تجزیه و تحلیل آسیب های سطحی و متالورژیکی در تیوب مسی پس از پایان عمر
این مقاله در مجله پردازش شماره ۱۲۸ و ۱۲۹، تیر و مرداد ۱۳۹۸ از صفحه ۱۱۰ تا صفحه ۱۱۲ منتشر شده است.
تجزیه و تحلیل آسیب های سطحی و متالورژیکی در تیوب مسی پس از پایان عمر
حسن بداغی-مدیر تحقیق و توسعه گروه پاترون
امیر حسین یوسف بیگی-کارشناس مهندسی فروش گروه پاترون
چکیده:
تیوب مسی یکی از اجزاء اصلی در فرآیند ریخته گری مداوم در تولید بیلت/بلوم/اسلب است. در تیوب مسی بواسطه عبور جریان مذاب، انتقال شار گرمایی بالایی از سطح داخلی که ذوب درون آن جریان دارد و سطح بیرونی که در حال خنک کاری توسط سیستم آبگرد قالب است، انجام می پذیرد. به واسطه این شار گرمایی، عبور مذاب با پوسته ی منجمد شده از درون تیوب مسی و تنش های مکانیکی و حرارتی وارد شده به آن، عمر تیوب مسی به عنوان یک عامل مهم در فولاد سازی مطرح بوده است. با توجه به اهمیت این موضوع در این مقاله به تجزیه و تحلیل آسیب های یک تیوب مسی پس از اتمام عمر آن می پردازیم. سپس به ارائه راهکارهایی برای کاهش میزان آسیب ها اشاره می کنیم.
مقدمه:
مهمترین قسمت ماشین ریخته گری مداوم، تیوب مسی می باشد. اهمیت اساسی تیوب مسی در بوجود آوردن پوسته منجمد شده با ضخامت و استحکامی مشخص است. انجماد اولیه فولاد مذاب در درون تیوب مسی انجام یافته و به منظور ایجاد حداکثر راندمان و انتقال حرارت مذاب، جنس تیوب از مس می باشد که مرتب در جریان انجماد مذاب توسط آب جداره خارجی خنک می گردد. موقعی که مذاب درون قالب برای شکل گیری و انجماد اولیه ریخته می شود مجموعه تبادل حرارتی مذاب می بایست به طریقی کنترل گردد که پوسته شمش در هنگام خروج از قالب دارای حداقل ضخامت لازم جهت تحمل نیروی فرواستاتیکی درونی مذاب باشد به طریقی که از پارگی شمش جلوگیری بعمل بیاورد.
تبادل حرارتی در سه ناحیه انجام می گیرد:
– تبادل حرارت تشعشعی که از طریق سطح مذاب درون تیوب مسی انجام می پذیرد.
– تبادل حرارت جابجایی که از طریق دیواره تیوب مسی با آب گردشی اطراف تیوب مسی انجام می پذیرد.
– تبادل حرارت مستقیم که در هنگام خروج شمش از تیوب مسی با آب اسپری و اتمسفر انجام می پذیرد.
تبادل حرارتی جابجایی در تیوب مسی که در طول آن انجام می پذیرد در قسمتهای فوقانی که ضخامت پوسته شمش حداقل و همچنین تماس پوسته با بدنه تیوب مسی برقرار بوده دارای بیشترین مقدار تبادل حرارتی و در قسمتهای تحتانی به علت افزایش ضخامت پوسته شمش و تشکیل فاصله هوایی، دارای کمترین مقدار تبادل حرارتی می باشد.
با توجه به شرایط کاری تیوب های مسی، این تیوب ها همواره در معرض تنش های حرارتی و مکانیکی می باشند. همین مساله منجر به ایجاد عیوب مکانیکی در تیوب مسی می شود که نهایتا بر روی ماشین ریخته گری پیوسته تاثیر گذار است. بدین صورت که منجر به پارگی خط یا ایجاد عیوب ظاهری یا درونی در بیلت/بلوم/اسلب می گردد. با توجه به اهمیت فراوان تیوب مسی در زنجیره ی تولید، عمر تیوب مسی به عنوان یک عامل تاثیر گذار در کیفیت و همچنین بهای تمام شده ی تولید محصول ریخته گری پیوسته مطرح است. به همین منظور در این مقاله به تحلیل آسیب های یک تیوب مسی پس از اتمام عمر آن و ارائه راهکارهایی برای کاهش میزان آسیب ها اشاره می کنیم.
