انتخاب ظرفیت کوره القایی
بررسی سناریوهای محتلف برای انتخاب ظرفیت کوره القایی مناسب
امیر حسین یوسف بیگی- مهندس فروش گروه پاترون
این مقاله در مجله چیلان، سال سیزدهم، شماره ۷۹، اردیبهشت ماه ۱۳۹۷، از صفحه ۷۱ تا ۷۵ به چاپ رسیده است.
مقدمه:
یکی از دغدغه های سرمایه گذاران در حوزه فولاد سازی با کوره های القایی، انتخاب تعداد کوره متناسب با تناژ مد نظر است. توصیه های افراد در این زمینه عموما حسب تجربه شخصی و گاه بر اساس برخی و نه همه عوامل تاثیرگذار در یک انتخاب اقتصادی است.
در این مطلب برای نمونه، دو سناریو را با هم مقایسه میکنیم: ۲ کوره ۳۰ تن القایی و یا ۳ کوره ۲۰ تن. در نگاه اول انتخاب ۳ کوره ۲۰ تن به دلیل سکوئنس های ریخته گری پیوسته به نظر اقتصادی تر می آید اما با بررسی جزئیات می خواهیم بدانیم کدام گزینه اقتصادی تر است.
برای انجام این بررسی، از مدل PSM گروه پاترون استفاده می کنیم.
تشریح مدل :
گروه پاترون برای اولین بار اقدام به مدلسازی میزان تولید با کوره های القایی با عنوان PSM (مخفف عبارت Patron Steelmaking Model) نموده است. با توجه به اینکه قبلا مدلی مشابه که بر اساس پارامترهای مختلف قادر به پیش بینی میزان تولید باشد ارائه نشده است، می توان گفت این مدلسازی برای اولین بار در جهان انجام گرفته است.
پارامترهایی که در مدل PSM وارد می شود و مدل را قادر به پیش بینی میزان تولید می کند عبارت است از: ظرفیت اسمی کوره، توان اسمی کوره، نوع کوره (مدار موازی یا مدار سری)، راندمان تجهیز، دمای محیط، دمای تخلیه، روش زینتر کردن، میزان توقفات، درصد مصرف انواع ضایعات، میزان مصرف آهن اسفنجی، آنالیز محصول تولیدی (مثلا شمش)، ضریب تبدیل ذوب به محصول، توقفات و تاخیرات در فرایند تولید و پارامترهای دیگری که بر راندمان تولید، میزان تولید و مصرف انرژی تاثیر گذار است.
در طول سال های گذشته، گروه پاترون در شرایط مختلفی مدل PSMرا آزموده و آن را محک زده است. خوشبختانه این مدل به قدری کامل و البته پیچیده است که قادر به پیش بینی تمام شرایطی که کارخانجات مختلف با آن روبرو هستند می باشد. همچنین با استفاده از PSM می توان بهای تمام شده محصول تولیدی را محاسبه نمود و در شرایط مختلف قیمتی، میزان سود یا زیان تولید را مشخص نمود.
