مروری بر مدل های فرایند ریاضی برای فرایند کوره قوس الکتریکی
A Review of Mathematical Process Models for the Electric Arc Furnace Process
Thomas Hay,* Ville-Valtteri Visuri, Matti Aula, and Thomas Echterhof
مروری بر مدلهای فرایند ریاضی برای فرایند کوره قوس الکتریکی
توماس هی، ویلی والتری ویزوری، ماتا آئولا و توماس اکتروف
کوره قوس الکتریکی واحد فرآیند اصلی در فولادسازی مبتنی بر قراضه است. با توجه به اهمیت آن، مدلهای ریاضی متعددی برای پیشبینی روند فرآیند کوره قوس الکتریکی ایجاد شدهاند. این مقاله مدلهای فرآیند ریاضی پیشنهاد شده در ادبیات را مرور میکند، رایجترین رویکردهای مدلسازی را شناسایی میکند و از توصیفهای ریاضی برای پدیدههای اصلی استفاده میکند. علاوه بر این، اعتبار چنین مدل هایی به تفصیل مورد بحث قرار گرفته است. در نهایت، مقاله شکافهای موجود در دانش موجود را شناسایی کرده و پیشنهاداتی برای توسعه بیشتر مدلهای فرآیند ریاضی ارائه میکند.
1-مقدمه
کوره قوس الکتریکی (EAF) که در سال 1889 توسط پاول هرولت اختراع شد، فرایند اصلی در فولادسازی مبتنی بر قراضه را تشکیل می دهد. در ابتدا بیشتر برای تولید فولادهای خاص استفاده می شد، اما خود را به عنوان یکی از فرایندهای اصلی فولادسازی در اواخر قرن بیستم تثبیت کرد. در سال 2018، فرایند EAF، 523918000 تن فولاد را در سراسر جهان عرضه کرد که 9/28 درصد از کل تولید فولاد خام را تشکیل می دهد. در مقایسه با مسیر اصلی در ساخت فولاد بر پایه سنگ آهن، کوره بلند و مبدل، مسیر EAF مصرف انرژی را تا 61 درصد و انتشار کربن را تا حدود 77 درصد کاهش می دهد. راندمان و بهره وری فرایند به طور چشمگیری از طریق آشنایی با پیشرفت های فنی مثل افزایش استفاده از اکسیژن، کربن و سایر منابع انرژی شیمیایی، سرباره کف کننده و کربن مونواکسید پس از احتراق، بهبود یافته است. با این وجود، پتانسیل قابل توجهی برای بهینه سازی بیشتر باقی مانده است. این امر، در تفاوت بین تقاضای انرژی نظری تقریباً 400 کیلووات ساعت برای ذوب و گرم کردن ضایعات و میانگین مصرف واقعی EAF مدرن که حدود 375 کیلووات ساعت انرژی الکتریکی و مقدار مشابهی از انرژی شیمیایی است، آشکار می شود، که منجر به بازدهی کل حدود 50 درصد می شود. با این حال، پارامترهای لازم برای تجزیه و تحلیل و بهینه سازی فرآیند را در بسیاری از موارد به دلیل شرایط سخت داخل کوره نمی توان مستقیماً اندازه گیری کرد. به عنوان مثال، دما و ترکیب مذاب و سرباره را می توان تنها از طریق اندازه گیری نقطه ای و به طور بالقوه با کمی تاخیر ناشی از تجزیه و تحلیل لازم نمونه تعیین کرد.
در حالی که روشهایی برای اندازهگیری مستقیم و پیوسته این پارامترها در حال توسعه هستند، برای اکثر کورهها در دسترس نیستند. علاوه بر این، آزمایشهای کارخانهای که برای ارزیابی تأثیر استراتژیهای بهینهسازی مختلف ضروری است، ممکن است به دلیل هزینههای گزاف یا نگرانیهای ایمنی غیرممکن باشد. بنابراین مدلهای ریاضی، منبع ارزشمندی از اطلاعات در مورد پارامترهای فرآیند ناشناخته هستند. شبیهسازیها همچنین میتوانند به عنوان جایگزین ارزانتر، سریعتر و ایمنتر برای آزمایشهای کارخانه ای مورد استفاده قرار گیرند. برایEAF، طیف گسترده ای از مدل ها ، با اهداف و رویکردهای مدل سازی مختلف، توسعه یافته است. هدف از این کار بحث در مورد مدل های فرآیند سریع و جامع است. برخلاف معادلات آماری، برای پیش بینی نقطه پایانی شرایط یا مدلسازی دینامیک سیالات محاسباتی (CFD)، این مدل ها تاکنون به طور دقیق بررسی نشده اند.
2-فرایند EAF
در EAF، مواد حامل آهن ذوب شده و برای تولید فولاد خام استفاده می شوند. ماده خام اصلی قراضه است، اما مواد دیگر مانند آهن بریکت شده داغ (HBI)، آهن کاهش یافته مستقیم (DRI)، یا از فلز داغ نیز می توان استفاده کرد. انرژی از طریق یک یا سه الکترود و همچنین مشعل های سوخت اکسی و واکنش های شیمیایی که با تزریق کربن و اکسیژن به مذاب و سرباره تسهیل می شود، تامین می شود. دو مفهوم مختلف الکتریکی وجود دارد: جریان متناوب (AC) و مستقیم (DC). در کوره های AC، از سه الکترود و قوس استفاده می شود، در حالی که کوره های DC دارای یک الکترود مرکزی و قوس در ترکیب با یک الکترود پایین برای بستن مدار الکتریکی هستند. در هر دو نوع کوره، جریان از طریق بازوهای الکترود متحرکی که برای به حداقل رساندن نوسانات پارامترهای الکتریکی ناشی از حرکت ضایعات یا سطح مذاب تنظیم شده اند، تامین می شود. کوره معمولاً از یک ظرف پایینی تشکیل شده است که با پوشش نسوز پوشانده شده و حاوی یک شیر تهنشینی خارج از مرکز (EBT) یا دهانه ضربهای است. بالاتر از آن، یک پوسته کوره آب خنک وجود دارد که ممکن است حاوی انژکتورها و مشعل ها باشد. یک درب سرباره امکان حذف سرباره و قرار دادن لنس ها برای تزریق اکسیژن و کربن را فراهم می کند. سقف واقع در بالای پوسته نیز با آب خنک می شود و دارای دهانه هایی برای الکترود(ها)، حذف گازهای خروجی و بطور بالقوه شارژ مواد اولیه، سرباره سازها یا آلیاژها می باشد. کوره بر روی سکویی نصب شده است که برای تخلیه و ضربه زدن کج شده است[1,7,11]. شکل 1 اجزای اصلی یک EAF را با استفاده از کوره AC به عنوان مثال نشان می دهد.
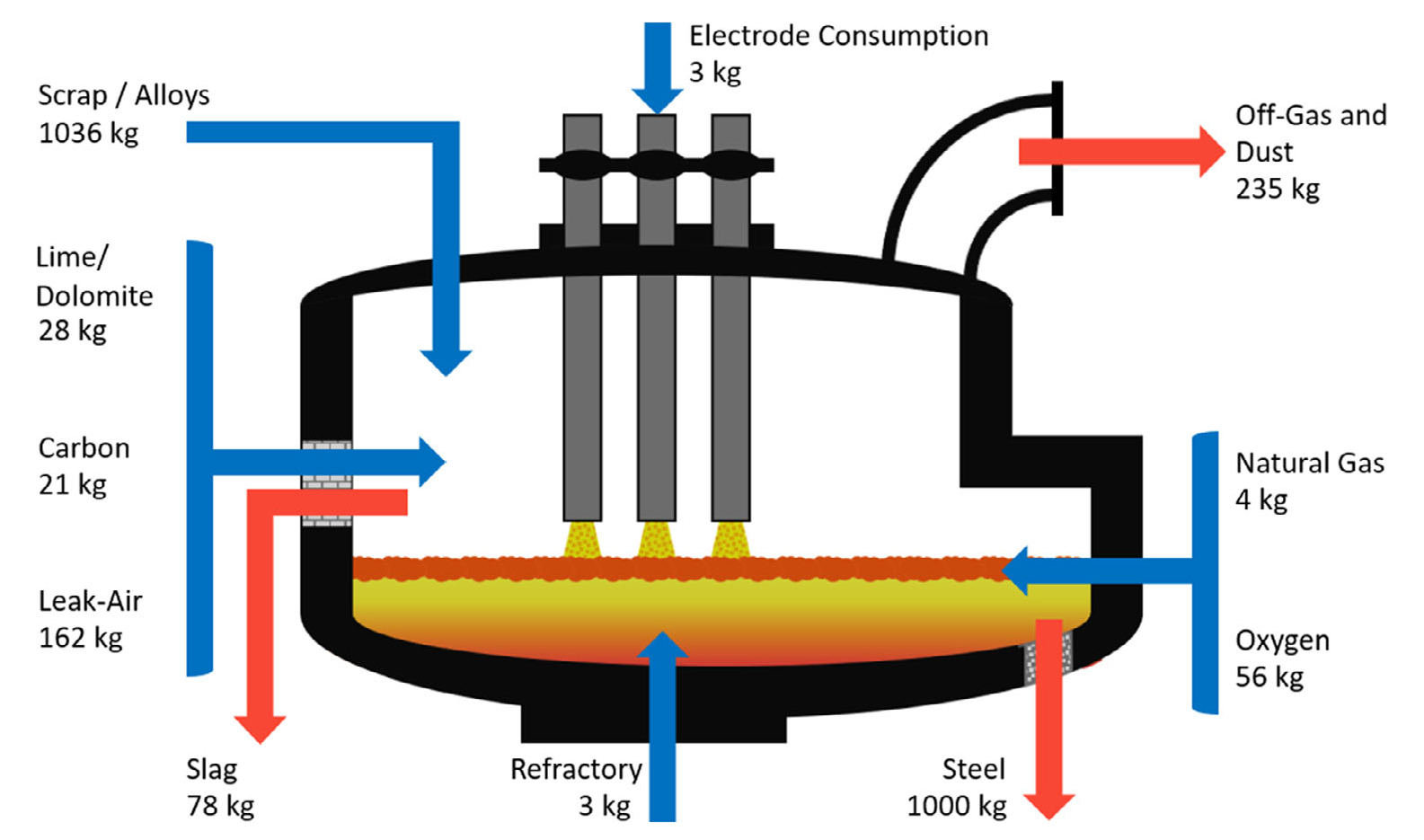
A Review of Mathematical Process Models for the Electric Arc Furnace Process-3
فرآیند EAF یک فرآیند دستهای (بچی) است که معمولاً میتواند به چهار مرحله تقسیم شود: شارژ با یک یا چند سبد قراضه، ذوب ضایعات، گرم کردن و پالایش و در نهایت ضربه زدن (مرحله تپینگ). در ابتدای مرحله ذوب، قوسها با کاهش قدرت به داخل شمع قراضه فرو میروند تا از شکستگی الکترود جلوگیری شود. هنگامی که الکترودها به سطح مذاب می رسند، می توان از تنظیمات قدرت بالا با ضایعات استفاده کرد که دیواره ها و سقف کوره را از قوس الکتریکی محافظت می کند. مشعل های اکسیژن با استفاده از سوخت هایی مانند گاز طبیعی یا نفت اغلب برای تسهیل ذوب ضایعات اطراف نقاط سرد در طول ذوب و افزایش بهره وری استفاده می شوند. آلاینده های قابل احتراق و کربن تا حدی در کوره می سوزند و گازهای قابل اشتعال آزاد می کنند. اکسیژن را می توان به تخته فری تزریق کرد تا امکان احتراق پس از احتراق این گازها در داخل کوره فراهم شود و بخشی از انرژی از دست رفته با گاز خارج شده را بازیابی کند. کارایی مشعل ها و پس از احتراق به مقدار و دمای ضایعات جامد داخل کوره بستگی دارد. بنابراین، استفاده از مشعل ها و تزریق اکسیژن برای پس از احتراق زمانی که ذوب آنقدر پیشرفت کرد که آنها را ناکارآمد کرد، متوقف می شود. هنگامی که شارژ بیشتر مذاب است، فرآیند وارد فاز حمام تخت می شود که طی آن مذاب فولاد گرم و تصفیه می شود. از آنجایی که قوس دیگر توسط ضایعات محافظت نمی شود، انرژی بیشتری به سطوح خنک شده با آب تلف می شود. با تزریق اکسیژن و کربن به مذاب و حفظ خواص صحیح سرباره، سرباره را می توان کف کرد، تا حدی از قوس محافظت کرد و کارایی انرژی را افزایش داد. اکسیژن نیز برای حذف ناخالصی ها از مذاب ضروری است. علاوه بر این، اکسیداسیون کربن و عناصر کمیاب، انرژی شیمیایی بیشتری آزاد می کند و بهره وری را افزایش می دهد. مفاهیم مختلفی برای پیش گرم کردن ضایعات با استفاده از مشعل ها یا EAF بدون گاز موجود است و در برخی موارد، ضایعات پیش گرم شده، فلز داغ یا سایر مواد آهن دار به جای استفاده از سبدهای قراضه به طور مداوم در کوره شارژ می شود.[5،7،12]
2.1. توازن جرم
یک موازنه جرم نمونه برای فرآیند EAF در شکل 2 نشان داده شده است. مقادیر داده شده جرم در هر تن فولاد خام تولید شده است. در حالی که مقادیر بسته به مواد شارژ و استراتژی عملیاتی خاص مورد استفاده برای یک EAF خاص میتوانند در محدوده وسیعی متفاوت باشند، این یک نمای کلی از جریانهای جرم مربوط به مدلسازی EAF را ارائه میدهد.
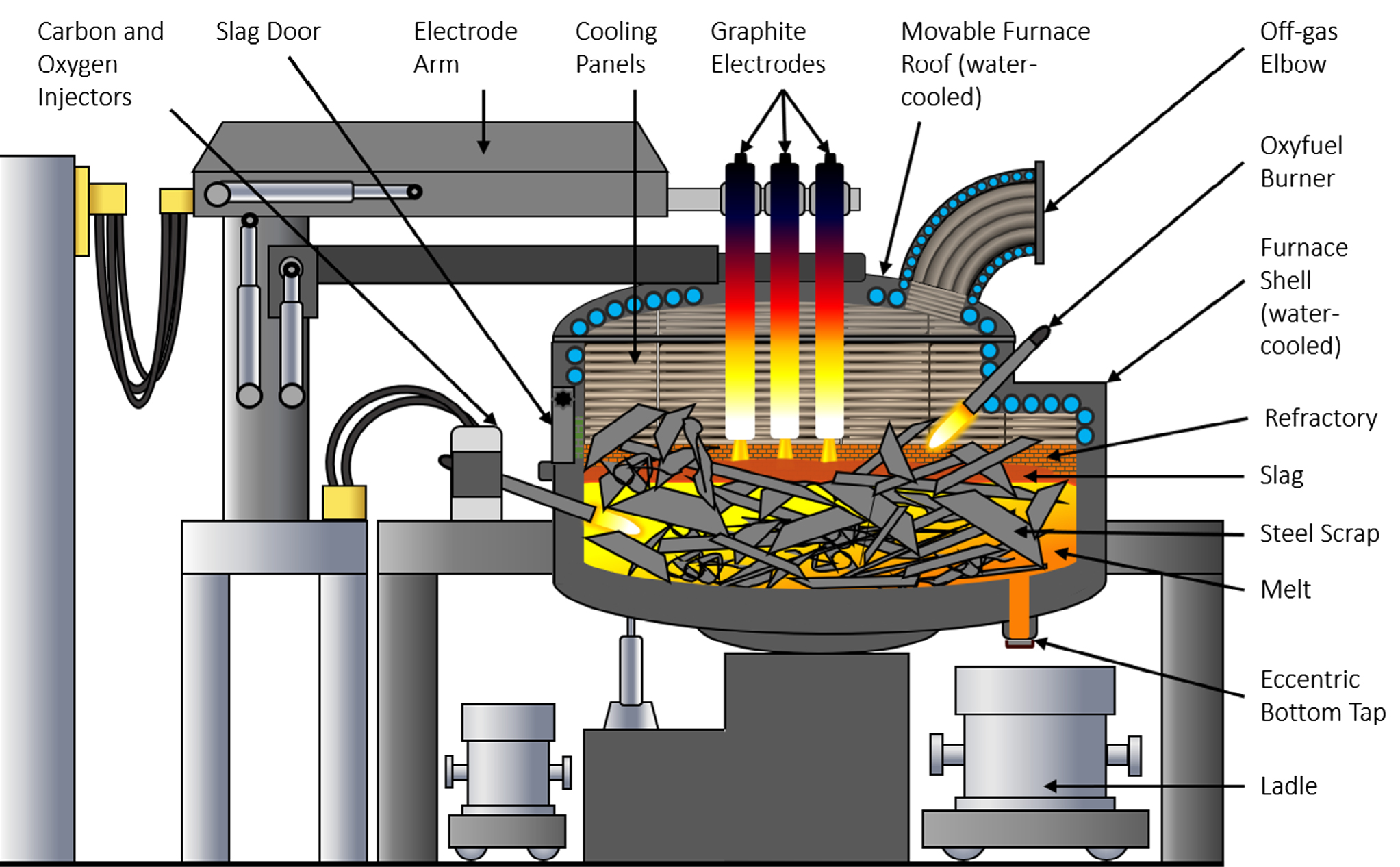
A Review of Mathematical Process Models for the Electric Arc Furnace Process-2
شکل 2: تعادل جرم فرآیندEAF
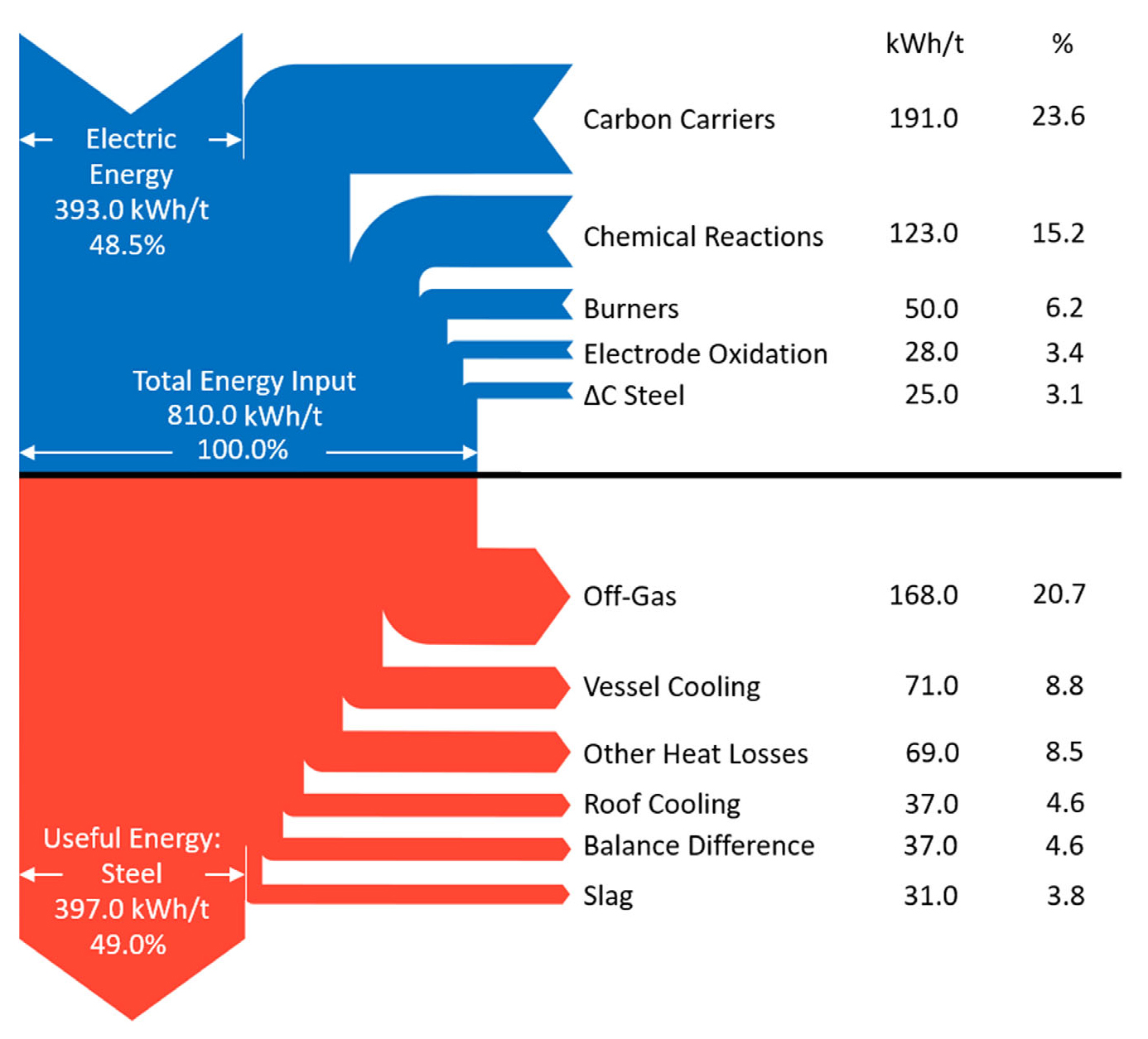
A Review of Mathematical Process Models for the Electric Arc Furnace Process-3 copy
شکل 3: تعادل انرژی یک EAF 100 تنی.
