کاهش ضریب مصرف الکترود گرافیتی
این مقاله در مجله پردازش شماره ۱۲۶ و ۱۲۷، اردیبهشت و خرداد ۱۳۹۸، از صفحه ۳۰ الی ۳۲ به چاپ رسیده است.
کاهش ضریب مصرف الکترود گرافیتی
حسام ادیب
رئیس هیئت مدیره گروه دانش بنیان پاترون
از حدود ۲ سال پیش الکترود گرافیتی افزایش قیمت شدیدی داشته و منجر به افزایش بهای تمام شده فولاد خام گردیده است. این موضوع فولادسازان را بر آن داشته تا به هر روش ممکن برای کاهش ضریب مصرف الکترود گرافیتی اقدام کنند. یکی از روشهایی که میتواند به تحلیل و کاهش مصرف الکترود گرافیتی کمک کند، جمعآوری دادههای کمّی مرتبط با مصرف آن است، روشی که در حل مسئلههای مشابه نیز به کار میرود.
اما پیچیدگی و تعدد عوامل موثر بر مصرف الکترود گرافیتی در کوره های قوس الکتریکی بسیار زیاد است به طوری که تحلیل دادهها را بسیار سخت مینماید. از همین روست که بسیاری از فولادسازان حتی لزومی به توزین الکترودها قبل و بعد از مصرف نمیبینند و به روشهای دیگری برای کنترل مصرف و کاهش آن میپردازند.
در طی بیش از یک سال گذشته، به خاطر پروژههای کاهش مصرف الکترود گرافیتی با پوشش الکوپات در کارخانجات مختلف کشور، گروه دانش بنیان پاترون امکان جمع آوری دادههای مرتبط با مصرف الکترود گرافیتی را به دست آورد و بر همین اساس با یکی از روشهای داده کاوی، موفق به مدلسازی ضریب مصرف الکترود گرافیتی به کمک شبکه عصبی گردید که نتایج این تحقیق در مقالهای در سمپوزیوم فولاد ۹۷ ارائه گردید.
به جز طرح و تکنولوژی کوره قوس الکتریکی و نیز برند و کیفیت الکترود گرافیتی، که خارج از کنترل مهندسان بهرهبردار است، دادههای کمی که در کورههای قوس الکتریک، در هر ذوب، قابل جمع آوری هستند عبارتند از:
جریان هر فاز (بر حسب کیلوآمپر)، عمر هر ستون الکترود (تعداد ذوب)، وزن مذاب تخلیه شده، مدت زمان ذوب، زمان خاموشی کوره، انرژی مصرف شده (کیلووات ساعت)، میزان آهک و دولومیت مصرف شده، مقدار آهن اسفنجی و قراضه مصرف شده، اکسیژن مصرفی، آهن کل موجود در آهن اسفنجی، متالیزاسیون، کربن و گوگرد آهن اسفنجی.
پارامترهای دیگری نیز هستند که بر میزان مصرف الکترود گرافیتی مؤثرند و در صورت وجود ابزار اندازهگیری، دادههای آنها نیز قابل جمع آوری و تحلیل است. داده هایی مثل مکش سیستم تصفیه دود و خنک کنندگی رینگ آب الکترود، دمای اولیه شارژ، تنظیم KT ها، تنظیمات طول قوس، عملکرد اپراتور و غیره.
تحقیق مذکور نشان میدهد در صورت بهینه بودن مصرف انرژی، نسبت سرباره سازها، اکسیژن و غیره، بزرگترین عامل کاهش مصرف الکترود گرافیتی، کاهش زمان خاموشی کوره (Power Off) است. عامل دومی که در این تحقیق آمده، درجه آهنی شدن آهن اسفنجی (متالیزاسیون) است که البته اثر کمتری نسبت به زمان خاموشی کوره دارد اما هرچقدر بالاتر باشد به کاهش مصرف الکترود کمک مینماید.
دلیل اهمیت کنترل زمان خاموشی کوره آن است که با فرض بهینه بودن پارامترهای عملیاتی کوره قوس الکتریک، زمان خاموشی کوره به عنوان عامل مخرب در مصرف الکترود گرافیتی تا حد زیادی از نظر اپراتوری قابل کنترل است.