نمودار ۱ یک نمونه خروجی از مدل PSM است که در مقالات متعدد و نیز در سمینارهای برگزار شده توسط گروه پاترون و همچنین در دوره کاربردی استاندارد سازی زمان و میزان تولید در کوره های القایی با همکاری انجمن تولید کنندگان فولاد ایران و آکادمی ملی فولاد ایران در آذر ماه ۱۳۹۶ برگزار شد، ارائه شده است:
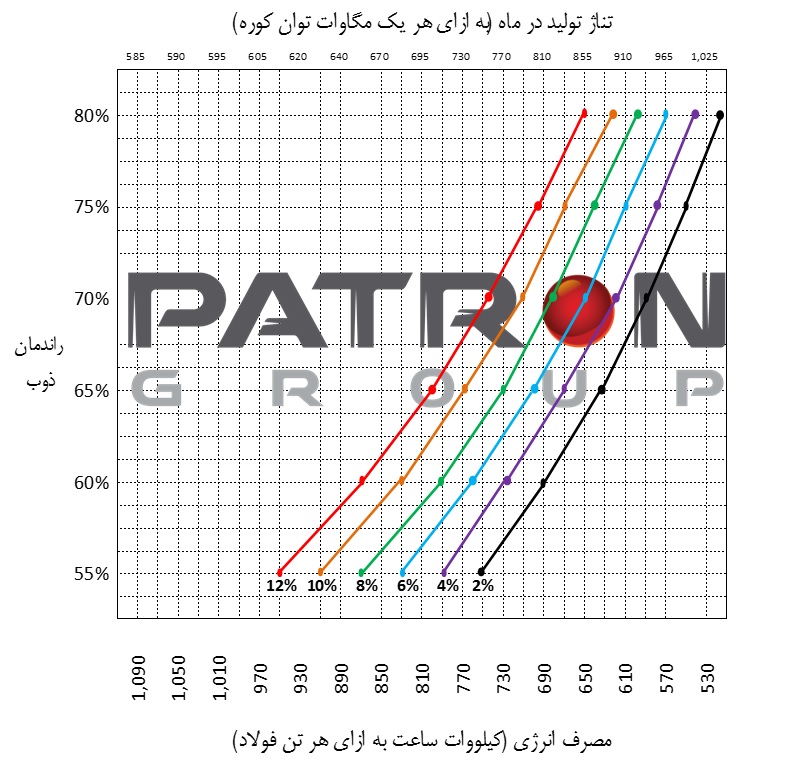
نمودار ۱: PSM
پیش فرض های تحلیل عددی در این مقاله:
پیش فرض ها و سناریوهای در نظر گرفته شده برای محاسبات در این مقاله در شرایط مطابق استاندارد مدل است که به برخی از آنها می پردازیم. این پیش فرض ها عبارتند از:
– ظرفیت کوره: سناریو اول دو کوره ۳۰ تن- سناریو دوم ۳ کوره ۲۰ تن
– نوع کوره: مدار موازی
– دمای محیط: ۲۰ درجه سانتیگراد
– دمای تخلیه مذاب در پاتیل: ۱۶۷۰ درجه سانتیگراد
– روش زینترینگ کوره: ذوب به ذوب یا زینتر مایع (تخلیه ذوب آخر در بوته آماده زینترینگ و نگهداشت ۴۵ دقیقه ای)
– ضریب دسترسی تجهیزات در طی ماه: ۸۲%
– میزان تاخیرات در فرایند تولید: ۶% زمان
– با در نظر گرفتن ۶۰% قراضه (با ترکیب ۲۰% درجه ۱، ۴۰% درجه۲ و ۴۰% درجه ۳) با قیمت میانگین ۱۳۸۵۰ ریال و ۴۰% آهن اسفنجی با قیمت ۱۰۵۰۰ ریال (قیمت ها فرضی هستند)
– آنالیز محصول تولیدی: شمش ۵SP
– ضریب تبدیل ذوب به شمش فولاد: ۹۷%
– توان هر کوره القایی: ۱۲مگا وات برای سناریو اول و ۸ مگا وات برای سناریوی دوم
– میزان تولید هر دو سناریو ۳۰۰٫۰۰۰ تن در سال بوسیله ی مدل PSM محاسبه و در نهایت تحلیل می گردد.
حال با توجه به یکسان بودن پیش فرض ها به بررسی دو سناریو با استفاده از مدل PSM می پردازیم:
- سناریو اول
- ۲ ست کوره ۳۰ تن ۱۲ مگاوات
- سیستم اسلاید گیت ۲QC
- ماشین ریخته گری مداوم ۲ خط
- تعداد ۲۰۰ نفر پرسنل با هزینه سربار ۲٫۵۰۰٫۰۰۰٫۰۰۰ ریال در ماه.
با توجه به فرضیات فوق، نتایج ذیل حاصل می گردد:
مدت زمان کل سرباره گیری، مدت زمان نمونه گیری، از دست رفته، خاموشی کوره، انتظار برای پاتیل و نگهداشت های دیگر ذوب (DAS)، مدت زمان تخلیه در پاتیل و برگشت کوره مطابق ادعای یک شرکت سازنده کوره القایی ۲۰ دقیقه در نظر گرفته شده است.