2.2. تعادل انرژی
تقریباً نیمی از انرژی در EAF توسط قوس الکتریکی (13) و نیمی دیگر از طریق واکنش های شیمیایی تأمین می شود. راندمان کلی حدود 50 درصد است و تلفات اصلی از طریق خنکسازی آب اجزای کوره و گازهای خارج از گاز رخ میدهد. انرژی شیمیایی از طریق اکسیداسیون منابع کربن تزریق شده یا باردار، محتوای کربن ضایعات و مصرف الکترود(های) گرافیت تامین می شود. شکل 3 تعادل انرژی نمونه ای را برای یک EAF نشان می دهد. انرژی شیمیایی اضافی توسط مشعل ها و اکسیداسیون آهن و عناصر کمیاب با اکسیژن تزریق شده تامین می شود. انرژی از دست رفته با گاز خارج شده عمدتاً انرژی شیمیایی به شکل مونوکسید کربن نسوخته و هیدروژن است که برخی از آنها را می توان از طریق پس احتراق در کوره بازیابی کرد.[13] سهم انرژی شیمیایی و الکتریکی بسته به استراتژی عملیاتی کوره، بسته به قیمت منابع انرژی و کیفیت محصول مورد نظر می تواند به طور قابل توجهی متفاوت باشد.[5]
مدلسازی و بهینهسازی فرآیند EAF به دلیل تعداد زیاد متغیرها مانند مواد بار مختلف، سهم حاملهای انرژی مختلف و ترکیب و دما هدف، یک کار پیچیده است. مراحل مختلف فرآیند، تغییرات ناپیوسته در طول شارژ مواد و تغییرات زیادی در فرآیند با انواع کورهها، مواد اولیه، کیفیت فولاد مورد نظر و استراتژیهای عملیاتی منجر به توسعه رویکردهای مدلسازی مختلف شده است.
- مدل های فرآیند
مدل فرآیند، «الگوریتمی برای پیشبینی رفتار یک سیستم باز یا بسته» است.[14] این مدل، کنترل پیشبینی و کمک به اپراتور، بهینهسازی فرآیند آفلاین، درک بهتر پدیدههای فیزیکی زیربنایی، و تخمین آنلاین پارامترهایی که نمیتوانند مستقیماً از طریق اندازه گیری ها تعیین شوند، فراهم می کند. [14] در اینجا، اصطلاح مدل فرآیند به مدلهای قطعی مبتنی بر روابط فیزیکی و ترمودینامیکی اشاره دارد و بنابراین رویکردهای صرفاً آماری را حذف میکند.
3.1. انواع مدل های فرآیندی
مدلهای فرآیند و سایر ابزارها برای شبیهسازی یا پیشبینی فرآیندهای صنعتی را میتوان بر اساس هدف و دامنه مورد نظر آنها و همچنین رویکرد مدلسازی مورد استفاده دستهبندی کرد.
3.1.1. دسته بندی با رویکرد مدل سازی
به طور کلی، مدلهای کاربردی صنعتی را میتوان به مدلهای مبتنی بر ارزیابی آماری دادهها که مدلهای آماری یا تجربی نامیده میشوند و مدلهای مبتنی بر روابط فیزیکی یا ترمودینامیکی شناختهشده به نامهای مدلهای مکانیکی، تحلیلی یا پدیدارشناسی تقسیم کرد. مدلهای آماری در صورتی قابل اجرا هستند که کیفیتی که قرار است پیشبینی شود قابل اندازهگیری باشد و دادههای کافی در دسترس باشد، هم این کیفیت و هم پارامترهای فرآیند مؤثر بر آن را مستند کنند. توسعه آنها نسبتاً آسان است و توصیف روابط فیزیکی اساسی ضروری نیست. دقت مدل های آماری عمدتاً با دقت و دامنه داده های مورد استفاده برای آموزش مدل تعیین می شود. یک قانون کلی این است که مدلهای آماری نباید خارج از محدوده دادههای آموزشی آنها اعمال شوند، زیرا توانایی آنها برای برونیابی دقیق فراتر از این محدوده محدود است. این همچنین به این معنی است که مدل بدون تعدیل به فرآیند یا کارخانه دیگری قابل انتقال نیست و به درک پدیدههای فیزیکی زیربنایی کمک نمیکند. در مورد فرآیندهای پیچیده مانند فرآیند EAF، توسعه مدلهای تحلیلی معمولاً دشوارتر از مدلهای آماری است و ممکن است به همان درجه دقت نرسد. با این حال، آنها اجازه برون یابی را می دهند و قابل انتقال هستند زیرا توصیف فیزیکی و ترمودینامیکی جهانی تر است.[15،16] همانطور که قبلا گفته شد، تنها این مدل های تحلیلی تعریف یک مدل فرآیند را برآورده می کنند. با این حال، روش های آماری یا ترکیبی اغلب برای کاربردهای مشابه استفاده می شود. علاوه بر این، مدل ها را می توان بر اساس نوع تعاملی که توصیف می کنند طبقه بندی کرد. یک مدل میتواند صرفاً بر اساس علت و معلول (جبرگرا) باشد یا شامل عناصر احتمالی (تصادفی) باشد. این مدل می تواند شامل رفتار خطی یا غیرخطی و تعریف پیوسته یا گسسته و همچنین یکپارچه یا توزیع شده متغیرها باشد. در عمل، بیشتر مدلها را میتوان بهعنوان ترکیبی مشخص کرد، بهعنوان مثال، عبارات تحلیلی معمولاً شامل پارامترهایی هستند که به صورت تجربی تعیین میشوند، یا پارامترهای یک مدل تجربی بر اساس روابط فیزیکی شناخته شده انتخاب میشوند.
3.1.2. دسته بندی بر اساس دامنه و کاربرد
یک مدل میتواند برای توصیف پدیدههای خاصی ایجاد شود که فقط فازها یا بخشهای خاصی از یک فرآیند را مشخص میکنند یا اغلب با استفاده از چندین مدل فرعی و منطقه، یک فرآیند کامل مانند EAF از شارژ تا ضربه زدن با خارج کوره که مرز سیستم را تشکیل میدهد. علاوه بر این، سطح جزئیات و زمان اجرا باید مطابق با هدف مورد نظر مدل متعادل شوند. برای برنامههای آنلاین و بهینهسازی، زمان اجرا باید کم نگه داشته شود، در حالی که برای درک پدیدههای فیزیکی پیچیده در مقیاسهای کوچک به سطحی از جزئیات نیاز است. این امر مستلزم مدل های مختلفی است که به طور خاص برای برنامه مربوطه تنظیم شده اند.
3.2. مدل های فرآیند EAF
با توجه به طیف گسترده ای از کاربردهای مختلف مدل سازی EAF و پیچیدگی فرآیند، رویکردهای متعددی برای استخراج مدل ها برای این فرآیند به کار گرفته شده است. مدلهای صرفاً آماری یا مبتنی بر دادهها، از جمله شبکههای عصبی، وجود دارد که به عنوان مثال برای ارزیابی مصرف برق[17] یا سیستم الکتریکی یک EAF استفاده میشوند.[18،19] دسته دیگری از مدلها برای ارزیابی مصرف انرژی EAF از یک رویکرد آماری مبتنی بر پارامترهایی استفاده میکنند که با استفاده از روابط فیزیکی مانند تحویل توان مورد انتظار از استفاده از اکسیژن یا گاز طبیعی تعیین میشوند. چنین مدلهای مصرف انرژی، از جمله برخی از رویکردهای شبکه عصبی، اخیراً توسط کارلسون و همکاران بررسی شدهاند.[6]
CFD شاخهای از مکانیک سیالات است که به مدلسازی جریانهای سیال با وضوح فضایی بالا میپردازد. مدلهای CFD مدلهای تحلیلی هستند و با ارائه یک مدل دقیق و جامع، میتوانند تمام پدیدههای مرتبط از جمله جریان سیال، الکترومغناطیسی، انتقال گرما و جرم و همچنین واکنشهای شیمیایی را مشخص کنند. یک بررسی به روز در مورد کاربرد مدل سازی CFD در فرآیند EAF توسط Odenthal ارائه شده است، [10] که به این نتیجه رسید که علیرغم موفقیت در توسعه مدل های CFD که از نظر محاسباتی برای پدیده ها یا اجزای خاص امکان پذیر هستند و پیشرفت های امیدوار کننده به سمت یک روش بیشتر رویکرد جامع در حال ایجاد، هنوز محدودیتهای اساسی برای مدلسازی CFD فرآیند کامل EAF وجود دارد. محدودیت اصلی طیف گسترده ای از مقیاس ها و پدیده های مختلف است که مدل های جامع CFD را از نظر محاسباتی گران و برای برنامه های آنلاین نامناسب می کند.
مدلهای فرآیندی را میتوان بهعنوان حد وسطی بین مدلهای مصرف انرژی و مدلسازی CFD دید. چنین مدلهایی از برخی سادهسازیها مانند معرفی یک یا چند فاز یا ناحیه تودهای استفاده میکنند و از برخی پارامترهای تجربی استفاده میکنند و در عین حال رویکردی عمدتاً تحلیلی را برای پیشبینی کیفیتهای وابسته به زمان حفظ میکنند. این امکان تخمین پارامترهای مختلف فرآیند وابسته به زمان را با مدلی ساده و سریع برای برنامه های آنلاین یا بهینه سازی فراهم می کند. در مقایسه با مدلهای فرآیند، مدلهای مصرف انرژی یک رویکرد بسیار سادهشده و عمدتاً آماری را برای پیشبینی یک پارامتر واحد نشان میدهند، در حالی که مدلهای CFD درجه بالاتری از جزئیات و دقت همراه با تقاضای محاسباتی بهطور قابلتوجهی را ارائه میدهند.
مدلهای فرآیند نه تنها برای فرآیند کامل، بلکه برای توصیف پدیدههای خاص در EAF، به عنوان مثال، انتقال حرارت در قوس الکتریکی، [20] واکنش کربن تزریق شده با سرباره، [21-23] یا تأثیر و پتانسیل بازیافت انرژی در سیستم خارج از گاز ایجاد شده اند. [24،25] در برخی موارد، اینها سپس در مدلهای EAF جامعتری گنجانده شدهاند. مروری کوتاه بر مدلهای فرآیند EAF پیشنهادی قبلاً توسط Logar و همکاران منتشر شده است.[26،27] در این کار، یک بررسی عمیق از مدلها ارائه شده است، که هم مدلهای ذکر شده در نمای کلی لوگار و هم چندین مدل دیگر پیشنهاد شده قبل یا پس از انتشار آن را در بر میگیرد. هدف از این کار بررسی مدلهای فرآیند موجود برای EAF کامل و راهحلهای مختلف اجرا شده برای پدیدههای مختلف مانند تغییرات فاز، تبادل حرارت یا ترموشیمی است. جدول 1 مدلهای فرآیند EAF موجود در نوشته جات را با مراجع مربوطه و سالهای انتشار نشان میدهد. این مدلهای فرآیند عموماً مبتنی بر مناطق تودهای هستند که گسستهسازی فضایی ندارند، به جز شارژ ضایعاتی که در برخی مدلها به چندین ناحیه گسسته شده است.[28،29] جریان های گرما و جرمی بین این مناطق و محیط اطراف مبادله می شود و واکنش های شیمیایی معمولاً در مناطق خاصی در نظر گرفته می شود. سپس از تعادل انرژی و جرم برای ردیابی دما و ترکیب هر منطقه استفاده می شود. در حالی که اکثر این مدلهای فرآیند پویا هستند، رویکردهای شبه پویا مبتنی بر مراحل فرآیند از پیش تعریفشده نیز پیشنهاد شدهاند.[30،31].
-
A Review of Mathematical Process Models for the Electric Arc Furnace Process-5
4. انتقال حرارت
در مدل سازی انتقال حرارت در EAF، توزیع انرژی وارد شده از طریق منابعی مانند قوس(ها) یا واکنش های شیمیایی (شامل مشعل ها و پس از احتراق) به فازهای مختلف داخل کوره باید شرح داده شود. همین امر برای انرژی حذف شده، به عنوان مثال، با گاز یا آب خنک کننده ضروری است. برای توصیف جامع انتقال حرارت و محتوای انرژی حاصل از مناطق مدل، تابش حرارتی، هدایت و همرفت باید تعیین کمیت شود. مدلهای متمرکز بر فاز حمام مسطح شامل انتقال حرارت بسیار محدود یا حتی فازهای همدما را فرض میکنند، [32،33] در حالی که مدلهایی که شامل شرح ذوب میشوند، تخمینهای دقیقتری از جریان گرما در داخل کوره و تأثیر هندسه در حال تغییر و دمای بار ضایعات اراِئه می دهند. [20،34-36] یک رویکرد بسیار ساده استفاده از جریان های حرارتی از پیش تعریف شده است، چه به عنوان ورودی مدل تعیین شده از اندازه گیری هایی مانند دمای آب خنک کننده، یا به عنوان پارامترهای برازش. به طور مشابه، فاکتورهای بازده تجربی را می توان برای تعیین مقدار گرمای تحویل شده به فازهای خاص یا از دست رفتن در گاز و خنک کننده تعریف کرد. روش دیگر، انتقال حرارت بین مناطق از طریق رسانش یا همرفت را می توان با استفاده از ضرایب انتقال حرارت و مناطق سطح خاص توصیف کرد. اینها معمولاً پارامترهای مدل تجربی هستند و متناسب با داده های اندازه گیری شده تنظیم می شوند. برای در نظر گرفتن مساحت سطح و شرایط مختلف، ضرایب انتقال حرارت، سطح سطوح خاص یا فاکتورهای کارایی را می توان با استفاده از مقادیری مانند حجم باقیمانده قراضه یا مقدار و شرایط سرباره کف کننده تنظیم کرد. [13،34،36-38] یک رویکرد حتی جامعتر که برای مدلهای فرآیند EAF اجرا شده است، استفاده از همبستگیهای عدد ناسلت برای استخراج ضرایب انتقال حرارت است.[41_29،30] با استفاده از ضرایب انتقال حرارت، جریان گرما بین مناطق را می توان بر اساس دما و منطقه تماس، با اطلاعات اضافی در مورد خواص فیزیکی و شرایط جریان مورد نیاز در صورت استفاده از همبستگی ناسلت، تعیین کرد. مساحت سطح با استفاده از همبستگی های تجربی و هندسه های ساده شده تعیین می شود و اغلب در یک پارامتر تجربی منفرد همراه با ضریب انتقال حرارت قرار می گیرد. روشهای مختلفی ممکن است ترکیب شوند، برای مثال، استفاده از فاکتورهای بازده یا جریانهای حرارتی ثابت برای محاسبه تلفات انرژی از طریق گاز و خنکسازی و همچنین ضرایب انتقال حرارت برای تبادل بین ضایعات و مذاب.
4.1. انتقال حرارت تشعشعی
با توجه به دماهای بالا در داخل کوره و به خصوص قوس الکتریکی، انتقال حرارت از طریق تشعشعات حرارتی نقش مهمی در EAF دارد. بنابراین برخی از سازندگان تلاش کردهاند تا توصیفات جامعی از انتقال حرارت تشعشعی را در مدلهای فرآیند خود بگنجانند.
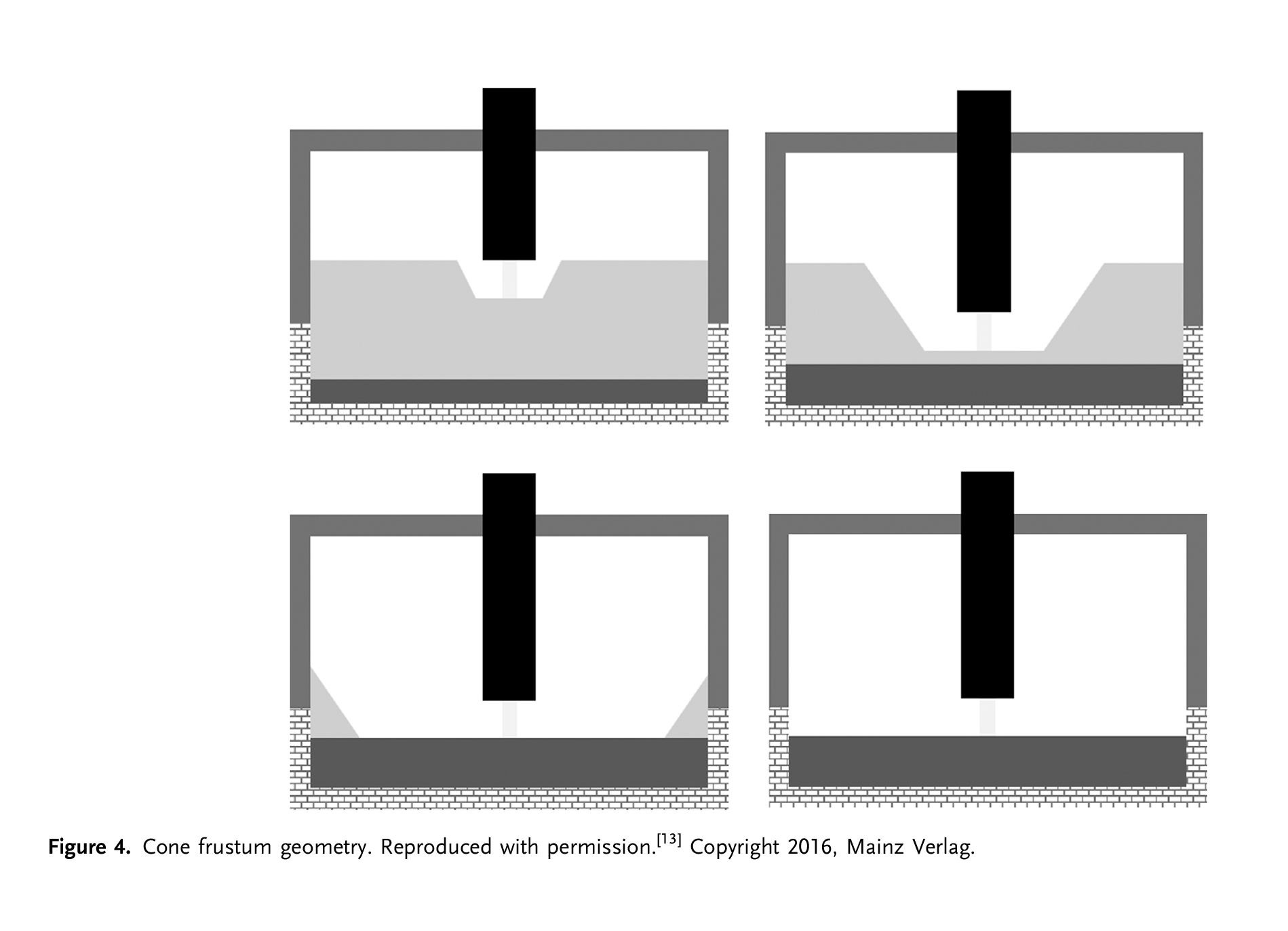
A Review of Mathematical Process Models for the Electric Arc Furnace Process-6
MacRosty و همکاران [34] هندسه ای مبتنی بر یک فضای خالی مخروطی شکل در داخل بار ضایعات معرفی کردند که با پیشرفت ذوب، اندازه آن افزایش می یابد. آنها یک کوره متقارن دورانی با یک الکترود مرکزی را فرض کردند. بر اساس این هندسه، اندازه ها و موقعیت های نسبی سطوح لازم برای محاسبه ضرایب دید را می توان بر اساس حجم فعلی شمع قراضه و طول قوس تعیین کرد. شکل 4 مراحل مختلف ذوب را با هندسه خراش مخروطی فرضی نشان می دهد.
