mechanics of Consumption of Graphite Electrodes in Electric Steel Furnaces,” Interrelation of Materials and Equipment, pp. 140-145, 1971. |
[۵] |
D.-m. Zhang, “Analysis for Graphite Electrode Unit Consumption in Manufacture System and Use System of Steelmaking EAF,” in Iran symposium steel, Ahvaz, Iran, 2013. |
[۶] |
A. Nazari, “Modeling of thermal radiation in the internal sections of a Three-phase AC electrical arc furnace by means of a new temperature estimation method for AC arcs,” JASETR, vol. 1, no. 3, pp. 60-70, 2012. |
[۷] |
G. D. Apalkova and V. V. Mochalov, “To the Problem of Graphite Electrode Consumption during Steel Smelting,” Ural Electrode Institute, Chelyabinsk , Russia, 1995. |
[۸] |
G. C. GmbH, “PROTECTIVE COATING FOR GRAPHITE ELECTRODES,” Graphite Cova GmbH, Pegnitz, Germany, 2018. |
[۹] |
P. Schroth and J. S. Davis, “ELECTRODE BREAKAGE PATTERNS AS A FUNCTION OF ELECTRODE/NIPPLE STRENGTH RELATIONSHIP,” Interrelation of Materials and Equipment, pp. 145-148, 1971. |
جداول
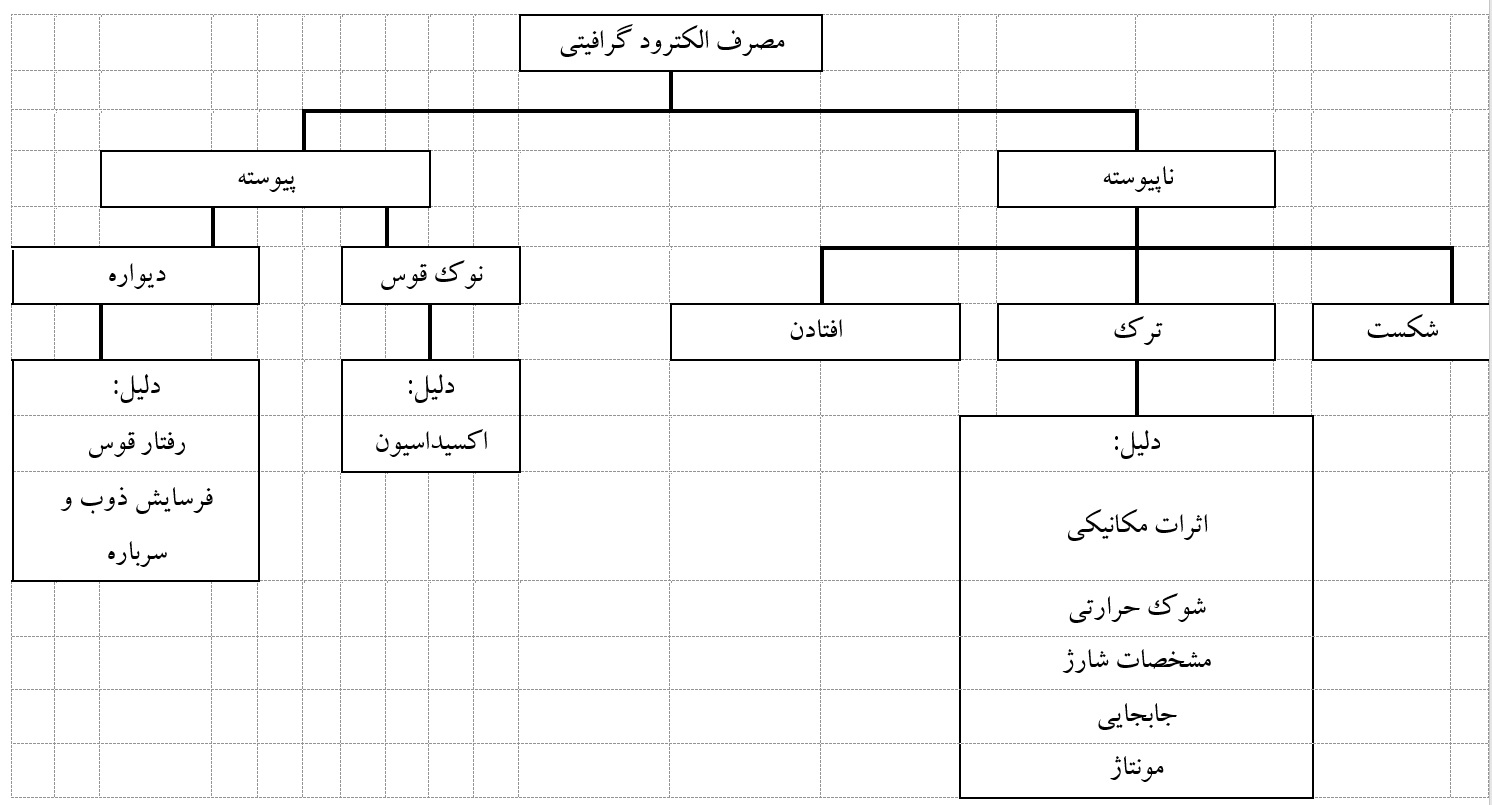
شکل ۱: طبقه بندی مصرف الکترود گرافیتی
[۱] a.yousefbeigi@patron.group
۳] Tap to Tap Time