نتایج |
|||
ردیف |
شرح |
مقدار |
واحد |
۱ |
حداکثر تولید در روز (بدون احتساب ۱۰ دقیقه توقف در تغییر شیفت) |
۷۳۶ |
تن در روز |
۲ |
متوسط تولید ماهیانه (بدون تعمیرات اساسی) با احتساب زینتر |
۱۷,۶۱۴ |
تن در ماه |
۳ |
متوسط تولید روزانه |
۵۸۷٫۱۳ |
تن در روز |
۴ |
تولید سالیانه با احتساب ۱۵ روز تعطیلات جهت اورهال |
۲۰۲,۶۸۱ |
تن در سال |
۵ |
راندمان نسبت به شاخص (هر ۱ مگاوات توان کوره ۱۰۰۰ تن در ماه) |
۷۳٫۳۹% |
درصد |
۶ |
فسفر محصول |
۰٫۳۶ |
درصد |
۷ |
گوگرد محصول |
۰٫۰۳ |
درصد |
۸ |
ضریب مصرف سیلیکومنگنز |
۹٫۳۱ |
کیلوگرم به ازای هر تن محصول |
۹ |
کل مدت زمان ذوب (Tap to Tap Time) |
۱۲۰٫۰۵ |
دقیقه |
۱۰ |
سود ماهیانه (هزار ریال) بدون مالیات در نظر گرفتن بر ارزش افزوده |
۱۷,۶۱۵,۱۰۴ |
هزار ریال در ماه |
۱۱ |
سود به ازای هر کیلو (بدون مالیات در نظر گرفتن بر ارزش افزوده) |
۱,۰۰۰ |
ریال به ازای هر کیلوگرم شمش |
۱۲ |
سود سالیانه (هزار ریال) بدون مالیات |
۲۰۲,۶۹۵,۱۵۰ |
هزار ریال در ماه |
هزینه ها در این شرایط |
|||
۱ |
هزینه قراضه در بهای تمام شده |
۹,۱۹۶ |
ریال به ازای هر کیلوگرم محصول |
هزینه آهن اسفنجی در بهای تمام شده |
۵,۰۷۲ |
ریال به ازای هر کیلوگرم محصول |
|
کل هزینه مواد اولیه |
۱۴,۲۶۸ |
ریال به ازای هر کیلوگرم محصول |
|
۲ |
هزینه برق |
,۴۷۹٫۶۷ |
ریال به ازای هر کیلوگرم محصول |
هزینه تقریبی گاز |
۲۹ |
ریال به ازای هر کیلوگرم محصول |
|
هزینه آب |
۷۲ |
ریال به ازای هر کیلوگرم محصول |
|
کل انرژی |
۵۸۱ |
ریال به ازای هر کیلوگرم محصول |
|
۳ |
هزینه فروآلیاژ |
۴۹۳ |
ریال به ازای هر کیلوگرم محصول |
هزینه جرم سیلیسی کوره |
۹۲ |
ریال به ازای هر کیلوگرم محصول |
|
هزینه مواد مصرفی به جز فروآلیاژ و جرم کوره |
۳۶۷ |
ریال به ازای هر کیلوگرم محصول |
|
کل مواد مصرفی |
۹۵۳ |
ریال به ازای هر کیلوگرم محصول |
|
۴ |
هزینه نیروی انسانی |
۳۰۷ |
ریال به ازای هر کیلوگرم محصول |
هزینه های بالاسری تولید |
۱۴۱٫۹۳ |
ریال به ازای هر کیلوگرم محصول |
|
کل هزینه های ثابت |
۴۴۹ |
ریال به ازای هر کیلوگرم محصول |
|
کل بهای تمام شده |
۱۶,۲۵۰ |
ریال به ازای هر کیلوگرم محصول |
پرت سر و ته شمش مطابق محاسبات ذیل انجام گردید:
میانگین وزن ذوب: ۳۲ تن
تعداد کوره: ۲ ست
تعداد سکوئنس: ۲ ذوب
وزن هر متر شمش ۱۵۰ در ۱۵۰ میلیمتر: ۱۰۵۰ کیلوگرم
بدین ترتیب که هر خط ۳۰ عدد شمش شش متری و یک عدد شمش ۲۸۲ سانتی متری خواهد داشت. با احتساب ۲ خط ریخته گری، مقدار پرت برای تولید ۶۴ تن فولاد در حدود ۴۲/۱۵ کیلوگرم به ازای هر تن می باشد. با در نظر گرفتن هزینه تبدیل ۲۴۰۰ ریال این مقدار ۳٫۷ تومان می باشد.