ریشه این تاثیر شگرف، به مکانیزم مصرف الکترود گرافیتی در کورههای قوس الکتریکی بر میگردد. مصرف الکترود گرافیتی به دو دلیل اتفاق میافتد: مصرف غیر پیوسته (شکل ۱) و مصرف پیوسته (شکل ۲).
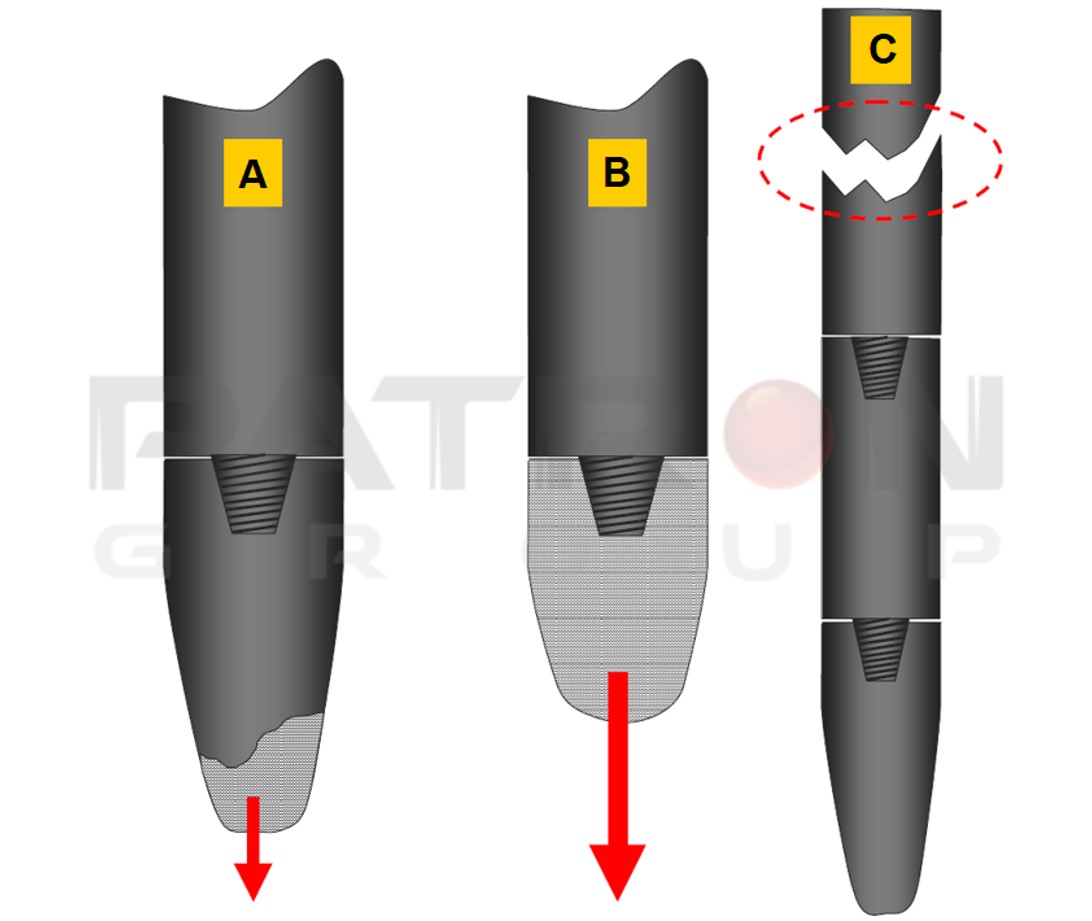
شکل ۱ مصرف غیرپیوسته الکترود گرافیتی
مصرف غیرپیوسته عمدتا به خاطر کندگی سر الکترود، افتادگی سر الکترود و شکست الکترود اتفاق میافتد که به خاطر سهم معمولا کم آنها در ضریب مصرف الکترود، در این مقاله به آنها نمیپردازیم.