شکل 4: هندسه شکسته مخروطی
برخی از سادهسازیها برای تسهیل محاسبه عوامل دید معرفی شدند. اینها شامل حذف الکترود و فاز گاز از انتقال حرارت تابشی و همچنین استخراج توابع تجربی برای تخمین عوامل دید است که با استفاده از عبارات تحلیلی موجود قابل تعیین نیستند.[34] لوگار و همکاران.[35] کار خود را بر اساس یک هندسه مشابه قرار دادند و محاسبه عوامل دید را برای کاهش تعداد تخمین های تجربی مورد استفاده تنظیم کردند. در آثار بعدی، فتحی و همکاران[39،42] و صبوحی و همکاران[43]. سطوح اضافی و سهم دینامیکی از تابش انرژی ساطع شده توسط قوس برای مطالعات دقیق تر از انتقال حرارت تابشی را قرار دادند. مایر و همکاران [13،36] نیز کار خود را بر اساس مدل لوگار انجام دادند و الکترود و فاز گاز شامل غبار را به محاسبات انتقال حرارت تشعشعی اضافه کردند. اپیتز و همکاران.[44] مجدداً تخمین لوگار از عوامل دید را پذیرفتند و تنظیمات متعددی مانند تأثیر گاز و غبار بر انتقال حرارت تشعشعی و نمایش دقیق تر بچ قراضه با چندین بخش جداگانه را معرفی کردند.
در مدل های فوق، تمام سطوح به جز قوس، اجسام خاکستری با دمای سطح یکنواخت فرض می شود. سهم گرمای منتقل شده از طریق تشعشع، همرفت، و حرارت مستقیم مذاب و ضایعات در قوس معمولا ثابت فرض می شود. یک مدل فرآیند توسط فتحی و همکاران.[39،42] بر اساس ضرایب دید محاسبه شده و در صورت در نظر گرفتن خواص گاز و غبار، تبادل حرارت تشعشعی را می توان کمی سازی کرد. فاکتورهای دید برای هندسه های ساده شده با استفاده از عبارات تحلیلی شناخته شده برای آرایش های ساده مانند سطوح استوانه، جبر ضریب دید و برخی فرضیات ساده کننده تخمین زده می شوند. هرناندز و همکاران [45،46] یک رویکرد متفاوت برای تخمین ضرایب دید برای مدلهای EAF بر اساس یک استوانه عمودی پیشنهاد کردند، که میتوان آن را به عنوان یک حالت افراطی از شکل شکسته مخروطی با زاویه مخروط 90 تعبیر کرد. روش مونت کارلو برای تعیین فاکتورهای نمای حاصل. هی و همکاران.[46] روش پیشنهادی مایر و همکاران [13،36] را با این هندسه تنظیم کرد و تخمین فاکتورهای دید را برای چندین پیکربندی سطحی خاص بهبود بخشید. رینگل[47] مدل دیگری را بر اساس مدل لوگار و همکاران[35،48] همراه با هندسه پیشنهادی هرناندز و همکاران توسعه داد.[45] و با نتایج مشابهی که توسط Hay و همکاران ارائه شده بود، عوامل دید را بر این اساس تنظیم کرد.[49]
سرباره کف کننده می تواند تأثیر قابل توجهی بر انتقال حرارت تابشی داشته باشد و مدل ها را می توان بر این اساس تنظیم کرد. . Oosthuizen و همکاران [50,51] یک محاسبه برای ارتفاع سرباره کف کننده به عنوان توسعه مدل ارائه شده توسط Bekker و همکاران معرفی کردند. بر این اساس، Rathaba [38] بسته به ارتفاع پیشبینیشده سرباره، تنظیم پارامتر بازده قوس را اضافه کرد. MacRosty و همکاران.[53] همچنین پیشبینی ارتفاع سرباره کفکننده را در مدل خود گنجانده و جریان گرمای تشعشعی را به دیوار و سقف تنظیم کردند تا محافظ قوس باشد. . لوگار و همکاران [35،54] از رویکرد مشابهی استفاده کردند اما در عوض عوامل دید را از قوس به دیوار و سقف تنظیم کردند، در حالی که مایر و همکاران [13،36] توزیع قدرت قوس را با کاهش سهم تابش و در عوض افزایش سهم گرمایش مستقیم مذاب با افزایش ارتفاع سرباره تنظیم کردند. به طور کلی، حتی مدلهای دقیقتر هنوز هم به سادهسازیهای قابل توجهی در رابطه با هندسه و تعریف سطوح و دماهای درگیر نیاز دارند. خطای ارائه شده توسط مفروضات و ساده سازی های انجام شده معمولاً اندازه گیری نمی شود و پدیده های محلی مانند تشکیل کانون ها به هیچ وجه با چنین رویکردهای ساده سازی شده قابل بازتولید نیستند.
اگر انتقال حرارت تشعشعی به طور مستقیم در یک مدل در نظر گرفته نشود، ممکن است به طور غیرمستقیم از طریق ضرایب انتقال حرارت تنظیم شده یا سایر پارامترهای مدل تجربی مانند راندمان تعریف شده در سطح جهانی یا جریان گرما نشان داده شود. جدول 2 نمای کلی از مدل های فرآیند و توضیحات پیاده سازی شده برای انتقال حرارت را نشان می دهد. برای چندین مدل، اطلاعات منتشر شده اجازه ارزیابی دقیق از پیاده سازی دقیق را نمی دهد و بنابراین فقط یک خلاصه کیفی از رویکردهای مربوطه فهرست شده است.
-
A Review of Mathematical Process Models for the Electric Arc Furnace Process-7
ذوب قراضه
گرمایش و ذوب ضایعات در داخل حمام فولادی و در مناطقی که مستقیماً توسط قوس و مشعل ها گرم می شوند باید در نظر گرفته شود تا مدل سازی دقیق ذوب ضایعات انجام شود. در حالی که شارهای حرارتی در ضایعات را می توان با استفاده از مدل های انتقال حرارت که قبلا توضیح داده شد تخمین زد، نرخ گرمایش و ذوب حاصل را نمی توان بر اساس جریان گرما به تنهایی تعیین کرد. ضایعات معمولاً به صورت یک منطقه تک تکهای مدلسازی میشوند، اما ذوب موضعی ضایعات را میتوان با تنظیم نرخ ذوب و حرارت به حساب آورد. از طرف دیگر، بار ضایعات را می توان به چندین ناحیه با رفتار ذوب متفاوت بر اساس موقعیت و ترکیب آنها تقسیم کرد.
5.1. ذوب ضایعات غوطه ور در فولاد مایع
ذوب ضایعاتی که در یک حمام فولادی مایع غوطه ور می شود نه تنها به EAF مربوط می شود بلکه به کوره اکسیژن پایه (BOF) نیز مربوط می شود و هم از طریق آزمایش ها و هم شبیه سازی های عددی به طور کامل مورد مطالعه قرار گرفته است. با مشاهده تغییر جرم و ترکیب، می توان پدیده ها و مدل های عددی مربوطه را برای هندسه های خاص تحت شرایط کنترل شده به دست آورد. محتوای کربن نمونه و حمام فلزی، دمای آنها، شرایط جریان در داخل حمام، و آرایش هندسی نمونهها تأثیر قابلتوجهی بر نرخهای حاصل از جرم، دما و تغییرات ترکیب دارند.[55،56،59،60]
مدلهای عددی برای بازتولید رفتار در آزمایشها با انواع نمونههای خاص [56،59،60] و شرایط درون مبدل BOF[58] یا EAF توسعه یافتهاند.[57] برای EAF، پدیده های اضافی مانند ذوب ضایعات در اطراف قوس ها و منابع انرژی شیمیایی مانند مشعل ها باید در نظر گرفته شوند.[57] علاوه بر آن، EAF معمولاً با بیش از یک سبد قراضه در هر گرما شارژ می شود، به این معنی که بر خلاف ضایعات BOF تازه روی شارژ قبلی و تا حدی ذوب شده شارژ می شود. این نیاز به مدلهای پیچیده و گسستهسازی برای در نظر گرفتن پدیدههای محلی دارد، که ترکیب چنین مدلهای دقیق برای ذوب ضایعات در مدلهای فرآیند EAF را دشوار میکند. علاوه بر این، بسیاری از پارامترها مانند شکل و ترکیب ضایعات یا شرایط جریان در حمام در بیشتر موارد نیاز به تخمین زدن دارند. بنابراین، رویکردهای ساده شده با تکیه بر معادلات تجربی در مدلسازی فرآیند EAF استفاده میشود.
5.2. مدل سازی فروگداخت در مدل های فرآیند EAF
برخی از سازندگان از یک پارامتر واحد استفاده می کنند که به عنوان تقاضای انرژی ویژه برای هر ماده باردار تعریف شده است و پیشرفت ذوب را با توجه به کسری از این انرژی که تا زمان کنونی عرضه شده است، تعیین می کنند.[30،61،62] شاه. و همکاران [63] از یک رویکرد مشابه با تقسیم مدل فرآیند شبه دینامیکی خود به مراحل فرآیند از پیش تعریف شده استفاده می کنند که ابتدا گرم کردن ضایعات تا دمای معین و سپس ذوب را در نظر می گیرد و برای مراحل نهایی، فولاد مایع را برای محاسبه تعادل شیمیایی فرض می کند. این رویکرد ساده تعادل انرژی عمدتاً برای تعیین پایان ذوب و نه برای توصیف پدیده های واقعی مانند تغییر هندسه به دلیل ذوب قراضه و تأثیر ناشی از آن بر جریان گرما استفاده می شود.
یکی دیگر از روش های ساده اما کمی دقیق تر، تقسیم کل جریان خالص گرما به منطقه(های) قراضه به یکی که برای گرم کردن ضایعات باقی مانده و دیگری برای ذوب استفاده می شود، است. سپس نرخ ذوب بر اساس کسر دوم و تغییر دما بر اساس کسر اول تعیین می شود. این کسری ها معمولاً با استفاده از یک معادله تجربی بر اساس دمای فعلی منطقه قراضه و دمای حمام یا دمای ذوب فولاد با میانگین محتوای کربن فرضی ضایعات محاسبه می شوند. هنگام تعیین توزیع در ذوب و گرمایش، ممکن است عوامل اضافی مانند انتقال برق فعلی مشعل ها و قوس ها نیز در نظر گرفته شوند. این رویکرد در مدلهای پیشنهاد شده توسط بکر و همکاران، [52] مکروستی و همکاران، [34] لوگار و همکاران، [48] و مدلهای مبتنی بر آنها استفاده شده است. لینینگر و همکاران.[37] هر دو گرمایش و ذوب را بر اساس گرمای ارائه شده به مناطق جامد بدون ارائه جزئیات بیشتر در مورد چگونگی تعیین نرخ های خاص ذکر می کنند.
توصیف دقیقتر نرخ ذوب و گرمایش را میتوان در مدل پیشنهاد شده توسط Matson و همکارانش یافت، [64] که در آن ضایعات به صورت کره نشان داده میشود و معادلات دیفرانسیل برای محاسبه توزیع دما و نرخهای ذوب و گرمایش حاصل از آن استخراج میشوند. نیسن و همکاران.[28] منطقه قراضه را به چند بخش با شرایط انتقال حرارت متفاوت بسته به مکان (غوطه ور در مذاب یا در تخته آزاد، موقعیت نسبت به قوس و مشعل ها و غیره) و ترکیب (که توسط لایه های انواع قراضه شارژ شده تعیین می شود) تقسیم می کنند. سپس یک نرخ ذوب خاص برای هر بخش محاسبه می شود. با این حال، روش دقیق تعیین گرمایش و ذوب در بخش های مختلف به طور دقیق توضیح داده نشده است. ساختار مناطق قراضه پیشنهاد شده توسط Nyssen و همکاران.[28] در شکل 5 نشان داده شده است.
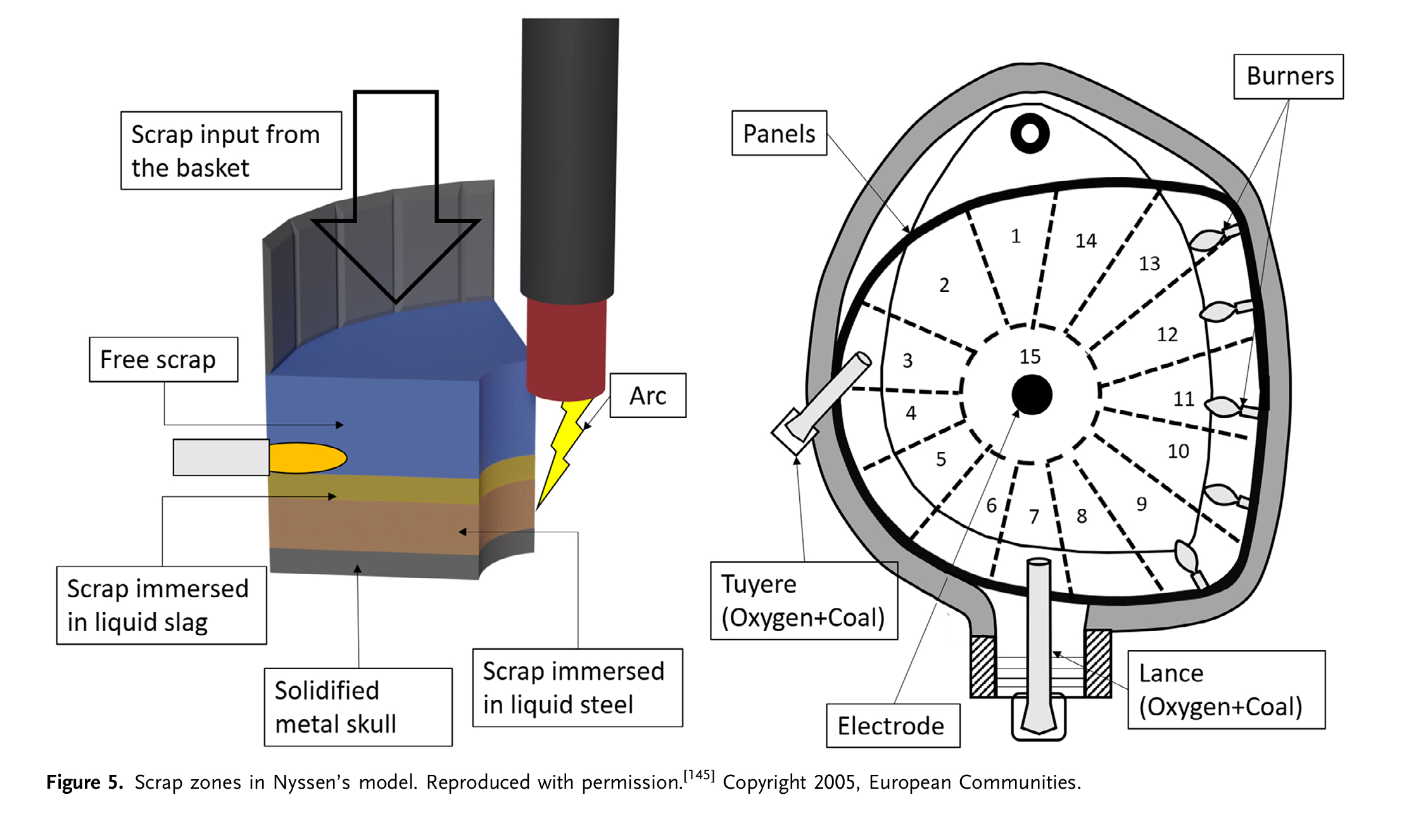
A Review of Mathematical Process Models for the Electric Arc Furnace Process-9
شکل 5: مناطق قراضه در مدل Nyssen
به طور مشابه، Opitz[29] از بخشهای مختلف در منطقه قراضه برای محاسبه جریانهای حرارتی موضعی استفاده میکند. برای هر منطقه جداگانه، یک رویکرد تعادل انرژی اجرا می شود، ابتدا تمام ضایعات داخل منطقه تا دمای ذوب گرم می شود و سپس به تدریج آن را ذوب می کند. هنگامی که یک بخش کاملاً مایع شد، محتویات به ناحیه مایع اضافه میشود و از ناحیه قراضه حذف میشود و در نتیجه یک پروفیل ذوب گسسته با تغییرات جرم ناپیوسته ایجاد میشود. مورالس و همکاران.[65] باری را که صرفاً از DRI تشکیل شده است در نظر می گیرند و نرخ ذوب تجربی را برای مدل آنها بدست می آورند.
رویکردهای مختلف اجرا شده برای ذوب ضایعات در مدل های فرآیند EAF در جدول 3 نشان داده شده است.
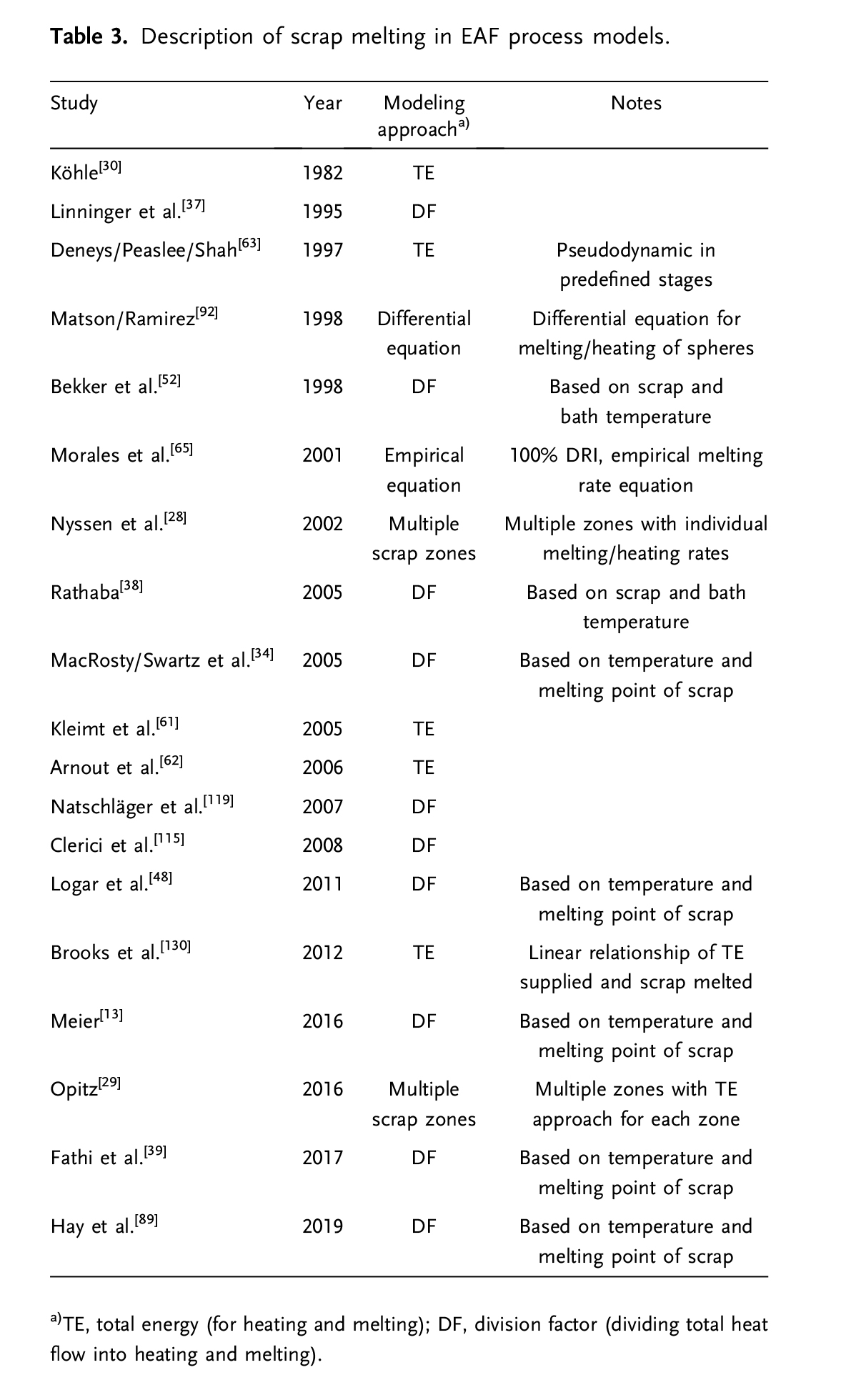
A Review of Mathematical Process Models for the Electric Arc Furnace Process-10
- ترموشیمی
تا نیمی از انرژی ورودی برای EAF توسط انرژی آزاد شده از طریق واکنشهای شیمیایی تامین میشود، [5،13] و به همین دلیل توصیفهای ترموشیمیایی بخشی ضروری از مدلهای فرآیند جامع برای EAF است. به طور خاص، توضیحات ترموشیمیایی برای تعیین اثر حرارتی مواد افزودنی و همچنین برای حل تعادل واکنش فلز-سرباره و تعادل فاز گاز در تخته آزاد مورد نیاز است.