- سناریو دوم
فرضیات:
- ۳ ست کوره ۲۰ تن ۸ مگاوات
- سیستم اسلاید گیت ۱QC
- ماشین ریخته گری مداوم ۲ خط
- تعداد ۲۲۰ نفر پرسنل با هزینه سربار ۳٫۰۰۰٫۰۰۰٫۰۰۰ ریال در ماه
با توجه به فرضیات فوق، نتایج ذیل حاصل می گردد:
مدت زمان کل سرباره گیری، مدت زمان نمونه گیری، از دست رفته، خاموشی کوره، انتظار برای پاتیل و نگهداشت های دیگر ذوب (DAS)، مدت زمان تخلیه در پاتیل و برگشت کوره مطابق ادعای یک شرکت سازنده کوره القایی ۲۰ دقیقه در نظر گرفته شده است.
نتایج |
|||
ردیف |
شرح |
مقدار |
واحد |
۱ |
حداکثر تولید در روز (بدون احتساب ۱۰ دقیقه توقف در تغییر شیفت) |
۷۳۵ |
تن در روز |
۲ |
متوسط تولید ماهیانه (بدون تعمیرات اساسی) با احتساب زینتر |
۱۷,۳۶۴ |
تن در ماه |
۳ |
متوسط تولید روزانه |
۵۷۸٫۸۰ |
تن در روز |
۴ |
تولید سالیانه با احتساب ۱۵ روز تعطیلات جهت اورهال |
۱۹۹,۸۰۸ |
تن در سال |
۵ |
راندمان نسبت به شاخص (هر ۱ مگاوات توان کوره ۱۰۰۰ تن در ماه) |
۷۲٫۳۵% |
درصد |
۶ |
فسفر محصول |
۰٫۳۶ |
درصد |
۷ |
گوگرد محصول |
۰٫۰۳ |
درصد |
۸ |
ضریب مصرف سیلیکومنگنز |
۹٫۳۰ |
کیلوگرم به ازای هر تن محصول |
۹ |
کل مدت زمان ذوب (Tap to Tap Time) |
۱۲۰٫۰۹ |
دقیقه |
۱۰ |
سود ماهیانه (هزار ریال) بدون مالیات در نظر گرفتن بر ارزش افزوده |
۱۶,۴۳۵,۶۴۸ |
هزار ریال در ماه |
۱۱ |
سود به ازای هر کیلو (بدون مالیات در نظر گرفتن بر ارزش افزوده) |
۹۴۷ |
ریال به ازای هر کیلوگرم شمش |
۱۲ |
سود سالیانه (هزار ریال) بدون مالیات |
۱۸۹,۱۲۴,۲۴۹ |
هزار ریال در ماه |
هزینه ها در این شرایط |
|||
۱ |
هزینه قراضه در بهای تمام شده |
۹,۱۹۶ |
ریال به ازای هر کیلوگرم محصول |
هزینه آهن اسفنجی در بهای تمام شده |
۵,۰۷۲ |
ریال به ازای هر کیلوگرم محصول |
|
کل هزینه مواد اولیه |
۱۴,۲۶۸ |
ریال به ازای هر کیلوگرم محصول |
|
۲ |
هزینه برق |
,۴۷۹٫۸۲ |
ریال به ازای هر کیلوگرم محصول |
هزینه تقریبی گاز |
۲۹ |
ریال به ازای هر کیلوگرم محصول |
|
هزینه آب |
۷۲ |
ریال به ازای هر کیلوگرم محصول |
|
کل انرژی |
۵۸۱ |
ریال به ازای هر کیلوگرم محصول |
|
۳ |
هزینه فروآلیاژ |
۴۹۳ |
ریال به ازای هر کیلوگرم محصول |
هزینه جرم سیلیسی کوره |
۸۸ |
ریال به ازای هر کیلوگرم محصول |
|
هزینه مواد مصرفی به جز فروآلیاژ و جرم کوره |
۳۵۸ |