شکل ۲ مصرف پیوسته الکترود گرافیتی
در مصرف پیوسته، مصرف نوک الکترود (A) به واسطه تصعید نوک الکترود، ناشی از دمای بالای نوک الکترود هنگام برقراری قوس رقم میخورد. این نوع مصرف تقریبا ۵۰% مصرف الکترود گرافیتی را تشکیل میدهد. همچنین اکسید شدن الکترود گرافیتی (B) منجر به مصرف آن میگردد که تقریبا ۵۰% دیگر مصرف الکترود گرافیتی را تشکیل میدهد.
اکسیداسیون سطحی الکترود گرافیتی در دماهای بالاتر از ۵۰۰ درجه سانتیگراد اتفاق میافتد. این در حالی است تقریبا تمامی طول الکترود از زیر سنتر (دلتا) تا نوک الکترود در هنگام کار کوره دمایی بالاتر از ۵۰۰ درجه سانتیگراد دارد و این بخش، که در شکل ۳ با نقطه چین آبی نشان داده شده، در معرض اکسیداسیون سطحی است. هنگامی که عملیات قوس متوقف میگردد و زمان خاموشی کوره آغاز میگردد، دمای مذکور به سرعت کاهش نمییابد، لذا بدون آنکه الکترود در نوک و جهت برقراری قوس الکتریکی مصرف گردد، از سطح آن اکسید میشود و ضریب مصرف الکترود افزایش مییابد.
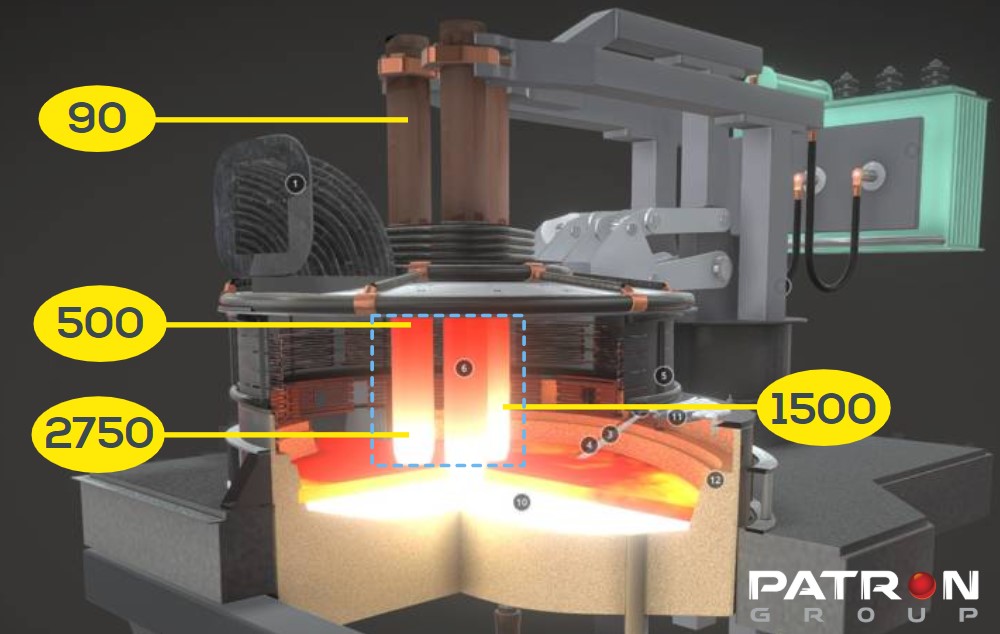
شکل ۳ دمای نقاط مختلف یک ستون الکترود گرافیتی در کوره قوس به سانتیگراد
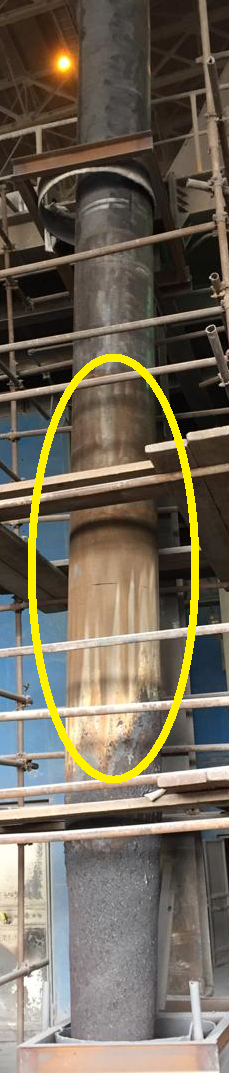
شکل ۴ آثار آب سیستم خنک کن الکترود گرافیتی
همین موضوع اهمیت دمای سطح الکترود گرافیتی را نشان میدهد. در تحقیقی که از آن نام برده شد، به دلیل نبود دادههای سیستم خنک کن الکترود، امکان مدلسازی وجود نداشت اما بدیهتا سیستم خنک کاری الکترود و اسپری رینگها نقش بسیار مهمی در کاهش مصرف الکترود گرافیتی دارند، هرچند متاسفانه در بسیاری از فولادسازیها مشاهده میگردد که تنظیم و نگهداری این قسمت به خوبی انجام نمیگیرد.