روش تحقیق:
به منظور بررسی موضوع، یک عدد تیوب مسی کارکرده با عمر تقریبی ۵۰۰۰ تن که با آن فولاد گرید ساختمانی تولید شده است را پس از مشاهده ی عیوب ریخته گری در شمش تولیدی از مدار خارج کرده، مقطع های مختلفی از آن بریده و توسط میکروسکوپ الکترونی روبشی به تجزیه و تحلیل آنها می پردازیم.
همانطور که در شکل (۱-a) مشاهده می شود بررسی متالورژیکی توسط میکروسکوپ الکترونی روبشی (SEM) بر روی نمونه های مختلف استخراج شده از نواحی مختلف و مورد نظر برای مشخص کردن ریزساختار تیوب و تعیین مکانیزم ترک خوردگی ها انجام شده است. سطح داخلی تیوب مسی در شکل۱-b پس از پایان عمر قابل مشاهده است. قسمت (A1) را از ناحیه قوسی شکل تیوب مسی خارج کردیم. تعداد ۱۰ نمونه متالوگرافی از این ناحیه تهیه شد. ۴ نمونه نیز از نواحی که دچار آسیب دیدگی نشده بودند نیز گرفته شد (B,C,D,E) و برای آماده سازی جهت متالوگرافی بر روی هر یک از این نمونه ها و رسیدن به سطح مطلوب، عملیات سمباده زنی و پولیش با استفاده از محلول H2O:NH3:H2O2=1:1:1 انجام شد و پس از آن به بررسی ترک ها، ساختار شناسی و اندازه گیری دانه ها و میکرو ساختارها بوسیله میکروسکوپ پرداختیم. در برخی از نمونه ها از روش تجزیه و تحلیل SEM + EDXS برای بررسی منشاء رسوبات درون ترک ها استفاده شده است.
شکل۱- موقعیت نمونه های تیوب مسی مورد بازرسی(a)، سطح داخلی آسیب دیده (b)
تحلیل داده ها:
بررسی ها بیانگر آسیب شدید در ناحیه قوسی شکل تیوب مسی است. بازرسی صفحه داخل تیوب مسی، تشکیل ترک ها در محدوده تقریبی ۱۳۰ میلیمتری از بالای تیوب مسی و دقیقا در جایی که بیشترین حرارت را دارد نشان می دهد.
بررسی میکروساختاری نمونه هایی که از ناحیه قوسی شکل تیوب مسی استخراج شده است، نشان دهنده وجود بیشترین ترک ها در نمونه های A1، A1_1، A1_2، A3 و A4 است. این نمونه ها در نواحی دارای تنش شدید در تیوب مسی واقع شده اند. نمونه های A3 و A1-2 بیانگر آن است که ترک ها از این سطح آغاز شده اند و سپس به سمت دیواره تیوب مسی پخش و منتشر شده است. به نظر می رسد این ترک ها میان دانه ای در لایه هایی از رسوبات هستند که با استفاده از روش های SEM+EDXS بیشتر مورد بررسی قرار می گیرند. مشاهده می شود که در منطقه مرکزی ترک، پوشش اصلی کروم از بین رفته و احتمالا به دلیل فرسایش جدا شده است.
شکل ۲- ترک در نمونه (A3) و (A1-2)
ریزساختار این ماده از دانه بندی هم محور آستنیتی، از مس خالص تشکیل شده است. اندازه دانه مس درشت و در محدوده تقریبی ۷۰ ± ۳۰ میکرومتر است. این ابعاد در محدوده نرمال ریز ساختاری برای این کاربرد قرار دارد. به نظر می رسد که در سطح، این مواد به دلیل حضور دانه های نازک تر نسبت به اکثریت مواد تبلور مجدد شده اند. از فرایند تبلور مجدد را می توان با تولید پوشش سخت توسط فرآیند ماشینکاری دیواره داخلی تیوب مسی و درجه حرارت بالا جلوگیری کرد.