6.1. اثر حرارتی ضایعات و مواد افزودنی دیگر
گرم شدن و ذوب شدن بارهای قراضه جزء اصلی انرژی مورد نیاز در کوره قوس الکتریکی را تشکیل می دهد. متأسفانه، همانطور که در بخش قبل ذکر شد، ترکیب، شکل، و چگالی ضایعات از یک بچ به بچ دیگر متفاوت است، که باعث می شود ضایعات یکی از متغیرترین پارامترها در این فرآیند باشد.[66] در نتیجه، مدیریت تنوع در خواص قراضه یک عامل کلیدی برای پردازش EAF قابل دوام از نظر فنی است.
برای EAF، تبدیل فاز اصلی ذوب قراضه است. تغییر آنتالپی مرتبط به گرمای نهان ذوب نیز گفته می شود. علاوه بر ضایعات، سایر مواد افزودنی و گازهای فرآیندی اثر خنک کنندگی ایجاد می کنند. تأثیر آنها بر تعادل حرارتی را می توان مشابه با قراضه محاسبه کرد. اگر ظرفیت گرمایی ویژه یک ماده اضافه شده مشخص نباشد، تخمین تقریبی از ظرفیت گرمایی ویژه را می توان با استفاده از قانون نیومن-کوپ به دست آورد.[67]
علاوه بر این، آنتالپی های انحلال احتمالی نیز باید به عنوان تبدیل فاز در نظر گرفته شوند. ظرفیت گرمایی ویژه معمولاً با چند جمله ای های وابسته به دما برای فواصل دمایی مختلف توصیف می شود. در عمل، برای مدلهای EAF معمول است که از یک توصیف سادهشده با در نظر گرفتن مقادیر cp بهعنوان ثابت در دما، که در پارامترهای ثابت توضیح داده شده در بخش قبل گنجانده شدهاند، استفاده کنند. به این ترتیب مقداری از هزینه های محاسباتی صرفه جویی می شود، در حالی که ساختار مدل تا حدودی ساده تر می شود.
6.2. تعادل واکنش فلز- سرباره
در طول فاز حمام مسطح، فلز مذاب شروع به واکنش با فاز سرباره می کند. به دلیل اختلاط ضعیف در ظرف EAF، شرایط جنبشی برای این واکنشها بیشتر از سایر فرآیندهای فولادسازی، مانند مبدلها یا ملاقهها، یک عامل محدودکننده است. در نوشته جات، روش های مختلفی برای محاسبه تعادل فلز- سرباره در فرآیند EAF استفاده شده است. روش ثابت تعادل برای سیستمهای واکنش نسبتاً ساده استفاده میشود، در حالی که تعادلهای فاز پیچیدهتر معمولاً با استفاده از کمینهسازی انرژی گیبس حل میشوند. صرف نظر از روش مورد استفاده، محاسبه تعادل فلز- سرباره نیاز به توصیف ترمودینامیکی گونه ها در فازهای فلزی و سرباره دارد. در مورد انرژی استاندارد واکنش گیبس، بسیاری از سازندگان از مقادیری استفاده کردهاند که میانگین بیش از درجه حرارت دارند. بنابراین یک منبع بالقوه خطا را القا میکنند. علاوه بر این، طرز عمل انرژی اضافی گیبس نیاز به توضیحاتی برای غیر ایده آل بودن فازهای فلزی و سرباره دارد. در حالی که مدلهای متعددی وجود دارد که تعادل فلز-سرباره را توصیف میکنند، بسیاری از آنها غیر ایدهآل بودن گونههای فلز و سرباره را در نظر نمیگیرند یا از رویکردهای تجربی صرف استفاده میکنند. خلاصه ای از شرح فعالیت های مورد استفاده در مدل سازی EAF در جدول 4 نشان داده شده است. بحث مفصلی در مورد رویکردهای مختلف برای فعالیت گونه ها در فازهای فلزی و سرباره در زیر ارائه شده است.
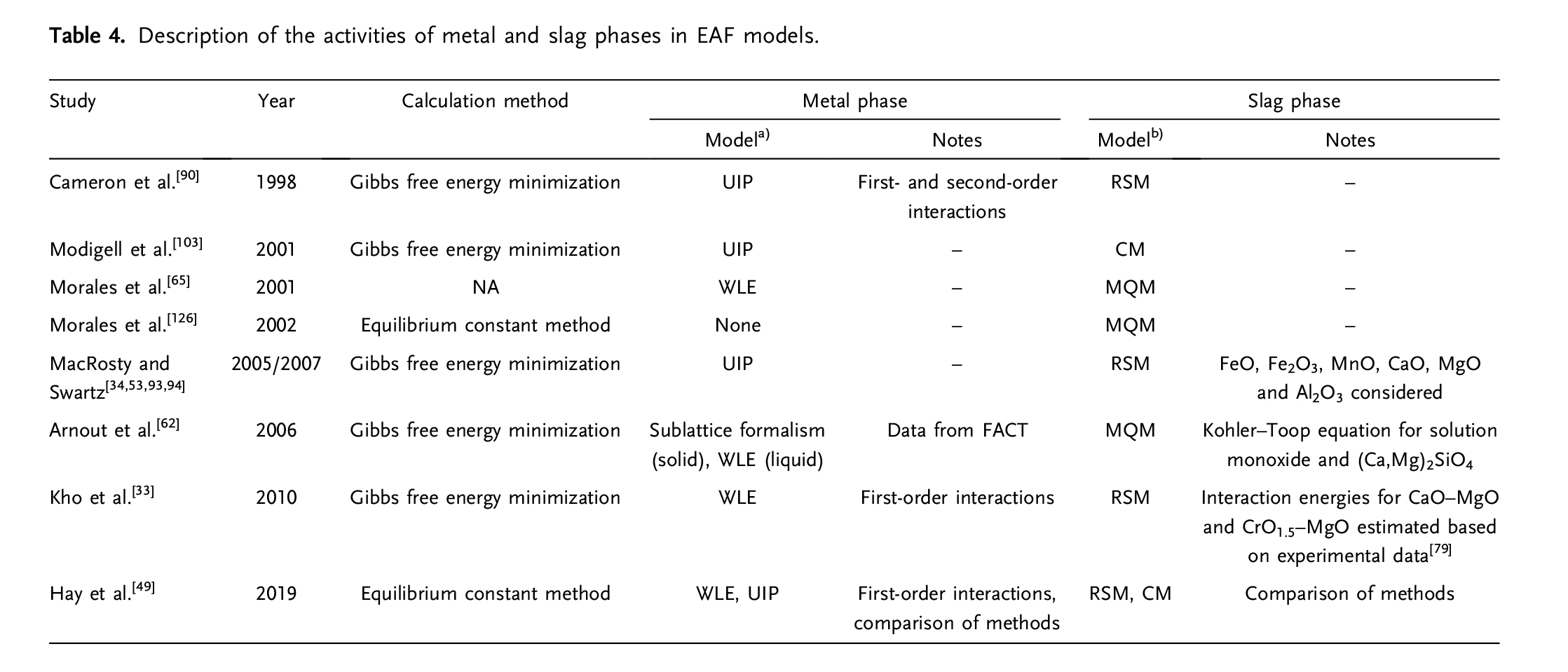
A Review of Mathematical Process Models for the Electric Arc Furnace Process-11
6.2.1. مدل های فعالیت برای فولاد مایع
در مورد محلولهای بینهایت رقیق، ضریب فعالیت هنری گونهها در فاز فلزی را میتوان با استفاده از فرمالیسم واگنر-لوپیس-الیوت (WLE) توصیف کرد، که بعداً برای حالت مرجع راولتی با استفاده از اصطلاحات مرتبه اول و دوم نشان داده شد.(68)
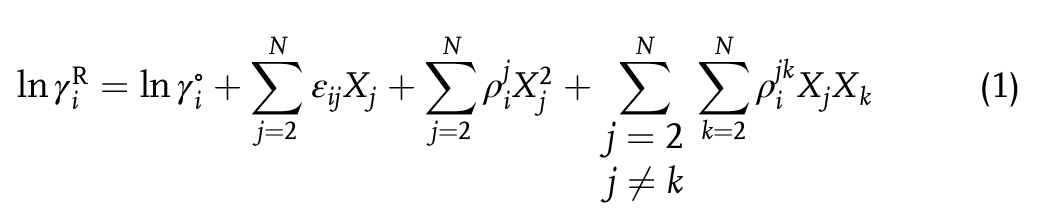
A Review of Mathematical Process Models for the Electric Arc Furnace Process-9-1
جایی که γ°i ضریب فعالیت در رقت بی نهایت است، εij پارامترهای برهمکنش مرتبه اول مولی هستند، X نشان دهنده کسر مول، و ρ پارامترهای برهمکنش مرتبه دوم مبتنی بر مولی هستند. لازم به ذکر است که در فرمالیسم WLE حلال (آهن) با شاخص 1 نشان داده میشود.
پلتون و بیل[69] با اشاره به اینکه فرمالیسم واگنر قانون گیبز-دوهم را برآورده نمیکند، یک عبارت اصلاحشده به نام فرمالیسم پارامتر تعامل یکپارچه (UIP) را پیشنهاد کردند که هم برای محلولهای رقیق و هم برای محلولهای غیررقیق قابل اجرا است. با استفاده از عبارت های مرتبه اول و دوم، ضریب فعالیت راولتین برای هر حل شونده(i=1,….N) را می توان با استفاده از دو معادله زیر محاسبه کرد.

A Review of Mathematical Process Models for the Electric Arc Furnace Process-10-01

A Review of Mathematical Process Models for the Electric Arc Furnace Process-10-02
که γsolvent حلال ضریب فعالیت حلال است و εjkl پارامترهای برهمکنش مرتبه دوم مولی هستند. فرمالیسم UIP به طور گسترده در پایگاه های داده ترمودینامیکی برای محلول های آهن مایع رقیق استفاده شده است. فرمالیسم پارامتر برهمکنش را به دست میآورد که توضیحات کمی جزئیتر برای حلال و برهمکنش املاح ارائه میدهد.
از آنجایی که اصطلاحات مرتبه دوم یا بالاتر همیشه برای همه سیستمهای مورد علاقه در دسترس نیستند، معمولاً در مدلسازی ریاضی فرآیندهای واحد نادیده گرفته میشوند. مجموعهای از پارامترهای تعامل مربوط به فولادسازی EAF به آسانی در نوشته جات موجود است.[73،74]
همانطور که در جدول 4 نشان داده شده است، رویکردهای مورد استفاده بیشتر فرمالیسم های WLE و UIP هستند. به دلیل فرمول بندی ساده آنها، هر سه مدل (WLE، [68] UIP، [69] و فرمالیسم ε توسط Ma و همکاران [72]) ارائه شده از نظر محاسباتی سبک هستند و تنها به حداقل تلاش برنامه نویسی نیاز دارند. با توجه به نتایج Hay و همکاران [49]، ضعفهای نظری آشکار فرمالیسم WLE در مقایسه با فرمالیسم UIP تأثیر کمی بر نتایج شبیهسازی در زمینه مدلسازی ریاضی فرآیند EAF دارد. در این میان، توصیف خواص ترمودینامیکی ضایعات جامد بسیار کمتر مورد توجه قرار گرفته است. در مدل Arnout و همکاران [62] محلول های ضایعات، fcc جامد و bcc جامد با استفاده از مدل زیرشبکه توصیف شدند.
6.2.2. مدل های فعالیت برای سرباره
از نقطه نظر ترمودینامیک، سرباره های سیلیکات را می توان به عنوان مایعات یونی با ساختار شبکه ای پیچیده در نظر گرفت.[70] مروری دقیق بر کاربرد مدلهای ترمودینامیکی برای سربارههای مذاب در پایگاههای اطلاعاتی ترمودینامیکی توسط یونگ منتشر شد.[70] علاوه بر آن ها، توصیف های ساده تری اغلب در مدل سازی ریاضی فرآیندها استفاده می شود.
همانطور که در جدول 4 نشان داده شده است، مدلهای اصلی مورد استفاده در مدلسازی EAF معاصر، مدل حل معمولی (RSM)، مدل سلولی [75]، [76] و مدل شبه شیمیایی اصلاحشده (MQM) هستند.[69،77] RSMسادهترین مدل است، که فرض می کند تمام کاتیون های موجود در مذاب سیلیکات به طور مساوی در ماتریکسی که توسط آنیون های اکسیژن تشکیل شده است، توزیع می شوند.[75] ضریب فعالیت گونه i به صورت زیر بیان می شود[75]

A Review of Mathematical Process Models for the Electric Arc Furnace Process-10-03
جایی که α نشان دهنده انرژی برهمکنش بین کاتیون ها است، X کسر کاتیونی است و I’ضریب تبدیل بین محلول فرضی منظم و محلول واقعی است. مقادیر جدولبندی شده برای انرژیهای تعامل و عوامل تبدیل در سیستمهای مربوط به فولادسازی [75] و فولاد ضد زنگ [78] در نوشته جات موجود است. انرژیهای متقابل مشتقشده توسط Kho و همکاران [33] برای CaO-MgO و CrO1.5-MgO بر اساس دادههای Pei و Wijk [79] گزارش نشد.
مدل سلولی پیشنهاد شده توسط کاپور و فروهبرگ [76] فرض میکند که مذاب سرباره مخلوطی از سلولهای تشکیلشده توسط دو کاتیون است.
به عنوان مثال، سیستم M-SiO2 را می توان با استفاده از سلول های M-O-M، M-O-Si، و Si-O-Si توصیف کرد، که واکنش شکست شبکه را می توان به صورت زیر ارائه کرد [70]

A Review of Mathematical Process Models for the Electric Arc Furnace Process-11-1
که برای آن تغییر انرژی آزاد متناظر با ΔG= 2WSi–M تعریف می شود، که در آن WSi-M انرژی تشکیل سلول است. این مدل به عنوان پارامترهای اصلی، انرژی تشکیل سلول (WSi-M و انرژی برهمکنش سلولی (ESi-M)، که به عنوان تابعی از ترکیب و دما تعریف می شوند، استفاده می شود.[70]
MQM پیشنهاد شده توسط پلتون و بلاندر[69] بر اساس نظریه شبه شیمیایی گوگنهایم است.[80] شبیه به مدل سلولی، مدل MQM به صراحت رفتار ترتیبی مذاب های سیلیکات را در خواص وابسته به ترکیب مذاب ها به حساب می آورد.[70] پارامتر اصلی مدل، انرژی گیبس واکنش گسست شبکه (depolymerization) است که با استفاده از یک تابع چند جمله ای تجربی ترکیب و دما تعریف می شود. در انتشارات بعدی، MQM بهبود یافته است[81] و به راهحلهای چند جزئی[82] و دو سیستم زیرشبکه با برهمکنشهای نزدیکترین و نزدیکترین همسایه گسترش یافته است. [70] برای مثال، در مدل Arnout و همکاران [62]، MQM با استفاده از کتابخانه معمولی ChemApp پیاده سازی شد. در مطالعه آنها مونوکسید محلول و (Ca,Mg)2SiO4 با استفاده از تکنیک برون یابی نامتقارن کهلر-توپ [85] مدلسازی شدند. انتخاب این رویکرد رفتار پیچیده سیلیکون در سرباره ها را برجسته می کند.
6.3. تعادل فاز گاز در فری برد
هر دو واکنش همگن و ناهمگن در جو EAF انجام می شود. اینها عبارتند از احتراق متان، واکنشهای همگن و ناهمگن جابجایی آب-گاز (WGS)، واکنش بودوار، و اکسیداسیون کربن توسط اکسیژن. مجموعه ای از رفتار واکنش های فاز گاز در مدل های ریاضی برای فرآیند EAF در جدول 5 نشان داده شده است. لازم به ذکر است که بسیاری از نشریات جزئیات کافی برای ارزیابی نحوه برخورد ریاضی با واکنش ها ارائه نمی دهند.
محاسبات لینینگر و همکاران.[37] نشان می دهد که سرعت جریان حجمی و ترکیب گاز خروجی به طور قابل توجهی در طول فرآیند EAF متفاوت است، در حالی که دمای گاز خروجی به تدریج به سمت پایان فرآیند افزایش می یابد. نوسانات در نرخ جریان گاز خروجی عمدتاً به استفاده از مشعل ها و لنس های اکسیژن و همچنین هوای نشتی مربوط می شود.[37] اجزای اصلی گاز اگزوز N2 و CO هستند.
رویکردهای محاسبه تعادل در فریبورد متفاوت است. مدلهای متسون و همکاران.[64] و فریتلا و همکاران.[86] و همچنین مدل مایر و همکاران [13,87] و توسعه بیشتر آن توسط Hay و همکاران [88,89] از روش ثابت تعادل استفاده می کنند. دنیز و همکاران، [31] شاه و همکاران، [63] کامرون و همکاران، [90] ماتسون و همکاران، [91،92] مک روستی و سوارز، [34،53،93،94] آرنوت و همکاران ، [62] و خو و همکاران [33] همه از کمینه سازی انرژی گیبس برای تعیین تعادل فاز گاز در فریبورد استفاده می کنند.
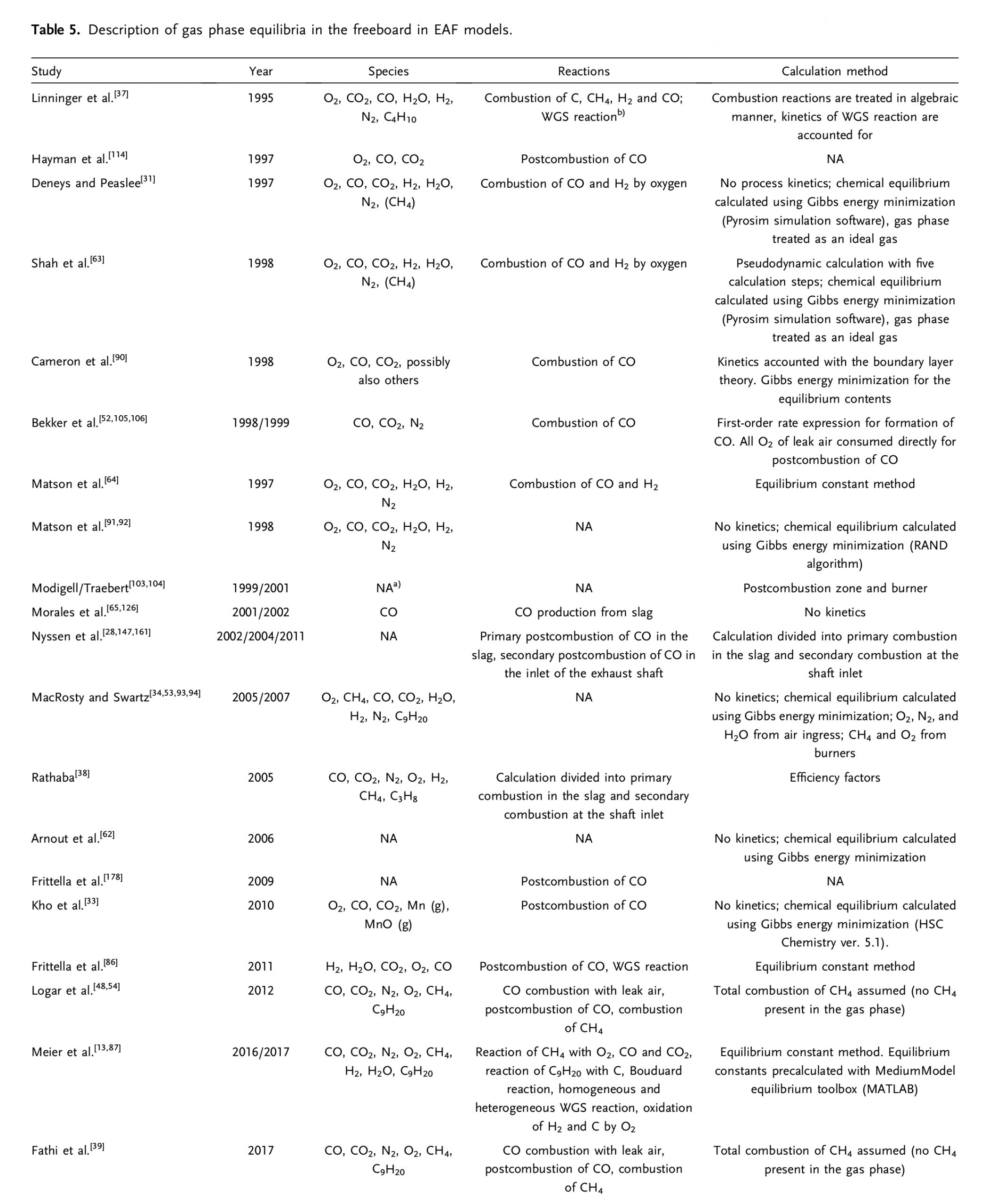
A Review of Mathematical Process Models for the Electric Arc Furnace Process-12
6.4. رفتار های جنبشی
یکی از چالشهای مدلسازی فرآیند EAF، دشواری تعیین نواحی واکنش و «سادهسازیهای هندسی» مناسب برای بیان ریاضی آنها است. به همین دلیل، مدلهای پیشنهادی بیشتر از رویکرد حجم واکنش استفاده میکنند، که در آن سینتیک فرآیند با مدلسازی تبادل جرم بین حجمهای تعادلی توصیف میشود. شکل 6 یک مثال معمولی از تعریف مناطق مختلف و تبادل بین آنها را نشان می دهد. متأسفانه، این رویکرد تأثیر مقاومتهای انتقال جرم میکروسینتیکی را بر تعادل ترمودینامیکی محلی در نظر نمیگیرد.