ریال به ازای هر کیلوگرم محصول |
|
کل مواد مصرفی |
۹۴۰ |
ریال به ازای هر کیلوگرم محصول |
|
۴ |
هزینه نیروی انسانی |
۳۴۲ |
ریال به ازای هر کیلوگرم محصول |
هزینه های بالاسری تولید |
۱۷۲٫۷۷ |
ریال به ازای هر کیلوگرم محصول |
|
کل هزینه های ثابت |
۵۱۵ |
ریال به ازای هر کیلوگرم محصول |
|
کل بهای تمام شده |
۱۶,۳۰۳ |
ریال به ازای هر کیلوگرم محصول |
با توجه به اهمیت داشتن پرت سر و ته شمش برای این سناریو محاسبات ذیل انجام گردید:
میانگین وزن هر ذوب: ۲۰ تن
تعداد کوره: ۳ ست
تعداد سکوئنس: ۹ ذوب
وزن هر متر شمش ۱۵۰ در ۱۵۰ میلیمتر: ۱۰۵۰ کیلوگرم
بدین ترتیب که هر خط ۹۴ عدد شمش شش متری و یک عدد شمش ۱۶۸ سانتی متری خواهد داشت. پرت ۰٫۲۸ می باشدکه با احتساب ۲ خط ریخته گری و مقدار پرت برای تولید ۱۹۸ تن فولاد در حدود ۲٫۹۷ کیلوگرم در تن می باشد. با در نظر گرفتن هزینه تبدیل ۲۴۰۰ ریال این مقدار ۰٫۷ تومان به ازای هر تن فولاد می باشد.
نتیجه گیری:
با توجه به داده های بدست آمده و با احتساب میزان تولید، بهای تمام شده و پرت سر و ته شمش سناریو اول یعنی ۲ ست کوره ۳۰ تن نسبت به ۳ تا کوره ۲۰ تن اقتصادی تر می باشد.
همانطور که در نمودار های بالا مشاهده می شود، هزینه های سناریوی دوم به مراتب بیشتر از سناریوی اول بوده و بر همین اساس برای کارخانجاتی که شمش تولیدی خود را تبدیل به محصول نهایی می کنند با توجه به محاسبات پرت سر و ته شمش سود در خرید دو کوره ۳۰ تن بیشتر از ۳ ست کوره ۲۰ تن می باشد.
لازم به ذکر است در محاسبه بهای تمام شده، هزینه استهلاک در نظر گرفته نشده است.
با توجه به آنکه سرمایه گذاری لازم برای ۲ ست کوره ۳۰ تن نسبت به ۳ ست کوره ۲۰ تن کمتر است، طبیعتا هزینه استهلاک این گزینه نیز کمتر است و لذا در محاسبه ها و مقایسه ها خللی ایجاد نمی نمایند و نتیجه گیری فوق معتبر خواهد بود. اما در مواردی که نتیجه فوق الذکر به دست نیاید، لازم است هزینه استهلاک نیز جهت انتخاب سناریوی اقتصادی تر در نظر گرفته شود.
نکته دیگر آن که با توجه به موقعیت جغرافیایی کارخانه های مختلف فولادسازی و تاثیر عواملی چون در دسترس بودن مواد اولیه قراضه یا آهن اسفنجی، همچنین قیمت تمام شده آنها و عوامل دیگر، چنانچه مکان های مختلفی مورد نظر باشد، به شیوه مشابه می توان شرایط هر گزینه را بررسی نمود.
عالی بود تشکر