وجود آثار آب خنک کن بر روی الکترودهای برگشتی از کوره، نشانهای از عملکرد سیستم خنک کن الکترود است که در شکل ۴، با خط زرد رنگ نشان داده شده است.
الکوپات
الکوپات، پوشش الکترود گرافیتی گروه پاترون، نیز به منظور جلوگیری یا تعویق اکسیداسیون سطحی الکترود طراحی گردیده است. این نوآوری، با ترکیبات ویژه خود، ضمن تحمل دمایی بالا، نسبت به شوکهای مختلف مقاوم بوده و میتواند منجر به کاهش مصرف الکترود گرافیتی گردد.
خوشبختانه پس از یک سال و اندی مصرف الکوپات در کارخانجات مختلف فولادسازی کشور، عملکرد این پوشش، در عین ناباوری برخی متخصصین، به اثبات رسیده و منجر به صرفهجویی میلیاردها تومان هزینه در کشور گردیده است.
چنانچه در شکل ۵ نشان داده شده است، الکوپات با ایجاد لایهای محافظ، با کاهش مصرف سطحی، منجر به کاهش ضریب مصرف و به اصطلاح لاغر نشدن الکترود گرافیتی میگردد.
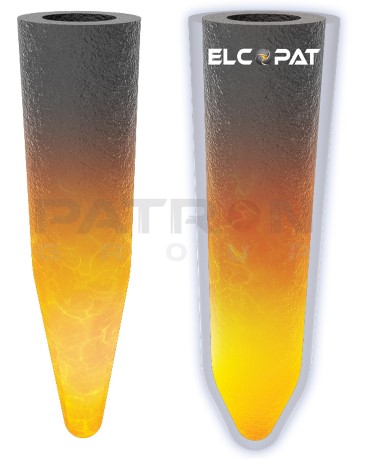
شکل ۵ شکل الکترود با الکوپات (سمت راست) و الکترود بدون الکوپات (سمت چپ)
لازم به ذکر است با وجود آنکه الکوپات در شرایط خاص منجر به کاهش ضریب مصرف تا حدود ۳۰% نیز شده است، به طور میانگین در کارخانجات مختلف بین ۱۵% تا ۲۰% از مصرف الکترود گرافیتی را کاسته است. حتی در کارخانهای در کشور ترکیه، که ضریب مصرف آن ۱/۱ کیلوگرم بر تن مذاب بوده است، الکوپات منجر به رسیدن ضریب مصرف به حدود نود و پنج صدم کیلوگرم بر تن مذاب شده است.
جمع بندی
در کنار بهینه سازی شرایط و رعایت نسبتهای اکسیژن، کک، سرباره سازها، تنظیم KT ها، جریان، ولتاژ، طول قوس و غیره، راهکارهای ساده و کارایی از جمله کاهش زمان خاموشی کوره (Power Off)، نگهداری مناسب سیستم خنک کن الکترود (اسپری رینگها) و نیز استفاده از الکوپات، میتواند منجر به کاهش ضریب مصرف الکترود گرافیتی به میزان قابل توجهی گردد.