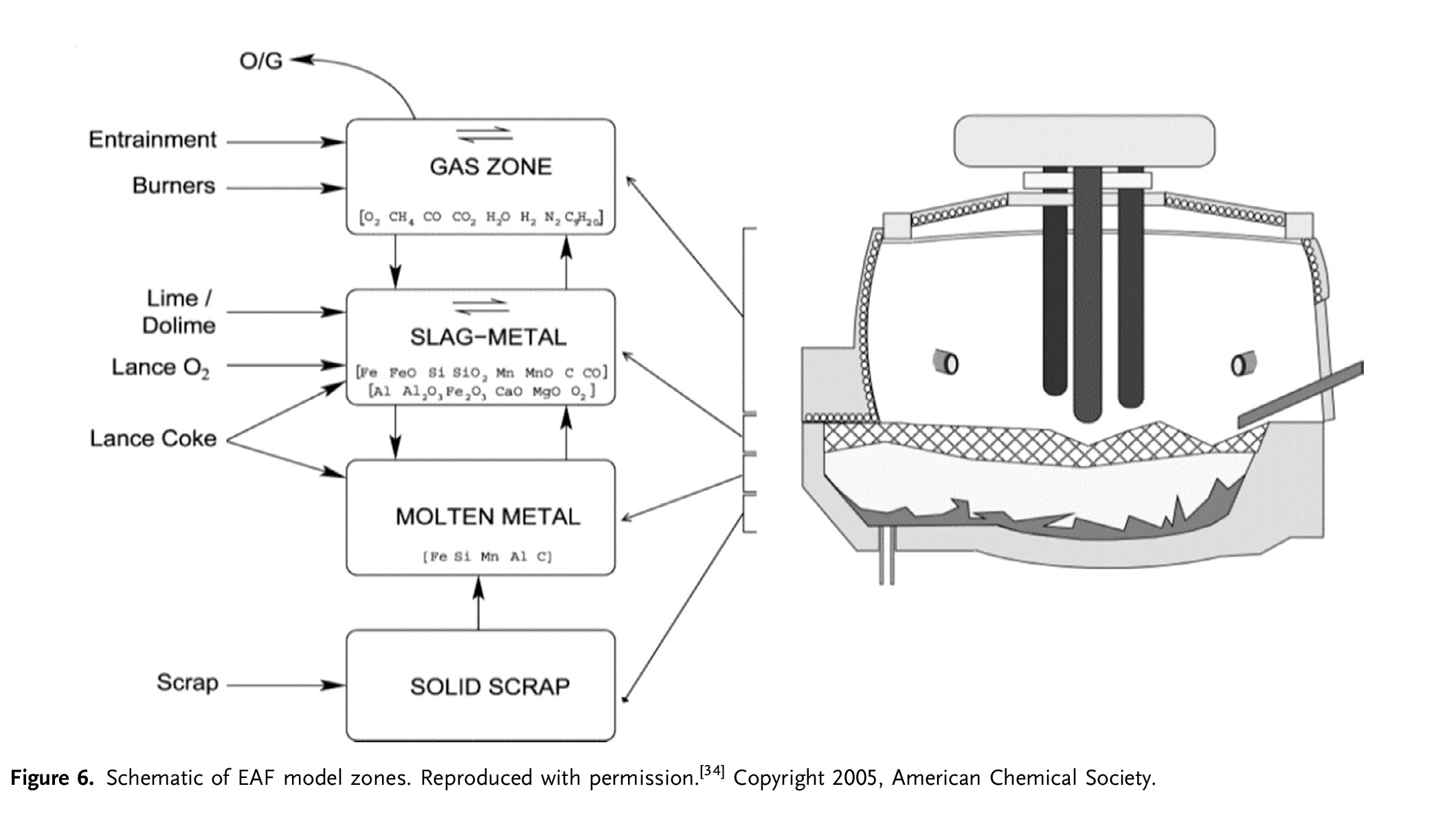
A Review of Mathematical Process Models for the Electric Arc Furnace Process-13 copy
شکل 6: شماتیک مناطق مدل EAF
6.4.1. رفتار جنبشی واکنش های فلز- سرباره
سینتیک مرتبه اول توسط چندین سازنده برای توصیف انتقال جرم فلز- سرباره استفاده شده است. اینها شامل مدلهای کامرون و همکاران، [90] هی و همکاران، [49] و مکروستی و سوارتز میشوند.[34،53] در این مدلها واکنشها از طریق ترکیب در رابط واکنش تعیین میشوند. در نتیجه، تغییر جرم گونه i به سادگی توسط

A Review of Mathematical Process Models for the Electric Arc Furnace Process-13-2
که در آن m˙ کل جریان جرمی بین حجم های واکنش است. این نوع فرمولبندی فرض میکند که نرخ با انتقال جرم کنترل میشود، اما در مورد عواملی که ممکن است بر آن تأثیر بگذارد موضعی اتخاذ نمیکند. از آنجایی که واکنشهای فلز- سرباره واکنشهای ناهمگنی هستند، معمولاً با انتقال جرم به دلیل دماهای بالا کنترل میشوند. برای اهداف مدلسازی ریاضی، معمولاً مجاز است فرض کنیم که مقاومت انتقال جرم به طور کامل در لایه مرزی انتشار بین فازها قرار دارد. این رویکرد برای اولین بار توسط Nernst [95] در سال 1904 ارائه شد. در برخی موارد، مقاومت های واکنش در هر دو فاز به یک اندازه است و هر دو باید در نظر گرفته شوند. مقاومت کلی محدودیتهای انتقال جرم در دو فاز را میتوان با استفاده از نظریه دو فیلم لوئیس و ویتمن،[96] که میتواند برای واکنشهای کنترلشده انتقال جرم رقابتی نیز گسترش دهد، به صورت تحلیلی حل میشود.[97] با این وجود، اغلب اوقات انتخاب روش حل عددی بسیار ساده تر و انعطاف پذیرتر است. بحث مفصلی در مورد رویکردهای موجود توسط Järvinen و همکاران ارائه شده است.[98] یک چالش عمده برای رویکرد لایه مرزی عدم قطعیت مربوط به ناحیه سطحی است. مورالس و همکاران.[65] منطقه سطحی فلز- سرباره را بر اساس همبستگی انرژی تکان دهنده تملیس و ژائو تعریف کردند[99] برای اکثر مدلهای دیگر، ناحیه سطحی به طور ضمنی در پارامترهای مدل تجربی قرار دارد. تاکنون تلاشهای کمی برای مدلسازی واکنشهای درون فوم در فرآیند EAF صورت گرفته است. در اصل، توصیفهایی مشابه آنچه در مدلهای اخیر BOF استفاده میشود [100-102] میتواند اتخاذ شود. با این وجود، هنوز اطلاعات بیشتری برای تشکیل فوم در فرآیند EAF مورد نیاز است.
6.4.2. رفتار جنبشی واکنش های فاز گازی
هر دو واکنش همگن و واکنش فاز گاز ناهمگن در EAF انجام می شود. مدلهای Deneys و Peaslee، [31] Sha و همکاران، [63] Matson و همکاران، [91،92] Modigell و همکاران، [103،104] MacRosty و Swarz، [34،53،93،94] Arnout و همکاران [62] و خو و همکاران [33] به هیچ وجه سینتیک واکنش های فاز گاز را در نظر نمی گیرند. کامرون و همکاران [90] از تئوری لایه مرزی برای تعیین دبی جرمی بین نواحی تعادلی استفاده کردند. Bekker و همکاران [52,105,106] فرض کردند که تمام اکسیژن موجود در هوای نشتی به طور کامل در پس احتراق CO واکنش نشان می دهد. این بدان معناست که تنها محدودیتهای جنبشی برای واکنشهای فاز گاز، نرخ تشکیل CO (که فرض میشد از سینتیکهای مرتبه اول پیروی میکند) و نرخ نشت هوا بود. به طور مشابه، لوگار و همکاران [48،54] پس از احتراق CO را در تخته آزاد در نظر می گیرند و احتراق کل CH4 را که از طریق مشعل ها اضافه می شود، فرض می کنند. Meier و همکاران [13،87،107] و بر اساس آن Hay و همکاران [49،89] واکنش های بی نهایت سریع برای سوزاندن CH4 در مشعل های اکسی سوخت و واکنش های جنبشی محدود در داخل تخته آزاد و همچنین واکنش های ناهمگن محدود همانند واکنش بودوار بر اساس پارامترهای تجربی و ثابت های تعادل را فرض می کنند.. واکنش های مختلف CH4 در نظر گرفته شده توسط Meier [13] در شکل 7 نشان داده شده است.
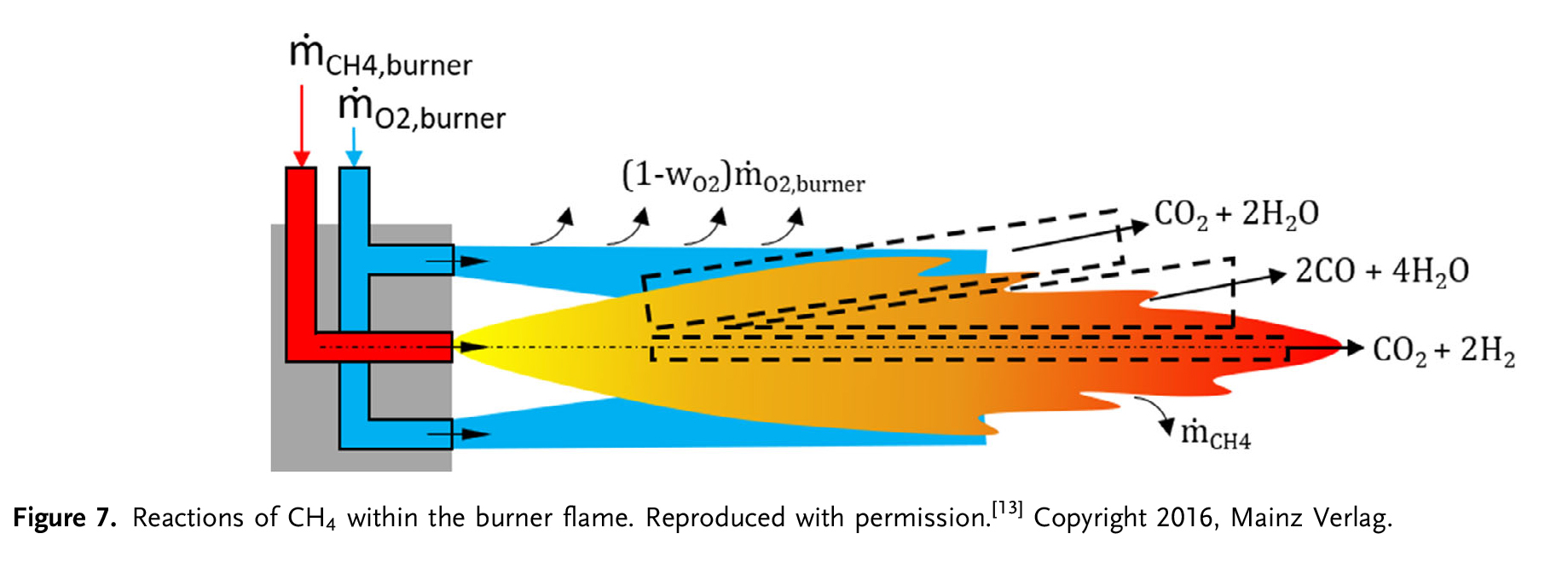
A Review of Mathematical Process Models for the Electric Arc Furnace Process-14-01
شکل 7: واکنش های CH4 در شعله مشعل
6.4.3. رفتار جنبشی تزریق کربن و اکسیژن
هنگامی که ذرات کربن به سرباره کفکننده تزریق میشوند، با CO2 در داخل حبابهای گاز اطراف خود واکنش نشان میدهند و CO را تشکیل میدهند. بخشی از این CO سپس اکسیدهای سرباره (به عنوان مثال، اکسیدهای آهن) را کاهش میدهد و CO2 تولید میکند که همانطور که در شکل 8 نشان داده شده است، به نوبه خود میتواند دوباره با ذره کربن واکنش دهد.

A Review of Mathematical Process Models for the Electric Arc Furnace Process-14
شکل 8: واکنش های حین تزریق کربن به سرباره
تبدیل ذرات کربن به شرایط مختلف فرآیند از جمله اندازه و زمان ماندن ذرات کربن، شرایط تزریق، شیمی سرباره و دما بستگی دارد.[21] نمای کلی مدلهای واکنش و مطالعات تجربی در مورد تزریق کربن به سربارههای EAF توسط King[108] و Zhu ارائه شده است.[109]
اکثر مدل های EAF پیشنهاد شده در نوشته جات ، تبدیل کامل کربن تزریق شده را فرض می کنند. در ساده ترین حالت، همانطور که در مدل های Bekker و همکاران، [106] Rathaba، [38] و Logar و همکاران، [48،54] پیاده سازی شده است، این بدان معنی است که کربن تزریق شده به طور کامل برای کاهش FeO مصرف می شود. شرح مفصلی از سینتیک کاهش FeO توسط تزریق کربن توسط مورالس و همکاران [22] ارائه شد، که همچنین برای نفوذ جت مرتبط در ویژگیهای مایع و جفت – جداسازی بین گاز حامل و ذرات جامد توضیح داده شد. بعدها مورالس و همکاران.[65] از مدل کاهش FeO به عنوان بخشی از مدل ریاضی اساسی خود برای ذوب DRI در EAF استفاده کردند. در مدلهای Matson و همکاران [64،91،92] Modigell و همکاران، [103] MacRosty و Swarz، [53] Arnout و همکاران [62] و Kho و همکاران [33] یک تبدیل کامل کربن نیز در نظر گرفته شده است، اما تزریق کربن به عنوان یک جریان ورودی به یک راکتور تعادلی در نظر گرفته می شود، در نتیجه به کربن اجازه می دهد تا با گونه هایی غیر از FeO واکنش دهد.
همانند تزریق کربن به سرباره، واکنش های حاصل از تزریق اکسیژن به حمام فلزی پدیده پیچیده ای را ارائه می دهد. لوگار و همکاران [48،54] از ضرایب توزیع اکسیژن ثابت برای تعیین توزیع اکسیژن تزریقی به گونه های محلول در حمام فلزی استفاده کردند. نقطه ضعف این رویکرد این است که وقتی ضرایب توزیع اکسیژن در طول زمان ثابت نگه داشته می شود، بخشی از پویایی فرآیند به ناچار از بین می رود. علاوه بر این، بعید است که ثابت ها برای مجموعه داده های مختلف معتبر باشند. بکر و همکاران.[106] فرض کردند که تمام اکسیژن تزریق شده ابتدا به FeO تبدیل می شود، که به عنوان یک محصول واکنش واسطه عمل می کند و بعداً با واکنش های بعدی به طور جزئی یا کامل کاهش می یابد. این رویکرد در مدل سازی BOF نیز به کار گرفته شده است.[110] مشابه تزریق کربن، تزریق اکسیژن به عنوان یک جریان ورودی به یک راکتور تعادلی در مدلهای Matson و همکاران، [64،91،92] Modigell و همکاران، [103] MacRosty و Swarz، [34] Arnout et al. همکاران [62] و خو و همکاران [33] در نظر گرفته شده است.
- اعتبار سنجی
آموزش و اعتبارسنجی یک مدل EAF به دلیل دسترسی محدود به اطلاعات آنلاین، یک کار چالش برانگیز است. دمای بالای اتمسفر کوره، تشعشعات رشته ای از قوس الکتریکی، جریان های مغناطیسی بالا و ارتعاش مداوم پوسته کوره، استفاده از سنسورهای اندازه گیری در مجاورت کوره را محدود می کند. بیشتر دادههای پیوسته موجود مربوط به مرزهای مدل EAF، یعنی دما و ترکیب گاز، گرادیان دمای آب خنککننده پانل جانبی و پارامترهای منبع الکتریکی است. ترکیب و دمای مذاب و سرباره فولاد را میتوان از طریق نمونهبرداری روتین پروب به دست آورد، که اطلاعات گسستهای به ویژه در اعتبارسنجی نتایج نهایی مدل فرآیند مفید است.
رویکرد اعتبارسنجی مدلهای EAF به هدف مدل بستگی دارد. مدل های EAF در نظر گرفته شده برای اهداف آموزشی اعتبار سنجی نشده اند یا نتایج اعتبار سنجی ارائه نشده است.[33,111,112] به همین ترتیب، برای بسیاری از مدلهای تجاری مورد استفاده، دادههای مورد استفاده برای اعتبارسنجی آنها فاش نمیشود. [37،113-122] در برخی از مطالعات، [49،88،89] داده های مورد استفاده نرمال شده اند ، که مقایسه دقت مدل را پیچیده می کند.
به طور معمول، پارامترهای اصلی که باید تنظیم یا برازش شوند با سینتیک فرآیند مرتبط هستند. اساسی ترین نوع اعتبارسنجی انجام یک مطالعه موردی است که در آن یک مقایسه اکتشافی بین گرمای شبیه سازی شده و گرمای انتخاب شده از یک EAF صنعتی انجام می شود. یک رویکرد اعتبارسنجی رایج که در اکثر مدل های غیرتجاری ارائه شده استفاده می شود [27,35,38,42,43,48,54,62,65,103,104,125-133] فرمول بندی یک مدل فیزیکی با داده های نوشته جات و اعتبارسنجی آن با استفاده از داده های نقطه ای از دوره پالایش یا بهره برداری از EAFصنعتی است.در حالی که دما و ترکیب فولاد و سرباره ارتباط بالایی با عملیات EAF دارند، فقدان متغیرهای پیوسته در آموزش و اعتبارسنجی مدل، تجزیه و تحلیل منابع خطا را دشوارتر میکند و اعتبارسنجی نتایج را در طول گرما بسیار چالش برانگیز میکند. علاوه بر این، مجموعه دادههای جداگانه اغلب مورد استفاده قرار نمیگیرند یا حداقل بهطور خاص برای آموزش و اعتبارسنجی منتشر نمیشوند، و روند نحوه تنظیم مدل و انتخاب مجموعه داده اعتبارسنجی را مبهم میسازد.
فقدان دادههای پیوسته برای ترکیب فولاد و سرباره چالشی را برای سایر فرآیندها در متالورژی اولیه و ثانویه فولادسازی ایجاد میکند و به ندرت دادهها تا حدی عمومی هستند که میتوانند برای اعتبارسنجی توسط سایر سازندگان استفاده شوند. برای مثال، مدلهای چندفیزیکی اخیر برای فرآیند BOF به دلیل تکیه بیش از حد بر مجموعه دادههای مشابه در اعتبارسنجی خود مورد انتقاد قرار گرفتهاند.[134] در مورد مدل سازی EAF، حتی استفاده از چنین مجموعه داده مرجع عمومی گامی مهم به جلو در مقایسه بیشتر نتایج مدل خواهد بود.