A04, 56±۲۴µm
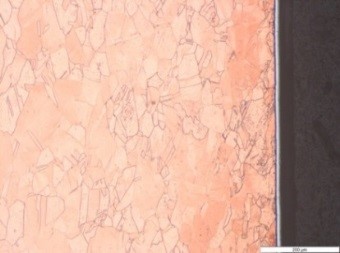
A01, 50±۲۰µm
شکل ۳- ریز ساختار نمونه های گرفته شده در گوشه ها
با توجه به نمونه هایی که از گوشه ها گرفته شده است فقط تعداد کمی از ترک های کوچک در (A04) قابل مشاهده است در حالی که هیچ ترکی در طرف مقابل (A01) قابل مشاهده نیست. برخی از نمونه ها یک پوشش جداگانه را ایجاد می کنند که ناشی از پوشش تیوب مسی است. در نمونه B1 و C1 ترک قابل مشاهده رویت نمی شود و پوشش کرومیتی با ضخامتی در حدود ۱۰۰ میکرومتر دارند (شکل ۴). در واقع، این نمونه ها خارج از منطقه قوسی شکل تیوب مسی استخراج شده اند، جایی که احتمالا تنش های حرارتی پایین تر است. در شکل ۵ تجزیه و تحلیل SEM انجام شده بر روی نمونه A1، حضور Pb، Zn و S را نشان می دهد. این عناصر احتمالا در فولاد مذاب وجود داشتند و به دلیل واکنش شیمیایی بالا به داخل مس نفوذ می کنند. ممکن است که این عناصر با مس واکنش داده و یک فاز ترد ایجاد کرده اند که باعث ایجاد و انتشار ترک شده است.
C1, 78±۲۶µm
B1, 94±۲۳µm
شکل ۴- ریز ساختار نمونه های B1 و C1
شکل ۵- طیف اشعه ایکس ناحیه آسیب دیده
تجزیه و تحلیل متالورژیکی ویژگی های لایه ترک ها را که بیانگر وجود خستگی حرارتی به عنوان عامل اصلی ترک است نشان می دهد.
این فرضیه با نتایج تجزیه و تحلیل عناصر محدود نیز تایید شده است (شکل ۶)، شبیه سازی رفتار دوره ای تیوب مسی، نشان دهنده مقادیر بحرانی تنش و کرنش در ناحیه ای است که در آن ترک ها ظاهر می شوند.
شکل ۶- توزیع استون فون میوز
تجزیه و تحلیل صدمات تیوب مسی در ماشین ریخته گری منجر به درک بهتر مکانیزم آسیب ها می شود. در ابتدا به علت فرآیند رسوب، پوشش کروم به طور طبیعی ترک می خورد و این ترکها به علت تنش های گرمایی ناشی از شرایط کاری تیوب مسی قابلیت انتشار دارد. علاوه بر این، دمای کاری بالا در تیوب مسی منجر به افزایش فرسایش کروم می شود. با ترک هایی که در سرتاسر ضخامت سطح نفوذ کرده است مذاب در تماس با مس باقی خواهد ماند و روی با مذاب پراکنده شده در سطح مس تشکیل یک آلیاژ برنج با مقدار بالای روی می دهد. هر دو پدیده تردی برنج و پدیده تبلور مجدد، دلیل نرم شدن مس و دلیل انتشار ترک است. آسیب مشاهده شده بسیار خطرناک است، زیرا می تواند ماشین ریخته گری مداوم را از بین ببرد. به همین دلیل باید از بالا رفتن میزان روی در مذاب جلوگیری کرد. با توجه به اینکه نمی توان از ترک خوردگی طبیعی کروم، تنش های حرارتی و فرسایش پوشش کروم اجتناب کرد.