استفاده از مدلها برای مناطق مختلف EAF اعتبار مدل را با دادههای پیوسته نیز فعال کرده است. [13،36،48،49،52،61،87-90،106،107،135-143] پرکاربردترین داده های پیوسته، دمای یا ترکیب خارج از گاز هستند. می توان از آن برای اعتبارسنجی مدل های در نظر گرفته شده برای بهینه سازی مشعل ها، سیستم های تزریق یا پس از احتراق استفاده کرد. [13,30,36,52,87,90,106,107,135,136,142,143] مدلهای در نظر گرفته شده برای محاسبات کلی تراز انرژی EAF ارائه شده توسط Logar و همکاران [35،48،54] Meier و همکاران [13،36]، Hay و همکاران. ، [49،88،89] و Opitz [29] نیز با استفاده از دماهای پیش بینی شده و اندازه گیری شده پانل جانبی و آب خنک کننده سقف تایید شدند. اکثر مدل های EAF حداقل برخی از پارامترهای منبع تغذیه را به عنوان متغیرهای ورودی در نظر می گیرند، اما تعداد کمی از آنها مقادیری مانند ولتاژ، جریان یا مصرف انرژی الکتریکی را پیش بینی می کنند و آنها را در اعتبارسنجی مدل در نظر می گیرند. مایر الگوریتمی را برای تولید خودکار نمودارهای عملیاتی بر اساس ورودی ضایعات، سرباره سازها و زغال سنگ و همچنین شرایط نقطه پایانی مورد نظر توسعه داد.[143] توسعه این الگوریتم توسط هی و همکاران ادامه یافت.[89] در هر دو مطالعه، پروفیلهای توان پیشبینیشده با مقادیر اندازهگیری شده برای گرما با ورودیهای مشابه مقایسه شد.[89] در همین حال، Logar.[35،48،54،131،132] و Opitz و همکاران [29،40،41،44،144] مدل های پیچیده ای از سیستم الکتریکی را در مدل های فرآیندی خود گنجانده اند که قادر به پیش بینی جریان و ولتاژ قوس بر اساس شیر ترانسفورماتور انتخاب شده هستند. هر دو مدل های الکتریکی خود را با داده های الکتریکی پیوسته تأیید کرده اند.[29,131] برخی از محققان همچنین از اندازهگیریهای پیوسته جدید برای اعتبارسنجی مدلهای خود استفاده میکنند. مورالس و همکاران [65,126] از پارامتر اعوجاج قوس اندازهگیری شده با سنسور صوتی در اعتبارسنجی شاخص فوم پویا استفاده کردند. Kleimt و همکاران [61,137-141] اعتبارسنجی دمای حمام را با مقایسه نتایج مدل با اندازهگیری دمای آنلاین با فیبرهای نوری انجام دادند. Nyssen و همکاران [28,145-148] اندازهگیریهای تصویربرداری از جریان ضربهگیری سرباره را انجام دادند که برای اعتبارسنجی مقدار سرباره محاسبهشده توسط مدل فرآیند استفاده شد. علاوه بر این، نیسن و همکاران، اندازه گیری های فاصله انجام شده بر روی ضایعات ذوب را برای ارزیابی اعتبار دمای مذاب محاسبه شده، در نظر گرفتند.
گردآوری منابع مختلف داده های اعتبار سنجی استفاده شده در جدول 6 نشان داده شده است. منابع داده های اعتبار سنجی همانطور که منتشر شده اند تفسیر شده اند و در صورت امکان، چندین اثر مربوط به یک مدل ترکیب شده اند.
نمونهای از اعتبارسنجی با استفاده از دادههای پیوسته را میتوان در محتوای CO اندازهگیریشده و شبیهسازیشده از گاز خارج از گاز که توسط Meier منتشر شده است، [13] همانطور که در شکل 9 نشان داده شده است، مشاهده کرد.
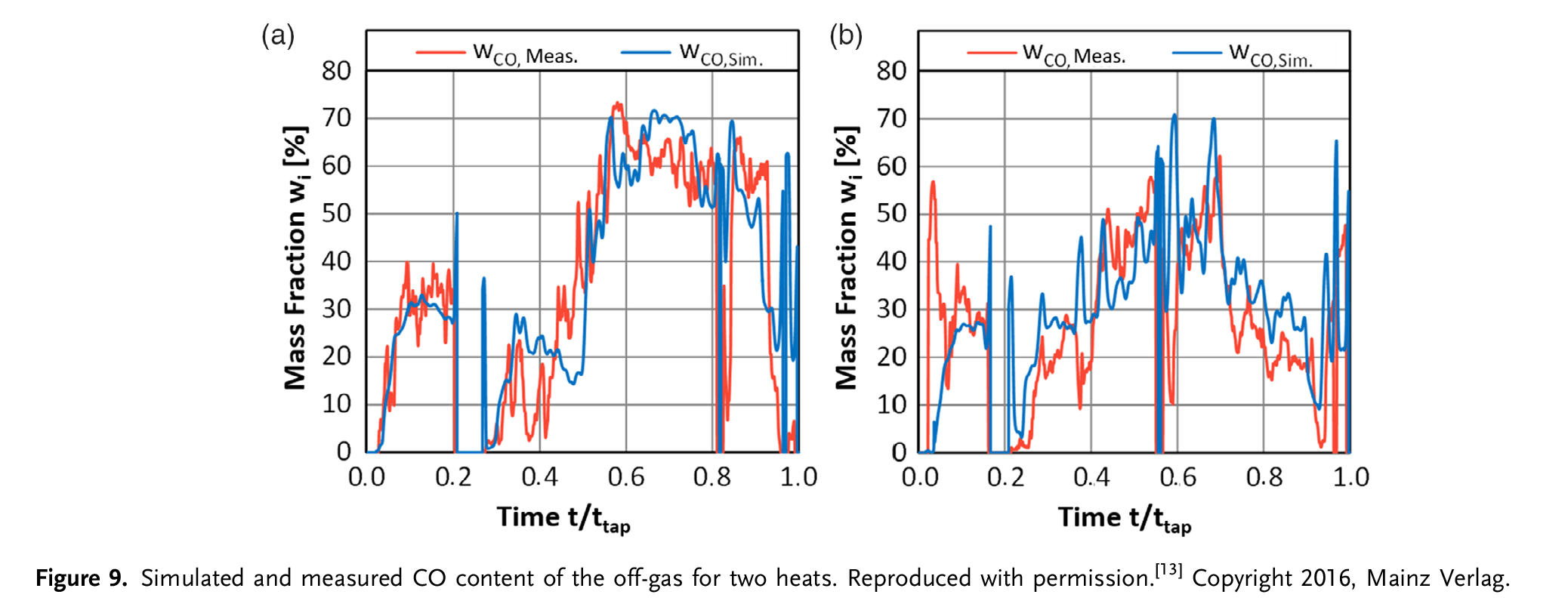
A Review of Mathematical Process Models for the Electric Arc Furnace Process-16-02
شکل 9: شبیه سازی و اندازه گیری محتوای CO از گاز خارج شده برای دو گرما
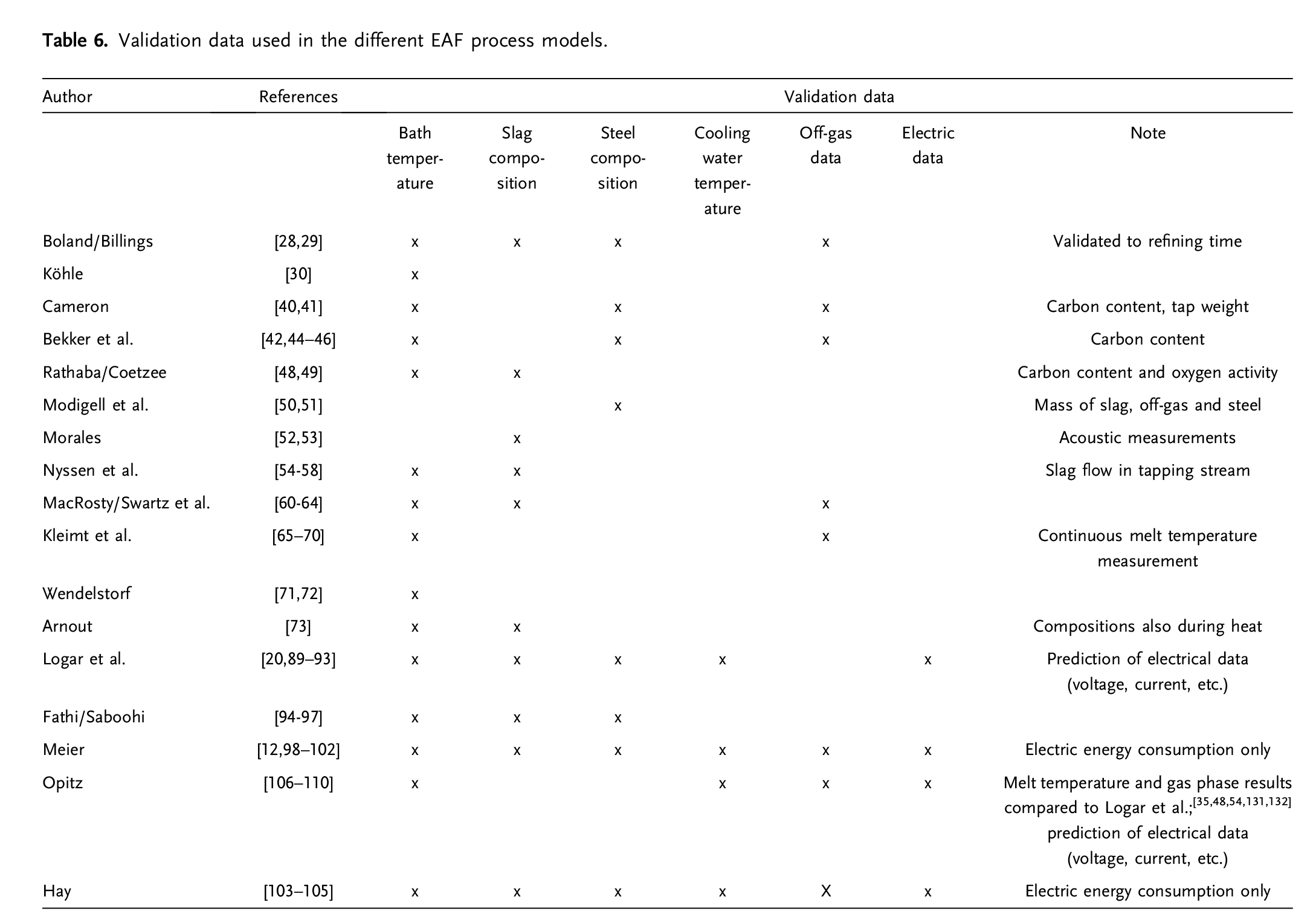
A Review of Mathematical Process Models for the Electric Arc Furnace Process-16
- بحث
جدای از حوزههایی که تاکنون مورد بحث قرار گرفت، مدلهای مختلف در جنبههای دیگری مانند تعداد و تعریف مناطق، الگوریتم حلکننده و تمرکز و هدف خاص آنها متفاوت هستند. در حالی که رویکرد استفاده از مناطق تودهای برای مدلهای فرآیندی رایج است، تعریف دقیق مناطق مختلف، مرزهای سیستم و سینکهای اضافی یا منابع جرم یا انرژی بسیار متفاوت است. مدلهایی که عمدتاً به سمت تخمین مصرف کلی انرژی یا کنترل نقطه پایانی هدف قرار میگیرند ممکن است فقط از یک منطقه و پارامترهای تجربی برای تعریف تلفات انرژی استفاده کنند. برخی دیگر از مناطق اضافی با تعادل گرما و جرم جداگانه استفاده می کنند که امکان ردیابی دقیق تر تلفات انرژی، تغییرات فاز، یا توزیع انرژی و جرم در فازهای مختلف را فراهم می کند. الگوریتمهای حلکننده از روشهای ساده گام زمانی ثابت [30،62،123] تا روشهای چند مرحلهای تطبیقی را شامل میشود.[39،142]
زمان محاسبات گزارش شده برای شبیه سازی بین _40 دقیقه [144] و کمتر از 1 دقیقه است، [49] اگرچه مقایسه مستقیم اغلب امکان پذیر نیست زیرا مشخصات رایانه های مورد استفاده برای به دست آوردن آن نتایج معمولاً ارائه نمی شود. در حالی که برخی از مدلهای پیشنهادی اخیرا و به تفصیل منتشر شدهاند و امکان ارزیابی جامع را فراهم میکنند، برخی دیگر، بهویژه مدلهایی که به صورت تجاری مورد استفاده قرار میگیرند، تنها به صورت سطحی و در مراحل اولیه توسعهشان توصیف شدهاند و مقایسه آنها با یکدیگر را دشوار میسازد.
8.1. ارتباط با مدل سازی سایر فرآیندهای متالورژی
بسیاری از چالشها و راهحلهای حاصل در مدلسازی EAF را میتوان در سایر فرآیندهای متالورژیکی مانند کوره اکسیژن پایه، کربنزدایی با اکسیژن/آرگون/خلاء (AOD/VOD)، گوگردزدایی فلز داغ و سایر فرآیندهای پالایش یافت. در برخی موارد، یک مدل را می توان برای چندین مورد از این فرآیندها وفق داد و ساختار مدل پایه مشترک را حفظ کرد. این را میتوان برای مثال در مدلهای EAF، VOD، و AOD که توسط Swinbourne و همکاران [33،149،150] یا Modigell و همکاران [103،104] برای مدلسازی EAF و BOF پیشنهاد شدهاند، یافت.
در موارد دیگر، مدل های کامل ممکن است قابل انتقال نباشند اما پدیده های خاص را می توان در چندین فرآیند و در شرایط مشابه یافت. به عنوان مثال، تزریق معرفهای جامد نیز در فرآیند گوگردزدایی مرتبط است و مدلهای دقیقی برای توصیف رابطهای حاصله و همچنین سینتیک واکنشها در امتداد این رابطها ایجاد شده است.[151]
در موارد دیگر، مدل های کامل ممکن است قابل انتقال نباشند اما پدیده های خاص را می توان در چندین فرآیند و در شرایط مشابه یافت. به عنوان مثال، تزریق معرفهای جامد نیز در فرآیند گوگردزدایی مرتبط است و مدلهای دقیقی برای توصیف رابطهای حاصله و همچنین سینتیک واکنشها در امتداد این رابطها ایجاد شده است.[151] به غیر از مورالس و همکاران، [21،22،65] که یک مدل پیچیده مشابه برای تزریق ذرات کربن به سرباره های EAF ایجاد کردند و آن را در مدل فرآیند EAF خود وارد کردند، مدل های فرآیند EAF شرح مفصلی از این واکنش ها را شامل نمی شوند. سینتیک تزريق اكسيژن هم از بالاي لنس ها و هم از لوله ها در زير سطح حمام بخش مهمي از فرآيندهاي BOF، VOD و AOD است. شرح خود رابط گاز و مایع و تشکیل قطرات سرباره وارد فاز فلزی و بالعکس در بسیاری از مدلهای فرآیند برای AOD، [152،153] VOD، [154] BOF، [134] و CAS-OB[ 155,156] جزئیات بیشتری از آنچه در EAF اجرا شده است. تأثیر تزریق گازها و جامدات بر اختلاط و سینتیک واکنش نیز به طور کامل از طریق مدلهای فیزیکی و مدلسازی CFD مورد مطالعه قرار گرفته است. در مدل های فرآیند EAF با این حال، برخی از مدلهای فرآیندهای پالایش، شامل توصیفهای دقیقتری از انتقال جرم و سینتیک واکنشهای ناشی از آن هستند. اطلاعات کمتری در مورد شرایطی مانند جریان، شکل دقیق و سطح سطح مشترک یا شرایط اختلاط در دسترس است، که سادهسازی و فرضیات بیشتری را ضروری میسازد. برعکس، فاز گاز معمولاً با جزئیات برای فرآیندهای دیگر مدلسازی نمیشود در حالی که تأثیر قابلتوجهی بر فرآیند EAF دارد. به خصوص پس از احتراق و مشعل ها در سایر فرآیندها استفاده نمی شود و بنابراین برای مدل سازی EAF و تا حدی BOF که در آن پس احتراق جزئی ممکن است در ظرف مبدل رخ دهد، خاص هستند.[134] به همین دلیل، توصیف واکنشهای فاز گاز و مناطق واکنش اضافی برای پس احتراق و مشعلها که در مدلهای فرآیند EAF اجرا میشوند، معمولاً در مقایسه با سایر فرآیندها جامعتر هستند. انتقال حرارت نیز نقش کمتری در مدلسازی فرآیندهای پالایش بازی میکند و مفروضاتی مانند فازهای همدما یا تلفات حرارتی ثابت بدون هیچ توضیح گستردهای از پدیدههای انتقال حرارت خاص رایج هستند. BOF در این زمینه یک استثنا است زیرا گرم کردن و ذوب ضایعات برای مدل سازی فرآیند ضروری است. سینتیک ذوب قراضه با جزئیات برای BOF مدلسازی شده است، [134] و در حالی که چالشهای اضافی مانند گرم کردن مستقیم قراضه از طریق مشعلها و قوسها برای EAF باقی میماند، مدلسازی ضایعات غوطهور میتواند به طور بالقوه بر اساس این راه حل های توسعه یافته برای BOF بهبود یابد.
8.2. کاربرد در صنعت معاصر و روندهای آینده
در حالی که بسیاری از مدلهای EAF به دلایل سرعت و استحکام مدل از توصیفات نسبتا سادهای برای تعادل فاز فلز- سرباره و گاز استفاده میکنند، مدلهای زیادی نیز وجود دارند که از روالهای پیچیده کمینهسازی انرژی گیبس و مدلهای سرباره استفاده میکنند که تقریباً مشابه آنچه در نرم افزار ترمودینامیکی محاسباتی استفاده میشود، استفاده میکنند.. در مورد دقت مدل، تفاوت بین مدلهایی با توصیف ساده و مدلهایی با توصیفهای پیچیدهتر (به عنوان مثال، MQM برای گونههای سرباره) قابل توجه نیست. در نتیجه، بعید به نظر میرسد که توصیفهای ترمودینامیکی دقت مدلهای فعلی را محدود کند یا با بهبود آنها بتوان به پیشرفتهای عمده در دقت مدل دست یافت.
یک منطقه اصلی برای بهبود بیشتر مدلهای EAF، توصیف سینتیک فرآیند است. به خصوص در مدل های حجم واکنش، پارامترهای جنبشی مربوط به تبادل جرم بین حجم ها اساساً ثابت های تجربی هستند. هر چه بیشتر از این پارامترها استفاده شود، مدل به مجموعه داده های مورد استفاده برای آموزش و اعتبار سنجی وابسته تر می شود.
در مورد واکنش های فلز- سرباره، عدم قطعیت های عمده مربوط به عمل سرباره کف می باشد. نایسن و همکاران [28,146,147,161] چگالی ظاهری سرباره کف کننده را با نرخ تولید CO مرتبط کردند. یک رویکرد رایج و ساده از نظر ریاضی، توصیف سرباره کفکننده با استفاده از مفهوم شاخص کفکننده است، که رایجترین تعریف برای آن، تعریفی است که در ref. [162] که به عنوان مثال توسط لوگار و همکاران استفاده شده است.[54] و مدل های مبتنی بر آن تعاریف دیگری نیز موجود است. مورالس و همکاران.[126] از شاخص فوم که توسط قاگ و همکارانش فرموله شده است استفاده می کنند.[163] با این حال، یک اعتبارسنجی جامع از رویکرد شاخص کف برای شرایط یک EAF صنعتی هنوز انجام نشده است.
همانطور که قبلا ذکر شد، شرح دقیق تری از سینتیک واکنش ها در طول تزریق واکنش دهنده ها، در سطح مشترک سرباره و مذاب، و ذوب ضایعات ممکن است بر اساس محلول های توسعه یافته و مورد استفاده برای فرآیندهای دیگر امکان پذیر باشد. با این حال، برای برخی از این موارد، اطلاعات بیشتر در مورد شرایط محلی و همچنین جریان و اختلاط در EAF لازم است، که مدلهای فرآیند را پیچیدهتر و از نظر محاسباتی با توجه به دانش سازندگان، هیچ یک از مدل های فرآیند EAF منتشر شده شرح مفصلی از شیب های محلی و تفاوت های داخل EAF ارائه نمی دهد. مدلهای پیشنهادی یا هندسههای سادهشده را در نظر میگیرند یا پدیدههای خاصی مانند انتقال حرارت یا واکنشهای شیمیایی را فقط برای کل کوره در نظر میگیرند و نه برای مقیاسهای محلی کوچکتر، جدا از تعریف مناطق اضافی برای توصیف واکنشهای خاص یا ذوب شمع قراضه که تا حدودی در برخی مدل ها دقیق تر است. این مفروضات به طور قابل توجهی سرعت محاسبه را افزایش می دهند که در بسیاری از موارد برای استفاده در برنامه های آنلاین مورد نیاز است. اشکال این رویکرد، دقت و کاربرد محدود این مدلها به دلیل حذف پدیدههای موضعی در مقیاسهای کوچکتر است. چنین پدیده های محلی بسیار مرتبط با بیشتر جنبه های مدل سازی EAF هستند. بهعنوان مثال، به دلیل تزریق گازها و کربن از طریق لنس ها و همچنین مشعلها، دماها و ترکیبات محلی ممکن است به طور قابلتوجهی با مناطق متوسط و همگن مورد استفاده در مدلسازی متفاوت باشد. در حالی که مدل های دقیق برای پدیده های خاص مانند شرایط انتقال حرارت محلی در اطراف شعله های مشعل، [164] ذوب ضایعات غوطه ور در فلز مایع، [56] یا تزریق واکنش دهنده ها همانطور که در بخش قبل بحث شد، ساده سازی های لازم در EAF وجود دارد. مدلسازی فرآیند از توصیف دقیق شرایط محلی دقیق و پدیدههای ناشی از آن مانند تشکیل نقاط داغ، ذوب یا انجماد موضعی فولاد یا واکنشهای شیمیایی خاص جلوگیری میکند.
یکی دیگر از کاستی های قابل توجه مدل های فعلی فرآیند EAF نحوه در نظر گرفتن انتقال حرارت پلاسما است. بسیاری از مدلها به فرض طول قوس نیاز دارند، که تعریف صحیح آن دشوار است زیرا دائماً بر اساس ولتاژ تغذیه تغییر میکند. مدلهای قوس را میتوان با استفاده از همبستگیهای تجربی بین ولتاژ و طول قوس برای استخراج طول قوس بر اساس ولتاژ بهبود بخشید. علاوه بر این، در تمام مدل های ارائه شده حاوی زیرمدل های پلاسما، انتقال حرارت از پلاسمای قوس بر اساس فرض سطح پلاسما به عنوان یک جسم سیاه است. از نقطه نظر فیزیکی، این فرض نادرست است زیرا انتقال حرارت در پلاسمای قوس الکتریکی از طریق حرکت الکترون ها و فوتون ها انجام می شود. با استفاده از مدلی که انتقال حرارت تشعشعی از پلاسمای قوس الکتریکی را بر اساس ترکیب پلاسما و شرایط تحریک محاسبه میکند، میتوان به توصیف دقیقتری از انتقال حرارت از پلاسما دست یافت. در مدلسازی جوشکاری قوس الکتریکی، از ضرایب انتشار تشعشعی برای مدلسازی اثر بخارات فلزی بر پلاسمای جوشکاری استفاده شده است.[165] در زمینه ذوب قوس الکتریکی، چنین مدلی توسط سواستاینکو و باکن [166] برای یک کوره تولید فروسیلیکون ایجاد شد. مزیت مدلهای انتشار تشعشعی این است که توصیف رابطه بین توان انتشار و طول موج را با دقت بیشتری ممکن میسازند، که میتواند با مدل جذبی رسانه فرستنده در EAF همراه شود. طول موج انتشار پلاسما در محاسبه انتقال حرارت مهم است زیرا رفتار جذب غبار و گاز در جو EAF وابسته به طول موج است. فرض جسم سیاه سطح پلاسما، دقت مدلهای جذب جو EAF را محدود میکند، به ویژه در نواحی نزدیک به قوس. برای دستیابی به مدلسازی دقیقتر انتقال حرارت، مدل انتشار قوس وابسته به طول موج میتواند با مدل وزنی مجموع گازهای خاکستری برای اتمسفر EAF همانطور که توسط Opitz و همکاران پیشنهاد شده است، استفاده شود.[44]
در حالی که اصولاً چندین مورد از این مسائل را میتوان از طریق مدلهای جامع CFD فرآیند EAF حل کرد، همانطور که قبلاً ذکر شد، این موارد هنوز از نظر محاسباتی بسیار گرانتر از آن هستند که بهعنوان جایگزینی برای مدلهای فرآیند استفاده شوند.[10] بنابراین، توسعه بیشتر به سمت مدلهای فرآیندی دقیقتر اما همچنان سریعتر و کارآمدتر، که تا حدی برخی از تواناییهای مدلهای CFD را تکرار میکنند، هنوز برای آینده قابل پیشبینی قابل انتظار است. برخلاف مدلهای CFD، مدلهای فرآیند موجود را میتوان در تحلیل سناریو برای پیشبینی تأثیرات تغییرات مختلف در فرآیند EAF بر پارامترهایی مانند زمان لازم برای ذوب کردن ضایعات یا تکامل دمای مذاب مورد استفاده قرار داد. پیچیدگی فزاینده مدلها، مانند معرفی مدلهای خارج از گاز برای بهینهسازی پس احتراق در EAF یا مدلسازی خواص و کفکردن سرباره، بر این اساس، امکان تحلیل و بهینهسازی سناریوهای دقیقتری را فراهم میکند.[124,133,143,148] توجه به این نکته مهم است که افزایش پیچیدگی مدلهای فرآیند باعث افزایش بیش از حد در زمان محاسبه نشده است.[89] این امکان میدهد که مدلهای فرآیند کنونی در محاسبات آنلاین نیز مورد استفاده قرار گیرند، [122،141،147،148،167–37،61،113،115] اگرچه کاربردهای گزارش شده از این مدلها هنوز کمیاب است. بیشتر برنامه های کاربردی آنلاین منتشر شده شامل پیش بینی دمای مذاب [122،141،148،167-61,113,115] یا کنترل مشعل ها و همچنین تزریق کربن و اکسیژن است. در برنامه پیشبینی دمای مذاب، مدل فرآیند به طور مداوم دمای مذاب را پیشبینی میکند و نتیجه مدل با اندازهگیریهای دما کالیبره میشود. اکثر برنامه های کاربردی آنلاین ارائه شده با مدل های تجاری به دست آمده اند، که ارزیابی عینی عملکرد آنها را دشوار می کند. انتشار و استفاده از مجموعه داده مرجع EAF گامی رو به جلو در مقایسه عملکرد مدل های پیشنهادی خواهد بود. علاوه بر این، آزمون واحد میتواند برای اعتبارسنجی مستقل مدلهای فرعی مانند محاسبه عوامل دید، جریانهای گرمای تشعشعی، یا ترکیبهای تعادلی و در نتیجه کمیسازی و احتمالاً حذف خطاهای معرفیشده توسط این مدلها در نتایج مدل فرآیند کلی مورد استفاده قرار گیرد.
این احتمال وجود دارد که برنامه های آنلاین مدل های فرآیند EAF در آینده افزایش یابد، به دلیل افزایش فشار برای بهینه سازی هزینه ها و انتشار گازهای گلخانه ای و همچنین افزایش پیچیدگی مسئله بهینه سازی به دلیل مواد اضافی و حامل های انرژی مورد استفاده در این فرآیند.[1] مزیت مدلهای فرآیند آنلاین این است که میتوان آنها را به راحتی به اندازهگیریهای آنلاین مرتبط کرد، زیرا هم اندازهگیریها و هم مدلهای فرآیند با مقادیر فیزیکی فرآیند سروکار دارند. این امکان تنظیم مجدد ثابت پارامترهای مدل تجربی و برون یابی دقیق نتایج بر اساس داده های اندازه گیری را فراهم می کند. توسعه مدلهای فرآیند EAF به مرحلهای نزدیکتر میشود که میتوان آنها را برای بهینهسازی فرآیندهای آفلاین و آنلاین نیز اعمال کرد. با توجه به تعداد بالای ارزیابی سناریوهای لازم در بهینه سازی، مدل برای این منظور باید بسیار کارآمد و سریع باشد. در حالی که برخی بهینهسازیها با مدلهای تا حدودی کاهشیافته و سادهشده انجام شده است، [۱۲۴،۱۳۳،۱۴۳،۱۴۸] هم بهینهسازی سریع یا حتی آنلاین استراتژیهای کنترل برای گرمای خاص و هم تنظیم خودکار پارامترهای تجربی چالشهای مهمی را در مدلسازی فرآیند EAF ارائه میکنند.
برای استفاده گسترده تر در صنعت، مدل های پیچیده تری برای غلبه بر این چالش ها و سایر چالش ها نیاز دارند. سرعت کافی و الگوریتمهای بهینهسازی کارآمد برای اجازه دادن به تنظیم خودکار پارامترهای مدل، اجتناب از تنظیم مجدد پیچیده مدل برای در نظر گرفتن تغییرات جزئی در محیط کوره یا شرایط فرآیند و امکان بهینهسازی آنلاین استراتژیهای عملیاتی مورد نیاز است. رابط های کاربر و داده مناسب برای ادغام مدل ها در سیستم های کنترل کارخانه فولاد مورد نیاز است. علاوه بر این، بررسی قابل قبول بودن نتایج و ورودیهای مدل برای شناسایی ورودیهای نادرست و شکستهای احتمالی مدل برای پیشبینی معنادار در موارد خاص و غیرعادی ضروری است. در حالی که برخی یا همه این شرایط ممکن است توسط چندین مدل تجاری موجود برآورده شوند، چندین مدل فرآیند دقیق و جامع در محیطهای عمدتاً دانشگاهی گزارش شدهاند که نیاز به توسعه بیشتر برای آوردن این پیشرفتها به استفاده صنعتی دارند. علاوه بر این، کالیبراسیون و اعتبارسنجی مدلهای پیچیده EAF از اندازهگیریهای اضافی و دقیقتر بهره میبرد. برخی از اندازهگیریهای مطلوب مانند آنالیز پیوسته ترکیب و دما خارج از گاز، [168-171] سطوح صدا و ارتعاشات به عنوان شاخصی از پیشرفت کیفیت سربارههای مذاب و کف، [172،173] تعیین مداوم مذاب. دما، [8،141] یا ترکیب پلاسمای قوس [9،174،175] فقط برای برخی از کوره ها یا هنوز در حال توسعه هستند. با استفاده گسترده تر از این گونه سیستم ها و کنترل کیفیت بهتری که برای اکتساب و مدیریت داده های فرآیند اعمال می شود، دقت و کاربرد مدل های فرآیند می تواند به طور قابل توجهی بهبود یابد.
- نتیجه گیری
مدلهای موجود عموماً قادر به توصیف تمام جنبههای اصلی فرآیند هستند. مدلهای فرآیند بنیادی اطلاعات بهدستآمده از انواع مدلها مانند مدلهای CFD و مدلهای آماری را با ارائه ابزاری برای درک و شبیهسازی تمام جنبههای اصلی فرآیند EAF با مزایا و معایب خاص در مقایسه با این کلاسهای دیگر مدلها، تکمیل میکنند. مدلهای فرآیند بنیادی مدرن میتوانند توزیع انرژی الکتریکی و شیمیایی را در کوره و همچنین تغییرات دینامیکی در ترکیبات فلز، سرباره و گازهای خارج از گاز را پیشبینی کنند و به اندازه کافی سریع و پایدار هستند تا برای کنترل پیشبینی مدل مورد استفاده قرار گیرند.
توصیفهای ترمودینامیکی نسبتاً پیچیده هستند و میتوانند تعادل فاز فلز-سرباره و گاز را با دقت نسبتاً خوبی بازتولید کنند. با این حال، توصیف سینتیک را میتوان بر اساس رویکردهای توسعهیافته برای سایر فرآیندهای متالورژی و با استفاده از اطلاعاتی که میتوان از مدلهای مبتنی بر پدیدههای دقیقتر یا آزمایشهای مقیاس آزمایشگاهی استخراج کرد، بهبود بخشید. همین امر برای توصیف دقیقتر پدیدههای محلی مانند ذوب ضایعات، تشکیل نقاط داغ یا توصیف قوس الکتریکی که با استفاده از مدلهای انتقال جریان، گرما و جرم سادهشده قابل پیشبینی نیست، صادق است. علاوه بر این، تکنیکهای اندازهگیری جدید را میتوان به عنوان منابع اطلاعاتی برای ورودی و اعتبارسنجی به محض در دسترس قرار گرفتن، گنجاند.
سپاسگزاری ها
کار Ville-Valtteri Visuri و Matti Aula در چارچوب پروژه AMET که توسط Business Finland تامین می شود انجام شد. بودجه دسترسی آزاد توسط Projekt DEAL فعال و سازماندهی شده است.
تعارض منافع
سازندگان اظهار هیچ تضاد منافعی را ندارند.
کلید واژه ها
کوره قوس الکتریکی، انتقال حرارت، سینتیک، مدل های فرآیند، بررسی، ترمودینامیک
دریافت: 21 جولای 2020
بازبینی شده: 22 سپتامبر 2020
انتشار آنلاین: 30 سپتامبر 2020
توماس هی دستیار پژوهشی در گروه کوره های صنعتی و مهندسی حرارت در دانشگاه RWTH آخن است. پروژه پایان نامه دکترای در حال انجام او بر مدل سازی ریاضی فرآیند EAF متمرکز است. او مدرک کارشناسی ارشد خود را در مهندسی انرژی و مدرک لیسانس خود را در مهندسی مکانیک از دانشگاه RWTH آخن دریافت کرد.
Ville-Valtteri Visuri یک محقق ارشد در واحد تحقیقات متالورژی فرآیند در دانشگاه اولو است. علایق تحقیقاتی او بر متالورژی اولیه و ثانویه فولادسازی متمرکز است. وی دارای مدرک دکتری (استاد کمکی) در رشته متالورژی فرآیند و دارای مدرک دکتری در مهندسی فرآیند و همچنین دارای مدرک کارشناسی ارشد و لیسانس در مهندسی صنایع و مدیریت است. همه از دانشگاه اولو.
Matti Aula رئیس تحقیقات Luxmet Oy است. او همچنین به عنوان محقق فوق دکترا در واحد تحقیقات متالورژی فرآیند در دانشگاه اولو کار می کند. وی دارای چندین سال تجربه در زمینه توسعه و کاربرد فناوری اندازه گیری مربوط به فرآیندهای فولادسازی، به ویژه کوره های قوس الکتریکی و کوره های ملاقه ای است. او مدرک دکترا، کارشناسی ارشد و لیسانس خود را در رشته مهندسی فرآیند از دانشگاه اولو دریافت کرد.
منابع:
1] J. Madias, in Treatise in Process Metallurgy – Volume 3: Industrial Processes, Elsevier, Oxford, UK 2014, pp. 271–300.
[2] World Steel Association, Steel Statistical Yearbook 2019, World Steel Association, Brussels, Belgium 2019.
[3] T. Reichel, Ph.D. Thesis, RWTH Aachen University, 2018.
[4] H. B. Lüngen, M. Peters, P. Schmöle, presented at AISTech 2012, Atlanta, GA, May 2012.
[5] Y. N. Toulouevski, I. Y. Zinurov, Fuel Arc Furnace (FAF) for Effective Scrap Melting: From EAF to FAF, Springer, Singapore, 2017.
[6] L. S. Carlsson, P. B. Samuelsson, P. G. Jönsson, Metals 2019, 9, 959.
[7] Y. N. Toulouevski, I. Y. Zinurov, Innovation in Electric Arc Furnaces – Scientific Basis for Selection, Springer, Heidelberg 2010.
[8] T. Kordel, B. Kleimt, R. Pierre, G. Weides, G. Thomassen, S. Barella, C. Mapelli, L. Bianco, A. Viotto, Determining Process Conditions for Online Monitoring of Temperature and Carbon Content in the Electric Arc Furnace to Optimize End Point Control (MELTCON), European Commission, Brussels 2017.
[9] T. Willms, T. Echterhof, H. Pfeifer, M. Aula, T. Fabritius, N. Andersson, A. Tilliander, P. Jönsson, M. Jokinen, E. Puukko, S. Praschko, J.-S. Klung, On-line Slag Composition Analysis for Electric Arc Furnaces – State of the Art, European Commission, Brussles 2016.
[10] H.-J. Odenthal, A. Kemminger, F. Krause, L. Sankowski, N. Uebber, N. Vogl, Steel Res. Int. 2018, 89, 170098.
[11] K. Krüger, H. Pfeifer, in Praxishandbuch Thermoprozesstechnik – Band II: Anlagen, Komponenten, Sicherheit, 2nd ed., Vulkan Verlag, Essen 2011, pp. 43–80.
[12] Y. N. Toulouevski, I. Y. Zinurov, Electric Arc Furnace with Flat Bath – Achievements and Prospects, Springer, Cham, Switzerland 2015.
[13] T. Meier, Ph.D. Thesis, RWTH Aachen University, 2016.
[14] J. Wendelstorf, presented at SteelSim, Graz/Seggau, Austria, September 2007.
[15] I. Cameron, K. Hangos, Process Modelling and Model Analysis, Vol. 4, Elsevier, London 2001.
[16] J. Hasener, Ph.D. Thesis, Universität Hamburg, 2004.
[17] C. Chen, Y. Liu, M. Kumar, J. Quin, presented at 51st CRIP Conf. on Manufacturing Systems, Stockholm, Sweden, May 2018.
[18] C.-I. Chen, Y.-C. Chen, IEEE Trans. Power Delivery 2015, 30, 1577.
[19] G. W. Chang, C.-I. Chen, Y.-J. Liu, IEEE Trans. Power Syst. 2010, 25, 138.
[20] V. Logar, A. Fathi, I. Škrjanc, Steel Res. Int. 2016, 87, 330.
[21] H. H. Rodriguez, A. N. Conejo, R. D. Morales, Steel Res. Int. 2001, 71, 298.
[22] R. D. Morales, H. Rodriguez-Hernandez, P. Garnica-Gonzlez, J. A. Romero-Serrano, ISIJ Int. 1997, 37, 1072.
[23] M. Ozawa, S. Kitagawa, S. Nakayama, Y. Takesono, Trans. ISIJ 1986, 26, 621.
[24] V. Velikorodov, Ph.D. Thesis, RWTH Aachen University, 2009.
[25] A. H. Kolagar, Ph.D. Thesis, RWTH Aachen University, 2017.
[26] V. Logar, presented at 9th Eurosim & 57th SIMS, Oulu, Finland, September 2016.
[27] V. Logar, Simul. Notes Eur. 2016, 26, 91.
[28] P. Nyssen, R. Colin, S. Knoops, J. Junque, presented at 7th European Electric Steelmaking Conf. (EEC), Venice, Italy, May 2002.
[29] F. Opitz, Dynamische Modellierung des Lichtbogenofenverfahrens mit objektorientierten Beschreibungsansätzen, Shaker, Düren, Germany 2019.
[30] S. Köhle, Führungsmodell zur Optimierung des Elektrostahlprozesses – Steuerung des Lichtbogenofens, Kommission der Europäischen Gemeinschaften – Generaldirektion Informationsmarkt und Innovation, Luxemburg 1982.
[31] A. C. Deneys, K. D. Peaslee, presented at 55th Electric Furnace Conf., Chicago, IL, November 1997.
[32] F. M. Boland, Ph.D. Thesis, Sheffield City Polytechnic, 1977.
[33] T. S. Kho, D. R. Swinbourne, B. Blanpain, S. Arnout, D. Langberg, Trans. Inst. Min. Metall. C 2010, 119, 1.
[34] R. D. M. MacRosty, C. L. E. Swartz, Ind. Eng. Chem. Res. 2005, 44, 8067.
[35] V. Logar, I. Škrjanc, ISIJ Int. 2012, 52, 1225.
[36] T. Meier, K. Gandt, T. Hay, T. Echterhof, Steel Res. Int. 2018, 89, 1700487.
[37] A. Linninger, M. Hofer, A. Patuzzi, Iron Steel Eng. 1995, 72, 43.
[38] L. P. Rathaba, M.Eng. Thesis, University of Pretoria, 2004.
[39] A. Fathi, Y. Saboohi, I. Škrjanc, V. Logar, Steel Res. Int. 2017, 83,1600083.
[40] F. Opitz, P. Treffinger, Metall. Mater. Trans. B 2016, 47B, 1489.