ارائه راهکار:
بخش عمده ای از عیوب به دلیل عدم سرویس دوره ای تیوب مسی ایجاد می شوند. دفرمه شدن تیوب، فرسایش و سایش تیوب، از بین رفتن کوتینگ و نیز ایجاد رسوبات در پشت تیوب می تواند موجب آسیب فراوان به شمش و در مواردی پارگی خط شود. شعاع نا مناسب گوشه های تیوب مسی نیز می تواند عیوبی مانند ترک در گوشه های شمش ایجاد کند. در نتیجه، کنترل صحیح تیوب مسی و نیز بازدید دوره ای از آن می تواند احتمال ایجاد عیوب را به حداقل برساند.
تیوب مسی در طول فرایند ذوب بنا به کارکرد آن باید مورد بازرسی قرار گیرد. این سرویس ها شامل اسید شویی و تمیز کردن سطح بیرونی تیوب مسی جهت خنک سازی بهتر (شکل ۷)، تعویض اورینگ و سرویس قالب می باشد.
شکل ۷- سرویس دوره ای تیوب مسی
برای کاهش صدمات به تیوب مسی، راهکارهای متعددی وجود دارد که از جمله آن می توان به کنترل آنالیز ذوب برای جلوگیری از افزایش عناصر مخرب بر عمر تیوب مسی مانند روی، قلع و … که نقش مخربی در فرسایش و خوردگی لایه کروم دارند، اپراتوری مناسب، سرویس دوره ای تیوب مسی، استفاده از پودر قالب ریخته گری Casting Pat یا روغن های پایه گیاهی و … اشاره کرد.
پودر ریخته گری علاوه بر بحث روانکاری، نقش های عمده دیگری نیز بر عهده دارد که استفاده از آن، تقریبا در اکثر ریخته گری های باز و بسته به روغن ریخته گری ترجیح داده می شود. پودر ریخته گری با ایجاد پوششی از لایه زینتر و ذوب نشده روی سطح مذاب منجر به کاهش انتقال حرارت از سطح مذاب می گردد. زیر این پودر خام، مقداری پودر زینتر شده و مذاب وجود دارد که از تماس اتمسفر با مذاب جلوگیری می کند و در اصل نقش پوشاننده ذوب را نیز دارد. یکی دیگر از ویژگی های خاص پودر ریخته گری، ایجاد یک محیط مناسب برای جذب ناخالصی هاست. در اصل با ایجاد این لایه در سرباره مذاب، می توان به خارج شدن نا خالصی ها از مذاب کمک کرد. نکته دیگر در مورد پودر، قابلیت تطبیق فرمولاسیون آن با ترکیب شیمیایی فولاد، سرعت ریخته گری و دیگر متغیرهای ماشین ریخته گری مداوم است.
شکل. ۷٫ استفاده از Casting Pat در عملیات ریخته گری مداوم
پس از افزودن پودر ریخته گری به درون تیوب مسی چه می شود:
- با قرار گرفتن پودر روی مذاب، این لایه موجب جلوگیری از انتقال حرارت به وسیله تابش و همرفتی (هدایت) به علت حضور پودر زینتر شده روی آن میگردد.
- با قرار گرفتن پودر روی مذاب، میزان اکسیداسیون مذاب موجود در تیوب کمتر خواهد شد
- نسبت بازیسیتهی بالای این پودر ناخالصیهای مذاب را جذب میکند و این باعث می شود تا این پودر علاوه بر فولادهای ساختمانی برای فولادهای آلیاژی نیز مناسب باشد (خصوصاً برای شرایط ریخته گری بسته).
- روانکاری مداوم بین پوسته ی منجمد شده و دیواره قالب.
- انتقال حرارت یکنواخت بین پوسته ی منجمد شده و دیواره قالب.
- کاهش احتمال وجود حفرات ریز زیر سطحی (Pin Holes) در شمش نسبت به زمان استفاده از روغن ریخته گری
- بالا رفتن عمر تیوب مسی
- بالا رفتن کیفیت شمش تولیدی