[41] F. Opitz, P. Treffinger, J. Wöllenstein, R. Schweikle, presented at 11th European Electric Steelmaking Conf., Venice, Italy, May 2016.
[42] A. Fathi, Y. Saboohi, I. Škrjanc, V. Logar, ISIJ Int. 2015, 55, 1353.
[43] Y. Saboohi, A. Fathi, I. Škrjanc, V. Logar, Steel Res. Int. 2018, 89, 1700446.
[44] F. Opitz, P. Treffinger, J. Wöllenstein, Metall. Mater. Trans. B 2017, 48B, 3301.
[45] J. D. Hernandez, L. Onofri, S. Engell, presented at 8th Int. Conf. on Modeling and Simulation of Metallurgical Processes in Steelmaking (STEELSIM 2019), Toronto, Ontario, Canada, August 2019.
[46] T. Hay, J. D. Hernandez, S. Roberts, Steel Res. Int. 2020, https://doi. org/10.1002/srin.202000341.
[47] A. Ringel, M.Sc. Thesis, RWTH Aachen, 2020.
[48] V. Logar, D. Dovžan, I. Škrjanc, ISIJ Int. 2012, 52, 402.
[49] T. Hay, A. Reimann, T. Echterhof, Metall. Mater. Trans. B 2019, 50, 2377.
[50] D. J. Oosthuizen, J. H. Viljoen, I. K. Craig, P. C. Pistorius, ISIJ Int. 2001, 41, 399.
[51] D. J. Oosthuizen, M.Eng. Thesis, University of Pretoria, 2001.
[52] J. G. Bekker, M.Sc. Thesis, University of Pretoria, 1998.
[53] R. D. M. MacRosty, C. L. E. Swartz, presented at Iron and Steel
Technology Conf. AISTech, Charlotte, NC, USA, May 2005.
[54] V. Logar, D. Dovžan, I. Škrjanc, ISIJ Int. 2012, 52, 413.
[55] G. Wei, R. Zhu, T. Tang, K. Dong, Ironmaking Steelmaking 2019, 46, 609.
[56] Y. L. Zhang, M. Gao, presented at STEELSIM, Toronto, Canada, August 2019.
[57] Y. A. Stankevich, V. I. Timoshpol’skii, N. V. Pavlyukevich, M. G. German, P. S. Grinchuk, J. Eng. Phys. Thermophys. 2009, 82, 221.
[58] A. Kruskopf, Metall. Mater. Trans. B 2015, 46, 1195.
[59] J. Li, G. Brooks, N. Provatas, Metall. Mater. Trans. B 2005, 36, 293.
[60] J. Li, N. Provatas, Metall. Mater. Trans. B 2008, 29, 268.
[61] B. Kleimt, S. Köhle, R. Kühn, S. Zisser, presented at 8th European Electric Steelmaking Congress, ECC, Brimingham, GB 2005.
[62] S. Arnout, F. Verhaeghe, B. Blanpain, P. Wollants, R. Hendrickx, G. Heylen, Steel Res. Int. 2006, 77, 317.
[63] D. H. Shah, K. D. Peaslee, presented at 56th Electric Furnace Conf., New Orleans, LA, USA, November 1998.
[64] S. A. Matson, W. F. Ramirez, presented at 55th Electric Furnace Conf., Chicago, IL, USA, November 1997.
[65] R. D. Morales, H. Rodríguez-Hernández, A. N. Conejo, ISIJ Int. 2001, 41, 426.
[66] B. Bowman, K. Krüger, Arc Furnace Physics, Stahleisen, Düsseldorf, Germany 2009.
[67] J. J. Valencia, P. N. Quested, in: ASM Handbook, ASM International, Materials Park, OH, USA, 2010.
[68] C. H. P. Lupis, J. F. Elliot, Acta Metall. 1966, 14, 1019.
[69] A. D. Pelton, C. W. Bale, Metall. Trans. A 1986, 17, 1211.
[70] I.-H. Jung, Calphad 2010, 34, 332.
[71] J. Lehmann, I.-H. Jung, in Treatise on Process Metallurgy, Volume 2: Process, Elsevier, Oxford, UK 2014.
[72] Z. Ma, J. Ohser, D. Janke, Acta. Metall. Sin. 1997, 10, 375.
[73] G. K. Sigworth, J. F. Elliot, Met. Sci. 1974, 8, 298.
[74] E. Karto, M. Inoue, T. Fujisawa, T. Mori, H. Ichise, A. Moro-oka, Z.-I. Morita, K. Narita, K.-I. Suzuki, Y. Kawai, K. Mori, Steelmaking Data Sourcebook, Gordon and Breach, Montreux, Switzerland 1988.
[75] S. Ban-Ya, ISIJ Int. 1993, 33, 2-11.
[76] M. L. Kapoor, M. G. Frohberg, presented at Int. Symp. On Metallurgical Chemistry – Applications in Ferrous Metallurgy, Sheffield, Großbritannien, 1973.
[77] A. D. Pelton, M. Blander, presented at AIME Symp. on Metallurgical Slags and Fluxes, Lake Tahoe, NV, USA, 1984.
[78] Y. Xiao, L. Holappa, Metall. Mater. Trans. B 2002, 33b, 595.
[79] W. Pei, O. Wijk, Scand. J. Metall. 1994, 23, 228.
[80] E. A. Guggenheim, Proc. R. Soc. Lond. A 1935, 148, 304.
[81] A. D. Pelton, S. A. Degterov, G. Eriksson, C. Robelin, Y. Dessureault, Metall. Mater. Trans. B 2000, 31, 651.
[82] A. D. Pelton, P. Chartrand, Metall. Mater. Trans. A 2001, 32, 1355.
[83] P. Chartrand, A. D. Pelton, Metall. Mater. Trans. A 2001, 32, 1397.
[84] A. D. Pelton, P. Chartrand, G. Eriksson, Metall. Mater. Trans. A 2001, 32, 1409.
[85] G. W. Toop, Trans. Metall. Soc. AIME 1965, 233, 850.
[86] P. Frittella, A. Lucarelli, L. Angelini, E. Filippini, B. Poizot, M. Legrand, presented at AISTech – The Iron and Steel Technology Conf. and Exhibition, Indianapolis, IN, USA, May 2011.
[87] T. Meier, K. Gandt, T. Echterhof, H. Pfeifer, Metall. Mater. Trans. B 2017, 48, 3329.
[88] T. Hay, A. Reimann, T. Echterhof, H. Pfeifer, presented at 8th Int. Conf. on Modeling and Simulation of Metallurgical Processes in Steelmaking (STEELSIM 2019), Toronto, Ontario, Canada, August 2019.
[89] T. Hay, T. Echterhof, V.-V. Visuri, Processes 2019, 7, 852.
[90] A. Cameron, N. Saxena, K. Broome, presented at 56th Electric Furnace Conf., New Orleans, LA, 1998.
[91] S. Matson, W. F. Ramirez, presented at 57th Electric Furnace Conf., Pittburgh, PA, November 1999.
[92] S. A. Matson, W. F. Ramirez, P. Safe, presented at 56th Electric Furnace Conf., New Orleans, LA, November 1998.
[93] R. D. M. MacRosty, C. L. E. Swartz, AIChE J. 2007, 53, 640.
[94] R. D. M. MacRosty, C. L. E. Swartz, IFAC Proc. Vol. 2007, 40, 285.
[95] W. Nernst, Z. physik. Chem. 1904, 47, 52.
[96] W. K. Lewis, W. G. Whitman, Ind. Eng. Chem. 1924, 16, 1215-1220.
[97] F. Oeters, Metallurgie der Stahlherstellung, Verlag Stahleisen GmbH, Düsseldorf, Germany 1989.
[98] M. Järvinen, V.-V. Visuri, E.-P. Heikkinen, A. Kärnä, P. Sulasalmi, C. D. Blasio, T. Fabritius, ISIJ Int. 2016, 56, 1543.
[99] N. J. Themelis, B. Zhao, in: Metallurgical Processes for the Early Twenty-First Century, TWS, Warrendal, PA 1994.
[100] N. Dogan, G. A. Brooks, M. A. Rhamdhani, ISIJ Int. 2011, 51, 1093.
[101] R. Sarkar, P. Gupta, S. Basu, N. B. Ballal, Metall. Mater. Trans. B 2015, 46, 961.
[102] B. K. Rout, G. Brooks, M. A. Rhamdhani, Z. Li, F. N. H. Schrama, J. Sun, Metall. Mater. Trans. B 2018, 49, 537.
[103] M. Modigell, A. Traebert, P. Monheim, AISE Steel Tech. 2001, 78, 45.
[104] A. Traebert, M. Modigell, P. Monheim, K. Hack, Scand. J. Metall. 1999, 28, 285.
[105] J. G. Bekker, I. K. Craig, P. C. Pistorius, IFAC Proc. Vol. 1998, 31, 55.
[106] J. G. Bekker, I. K. Craig, P. C. Pistorius, ISIJ Int. 1999, 39, 23–32.
[107] T. Meier, T. Hay, T. Echterhof, H. Pfeifer, T. Rekersdrees, L. Schlinge, S. Elsabagh, H. Schliephake, Steel Res. Int. 2017, 88, 1600458.
[108] M. P. King, M.A.Sc. Thesis, McMaster University, 2009.
[109] T. X. Zhu, M.A.Sc. Thesis, McMaster University, 2011.
[110] Y. Lytvynyuk, J. Schenk, M. Hiebler, A. Sormann, Steel Res. Int. 2014, 85, 537.
[111] World Steel Association, Electric Arc Furnace Simulation, https://steeluniversity.org/product/electric-arc-furnace-simulation/ (accessed July 2019).
[112] World Steel Association, Electric Arc Furnace Simulation User Guide, https://content.steeluniversity.org/simulators/eaf/ userguide/en/ (accessed August 2019). [113] M. Hofer, P. L. Steger, J. Lehner, W. Gebert, Iron Steel Eng. 1997, 40, 35.
[114] C. Hayman, S. Agarwal, A. Heyd, I. Gordon, presented at 55th Electric Furnace Conf., Chicago, IL, November 1997.
[115] P. Clerici, F. Dell’Acqua, J. Maiolo, V. Scipolo, MPT Int. 2008, 31, 40.
[116] C. Raggio, Steel Times Int. 2008, 32, 45.
[117] P. Clerici, F. Dell’Acqua, J. Maiolo, S. Vittorio, Steel Times Int. 2008, 32, 19.
[118] J. Maiolo, V. Scipolo, P. Clerici, Millenium Steel 2011, 60.
[119] S. Natschläger, K. Stohl, IFAC Proc. Vol. 2007, 40, 207.
[120] S. Natschläger, K. Stohl, presented at CMS Annual Meeting, Chengdu, China, November 2007.
[121] S. Natschläger, S. Dimitrov, K. Stohl, Arch. Metall. Mater. 2008, 53, 373.
[122] S. Natschläger, S. Dimitrov, K. Stohl, Stahl Eisen 2009, 129, 73.
[123] S. A. Billings, F. M. Boland, H. Nicholson, Automatica 1979, 15, 137.
[124] Y. E. M. Ghobara, M.A.Sc. Thesis, McMaster University, 2013.
[125] L. C. Coetzee, M.Eng. Thesis, University of Pretoria, 2006.
[126] R. D. Morales, A. N. Conejo, H. H. Rodriguez, Metall. Mater. Trans. B 2002, 33, 187.
[127] J. Wendelstorf, K.-H. Spitzer, presented at AISTech – The Iron and Steel Technology Conf. and Exhibition, Cleveland, OH, USA, May 2006.
[128] J. Wendelstorf, Arch. Metall. Mater. 2008, 53, 385.
[129] G. Brooks, R. Reeves, presented at 55th Electric Furnace Conf., Chicago, IL, USA, November 1997.
[130] G. Brooks, J. McClellan, D. Muschamp, A. Fontana, M. Bogusz, SEAISI Q. 2012, 41, 17.
[131] V. Logar, D. Dovžan, I. Škrjanc, ISIJ Int. 2011, 51, 382.
[132] V. Logar, I. Škrjanc, ISIJ Int. 2012, 52, 1924.
[133] Y. Saboohi, A. Fathi, I. Škrjanc, V. Logar, IEEE Trans. Ind. Electron. 2019, 66, 8030.
[134] L. D. Vos, I. Bellemans, C. Vercruyssen, K. Verbekn, Metall. Mater. Trans. B 2019, 50, 2647.
[135] A. Cameron, Steel Times 1999, 227, 7.
[136] J. G. Bekker, I. K. Craig, P. C. Pistorius, Control. Eng. Pract. 2000, 8, 445.
[137] U. Martini, B. Kleimt, S. Zisser, H. Pfeifer, M. Kirschen, V. Velikorodov, U. De Miranda, R. Kühn, J. Deng, J. Siig, H. J. Wahlers, Development of Operating Conditions to Improve
Chemical Energy Yield and Performance of Dedusting in Airtight EAF, European Commission, Brussels 2007.
[138] B. Kleimt, B. Dettmer, V. Haverkamp, T. Deinet, P. Tassot, in Recycling und Rohstoffe, Thomé-Kozmiensky Verlag GmbH, Neuruppin, Germany 2012, pp. 367.
[139] B. Kleimt, B. Dettmer, V. Haverkamp, T. Deinet, P. Tassot, Chem. Ing. Tech. 2012, 84, 1714.
[140] B. Kleimt, R. Pierre, B. Dettmer, J. Deng, L. Schlinge, H. Schliephake, presented at 10th European Electric Steelmaking Conf., Graz, Austria, September 2012.
[141] H. Köchner, T. Kordel, B. Kleimt, R. Pierre, G. Thomassen, G. Weides, S. Barella, C. Mapelli, L. Bianco, A. Viotto, presented at 11th European Electric Steelmaking Conf., Venice, Italy, May 2016.
[142] T. Meier, V. Logar, T. Echterhof, I. Škrjanc, H. Pfeifer, Steel Res. Int. 2016, 87, 581.
[143] T. Meier, M.Sc. Thesis, RWTH Aachen University, 2017.
[144] F. Opitz, P. Treffinger, Schlussbericht BMBF Forschungsvorhaben im Rahmen des Programms “Forschung an Fachhochschulen”, Bundesministerium für Bildung und Forschung, Bonn 2017.
[145] J. C. Baumert, J.-L. R. Vigil, P. Nyssen, J. Schaefers, G. Schutz, S. Gillé, Improved Control of Electric Arc Furnace Opterations by Process Modelling, European Commission, Brussels, Belgium, 2005.
[146] P. Nyssen, G. Monfort, J. L. Junque, M. Brimmeyer, P. Hubsch, J. C. Baumert, presented at STEELSIM, Int. Conf. of Simulation and Modelling of Metallurgical Processes in Steelmaking, Vol. 2, Graz/Seggau, Austria, 2007.
[147] P. Nyssen, C. Ojeda, J. C. Baumert, M. Picco, J. C. Thibaut, S. Sun, S. Waterfall, M. Ranger, M. Lowry, presented at STEELSIM, Int. Conf.
of Simulation and Modelling of Metallurgical Processes in Steelmaking, 4, METEC InSteelCon, Düsseldorf, Germany, June 2011.
[148] C. Ojeda, O. Ansseau, P. Nyssen, J. C. Baumert, J. C. Thibaut, M. Lowry, presented at METEC & 2nd ESTAD, Düsseldorf, June 2015.
[149] D. R. Swinbourne, T. S. Kho, B. Blanpain, S. Arnout, D. Langberg, Trans. Inst. Min. Metall. C 2012, 121, 23.
[150] D. R. Swinbourne, T. S. Kho, D. Langberg, B. Blanpain, S. Arnout, Trans. Inst. Min. Metall. C 2010, 119, 107.
[151] V.-V. Visuri, T. Vuolio, T. Haas, T. Fabritius, Steel Res. Int. 2020, 91, 1900454.
[152] V.-V. Visuri, M. Järvinen, A. Kärnä, P. Sulasalmi, E.-P. Heikkinen, P. Kupari, T. Fabritius, Metall. Mater. Trans. B 2017, 48, 1850.
[153] V.-V. Visuri, M. Järvinen, P. Sulasalmi, E.-P. Heikkinen, J. Savolainen, ISIJ Int. 2013, 53, 603.
[154] R. Ding, B. Blanpain, P. T. Jones, P. Wollants, Metall. Mater. Trans. B 2000, 31B, 197.
[155] P. Sulasalmi, V.-V. Visuri, A. Kärnä, M. Järvinen, S. Ollila, T. Fabritius, Metall. Mater. Trans. B 2016, 47, 3544.
[156] M. Järvinen, A. Kärnä, V.-V. Visuri, P. Sulasalmi, E.-P. Heikkinen, K. Pääskylä, C. D. Blasio, S. Ollila, T. Fabritius, ISIJ Int. 2014, 54, 2263.
[157] L. Cao, Y. Wang, Q. Liu, X. Feng, ISIJ Int. 2018, 58, 573.
[158] M. Ersson, A. Tilliander, Steel Res. Int. 2018, 89, 1.
[159] A. N. Conejo, F. R. Lara, M. Macias-Hernandez, R. D. Morales, Steel Res. Int. 2007, 78, 141.
[160] K. J. Graham, Ph.D. Thesis, McMaster University, 2008.
[161] P. Nyssen, R. Colin, J.-L. Junqué, S. Knoops, Rev. Met. Paris 2004, 101, 317.
[162] H. Baer, D. F. Baret, C. D. Blumenschein, J. A. Burgo, W. E. Buss, A. Calderon, R. G. DiNitto, D. J. Doran, R. F. Drnevich, A. J. Dzermejko, J. Feinman, R. J. Fruehan, N. J. Goodman, F. W. Hyle, M.-A. Van Ende, F. Keissling, H.-M. Lee, A. Lehrman, C. J. Messina, J. J. Poveromo, J. Richardson, J. A. Ricketts, U. Schwarz, R. J. Selines, S. E. Stewart, J. L. Sundholm, E. T. Turkdogan, H. S. Valia, J. P. Wallace, R. Worberg, R. W. Ziegler, The Making, Shaping and Treatment of Steel, 11th ed., AISE Steel Foundation, Pittsburgh, PA 1999.
[163] S. S. Ghag, P. C. Hayes, H.-G. Lee, ISIJ Int. 1998, 38, 1201.
[164] J. D. Hernandez, L. Onofri, S. Engell, presented at Mining, Minerals and Metal Processing MMM 2019, Stellenbosch, South Africa, 2019.
[165] A. B. Murphy, J. Phys. D: Appl. Phys. 2010, 43, 434001.
[166] V. G. Sevastyanenko, J. A. Bakken, presented at 5th European Conf. on Thermal Plasma Processes (TPP-5), St. Petersburg, Russia, 1998.
[167] M. Hofer, P. L. Steger, J. Lehner, W. Gebert, Steel Times 1997, 225, 108.
[168] M. Kirschen, H. Pfeifer, presented at EEC, Birmingham, 2005.
[169] R. Kühn, H. G. Geck, K. Schwerdtfeger, ISIJ Int. 2005, 45, 1587.
[170] D. Tolazzi, M. Picciotto, M. Piazza, O. Milocco, presented at 46º Seminário de Aciaria – Internacional (AMB Week 2015), Rio De Janeiro, Brasil, 2015.
[171] D. Tolazzi, S. Marcuzzi, S. Beorchia, presented at AISTech – The Iron and Steel Technology Conf. and Exhibition, Indianapolis, IN, USA, 2011.
[172] T. Matschullat, D. Rieger, K. Krüger, A. Döbbeler, Arch. Metall. Mater. 2008, 53, 399.
[173] C. Schmidt, N. Å. I. Andersson, P. Ljungsqvist, A. Tilliander, P. G. Jönsson, presented at 6th Int. Congress on the Science and Technology of Steelmaking, Beijing, China, 2015.
[174] H. Pauna, T. Willms, M. Aula, T. Echterhof, T. Fabritius, presented at 7th Int. Congress on Science and Technology of Steelmaking – ICS, Venice, Italy, 2018.
[175] M. Aula, T. Demus, T. Echterhof, M. Huttula, H. Pfeifer, T. Fabritius, ISIJ Int. 2016, 57, 47.
[176] H. Matsuura, C. P. Manning, R. A. F. O. Fortes, R. J. Fruehan, ISIJ Int. 2008, 48, 1197.
[177] R. A. F. d. O. Fortes, Ph.D. Thesis, PUC do Rio de Janeiro, 2010.
[178] P. Frittella, A. Lucarelli, B. Poizot, M. Legrand, Steel Times Int. 2009, 102, 11.